Tribological properties indicate how plastics perform when in contact with mating materials under dynamic conditions. They refer to the frictional and abrasive wear characteristics of a material. However, the properties are not always provided on resin suppliers’ data sheets, and must be obtained by testing under conditions specific to the application.
Why are Tribological Properties Not Always Listed on Resin Data Sheets?
It can be difficult to find tribological data, especially for high-performance plastics. Major resin producers typically do not provide data sheet values for bearing and wear properties other than coefficient of friction. The possible combinations of variables that affect wear and load-bearing performance make it impractical to pinpoint test conditions that yield results of practical value.
Fortunately, there are standard tribological test methods, testing services and material processors with applications and materials experience that can guide engineers in evaluating bearing and wear plastics for their components.
What Are the Key Tribological Properties and Test Methods for Bearing and Wear Grade Plastics?
Engineers designing bearing and wear components focus on three principal tribological properties:
- Wear resistance
- Coefficient of friction (static and dynamic)
- PV and limiting PV
Testing procedures under ASTM D3702 and ISO 7148-2. detail how tests are conducted and how data can be used for material comparisons. ASTM D3702, for example, covers testing for all three tribological properties using a thrust washer apparatus (Figure 1).
Wear resistance:
PV and limiting PV:
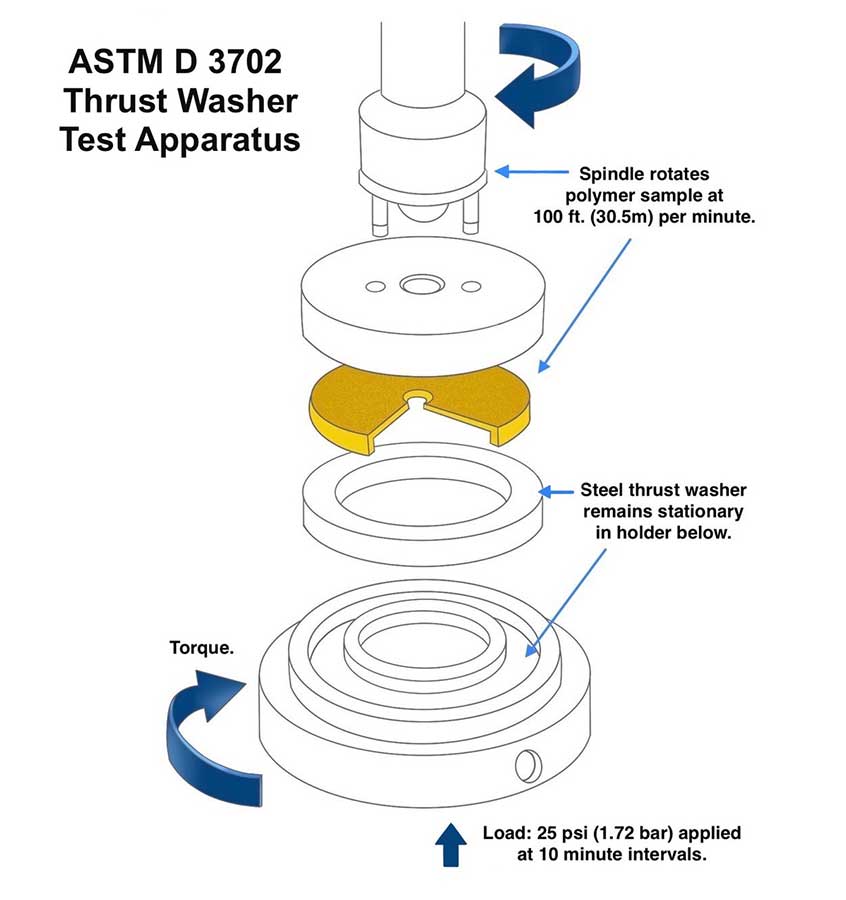
Pressure (P) and Velocity (V) are two key determinants of performance for a dynamic load-bearing component. P is the load on the component and measured in MPa or psi units; V is the velocity or speed at which the mating surfaces are in contact, measured in units of length over time; e.g., cm or feet / minute. This testing is typically done on a thrust washer set-up as shown in Figure 1.
