Ultra High-Performance Polymers for Electrical and Electronic Applications
Electrical insulation, thermal isolation, and the ability to retain strength under load at high temperatures are major reasons why Torlon PAI, PEEK, Ultem PEI and Ryton PPS have gained acceptance for use in the diverse world of electrical and electronic devices and components. These versatile ultra high-performance polymers have proven their reliability under varied and extreme end-use conditions in components for the transportation, aerospace, aircraft, medical, defense, energy, and electronics manufacturing industries as well as many others. Even over the wide temperature swings common in these types of applications. For example, these high-performance polymers provide the dimensional stability required to maintain part tolerances critical to electrical connectors and other precision components. Depending on the actual application environment, specific polymers within Drake’s family of stock shapes and parts also eliminate corrosion and degradation in steam and chemical environments, which provide long and dependable service. And their inherent toughness is an asset in parts and components that must withstand routine impact, vibration and abuse during handling, installation, and in use- even in cold weather.
With their combination of physical properties, light weight and long-term reliability, Drake’s stock shapes and parts made from these ultra high-performance polymers have proven their value as replacements for many metals, glass formulations and ceramics in diverse electrical and electronics applications, from rugged high voltage downhole connectors to precision sensor housings.
Torlon PAI’s Dielectric Strength and Thermal Properties Afford Advantages in Extreme Conditions
Among polymers, Torlon PAI offers unique characteristics that solve design and performance problems often associated with connectors and insulators in electrical and electronic devices.
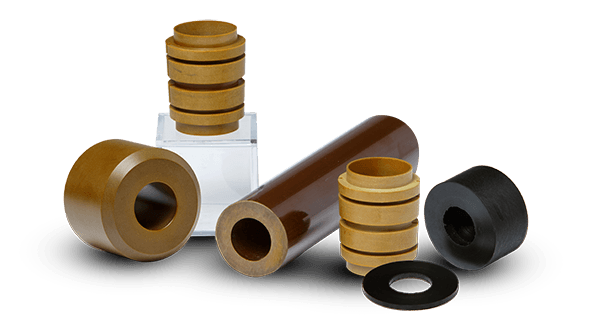
- Torlon PAI does not melt – When exposed to temperatures that would melt other polymers and cause parts to fail, Torlon PAI performs. Parts made from the material maintain their strength and mechanical integrity up to 260°C/ 500°F Even at higher temperatures, it still does not melt. Eventually it will char and smolder but will not ignite or support flame.
- Tough and light weight – In high temperature insulators, Torlon PAI provides the advantages of lighter weight and durability over glass, glass epoxy and ceramic. While these heavy, brittle materials are prone to damage in handling and use, Torlon PAI is literally hammer tough even in thin sections. The specific gravity of insulative Torlon grades 4203L (1.42 g/cm³) and Torlon 5030 (1.61 g/cm³) approaches only half the weight of traditional high temperature insulation materials.
- Dielectric strength –Torlon PAI functions extremely well as an insulating material because of its high dielectric strength. This is particularly true of Torlon 5030 and 4203L grades, which combine excellent dielectric strength with added toughness. Torlon also maintains its dielectric strength when exposed to both cryogenic and high temperatures, making it a reliable option for applications that must operate at these extremes.
- Thermal performance – No melt processable polymer maintains its strength at high temperatures as well as Torlon PAI. This has led to its specification for a wide variety of demanding applications that must perform long-term in extremely hot environments. Its thermal stability also makes the polymer a good choice for electrical and electronic components that are exposed to high temperatures in production processes, and in final testing phases for validating various components performance in actual application environments.Torlon PAI has a maximum operating temperature of 260°C / 500°F with an even higher glass transition temperature- 275°C / 527°F. Its low coefficient of linear thermal expansion supports precise part tolerances over wide temperature changes, and all grades are inherently flame resistant. Combined, these impressive thermal properties make Torlon the most thermally stable melt processable polymer available.