- PV is calculated by multiplying Pressure x Velocity to which the material is exposed. The combination of these variables creates frictional heat at the mating surface of the sample. When the PV exceeds a material’s capability, the heat generated can cause failure of the load bearing component.
- Limiting PV defines the maximum PV that a material can withstand with no lubrication at the mating surfaces. When the actual PV that occurs under operating conditions exceeds the plastic’s Limiting PV, the material will likely fail due to surface melting or excessive wear.
Engineering note: It is standard engineering practice to utilize a safety factor for applying a plastic’s limiting PV to an application. This is done by dividing the test results by a safety factor of 4.
Coefficient of friction (COF):
This describes the resistance to sliding, either to initiate a component’s movement, or maintain it once in motion. Lower is better: the less resistance to movement, the greater the sliding capability.
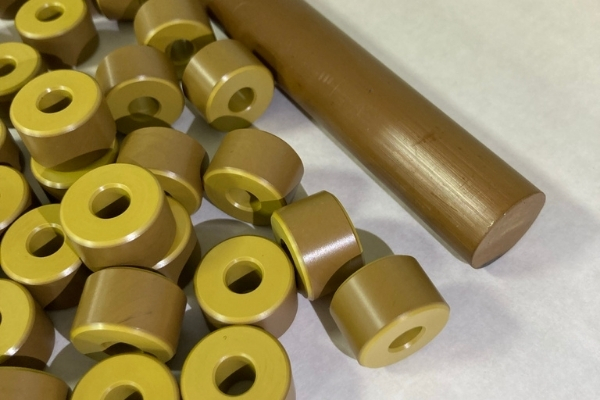
Coefficient of friction values can often be found in data sheets, and may be reported in two ways:
- Static COF: this defines material’s resistance to movement from a stand-still. It measures the ratio of forces to get movement started. It is not expressed in units of measure, because It is a ratio of two forces: the torque or force required to get the sample in motion, divided by the normal force applied to the material sample.
- Dynamic COF: this property measures the ratio of forces that sustain motion at a given speed. This is the most common form of data provided by material suppliers.
Note: Normally, it takes more force to set an object in motion from a stand-still than it does to keep it in motion. That means a plastic’s Static COF is usually higher than its Dynamic COF.
What other factors influence tribological performance?
In addition to physical load, velocity and temperature, these are some of the other factors that can influence the wear life of components:
- The operating environment.
- Type of physical load; e.g., constant, intermittent.
- Surface texture of the mating part.
- Chemicals that may soften or embrittle a material over time.
- Moisture or steam in the operating environment.
- How mating surfaces contact each other (e.g., sliding; rotating; point load).
-
The type of polymer.
-
- Semi-crystalline high-performance polymers such as PPS, PEEK and Torlon PAI have inherently good wear resistance.
- Amorphous materials like ABS and polycarbonate exhibit high wear rates.
-
Additives in polymer formulations.
-
- Lubricants such as PTFE and graphite can significantly improve bearing and wear performance even of semicrystalline polymers such as Torlon and PEEK.
- Carbon fibers provide bearing and wear resistance and more structural strength.
-
The processor’s expertise.
-
- High-performance plastics usually require a high melt process temperature to injection mold or extrude into shapes for machining. A capable processor will be able to analyze melt characteristics and precisely control process conditions to avoid degrading the polymer.
What Resources Can Help Identify Polymer Candidates for a Bearing and Wear Application
Material comparisons based on standard test procedures give engineers a good starting point for assessing different wear-resistant and load-bearing thermoplastics for their application.
A plastics stock shapes extruder, injection molder or precision machinist who specializes in high performance bearing and wear polymers can also be an asset. A capable company will have extensive experience in high-performance severe service applications in industries where long term reliability of components is essential. Their history will likely encompass applications similar to that which an engineer is developing.