- Chemical resistance – Torlon PAI is highly resistant to many chemicals, including most hydrocarbons and acids. It is susceptible to saturated steam and some strong bases, but its chemical resistance profile is a good fit for electronics and semiconductor processing. Parts machined or injection molded from Torlon PAI must be properly cured after forming to achieve optimum chemical resistance.Drake utilizes its more than 30 post-cure ovens coupled with extensive experience in curing to achieve a consistently high Tg (glass-transition temperature) in Torlon PAI shapes and parts. Tg of this polymer advances with cure and serves as the typical measure of cure effectiveness.
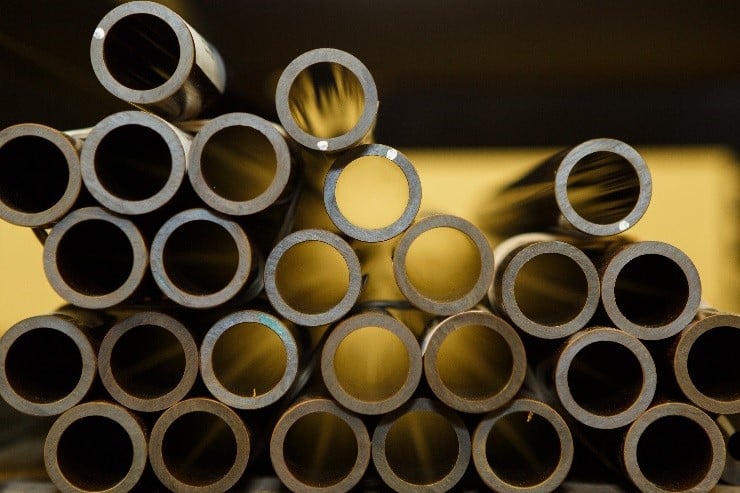
With its combined advantages of thermal, chemical, and electrical resistance, Torlon PAI is a common choice for numerous electronics applications including test sockets, chip contactors, probes insulators and ferrules. In these roles, Torlon PAI is not only long-lasting and resistant to mechanical stresses but is less likely to release ionic impurities compared to polyimides. Torlon 4200, in particular, exhibits minimal erosion when exposed to plasma gases and is a good choice for plasma chamber applications.
PEEK Offers High Dielectric Strength Plus Exceptional Chemical Resistance for Electrical and Electronics Components
Torlon PAI is the go-to option when a combination of extreme mechanical, temperature and electrical stresses are present. However, PEEK also offers its own unique combination of properties that make it ideal for a variety of electrical and electronic components and for parts used in the production of electronics. This high-performance polymer affords long-term operating reliability even in harsh chemicals over wide fluctuations in temperature, pressure and electrical frequency. Its applications include components and bodies for trimming potentiometers that calibrate and correct voltage or resistance errors in electronic devices after manufacturing, and electrical connector blocks and pin insulators in ESP pumps and subsea electrical gear and other extreme environments.
Key properties behind the selection of PEEK for these applications include:
- Dielectric strength comparable to vacuum conditions – While it would be ideal but not actually feasible to manufacture electronics in a vacuum, some materials including PEEK provide a good option. With dielectric strength like that of a high vacuum (200 uPa), PEEK is an excellent electrical insulator and therefore a good choice for materials handling applications used in electronics production and insulating components.
- Superior chemical resistance – PEEK’s chemical resistance exceeds that of almost all other polymers, including Torlon. It can maintain this broad chemical resistance at elevated temperatures up to nearly 204°C / 400°F, which has led to its use as a corrosion resistant material in many severe service applications.
- Thermal stability – With a Tg of 290° F/ 143°C and heat distortion temperature of 160°C / 320°F, PEEK withstands soldering temperatures in the production of electrical and electronic components. It also maintains its electrical and chemical properties at elevated temperatures, adding to its advantages for parts used in wet production processes.
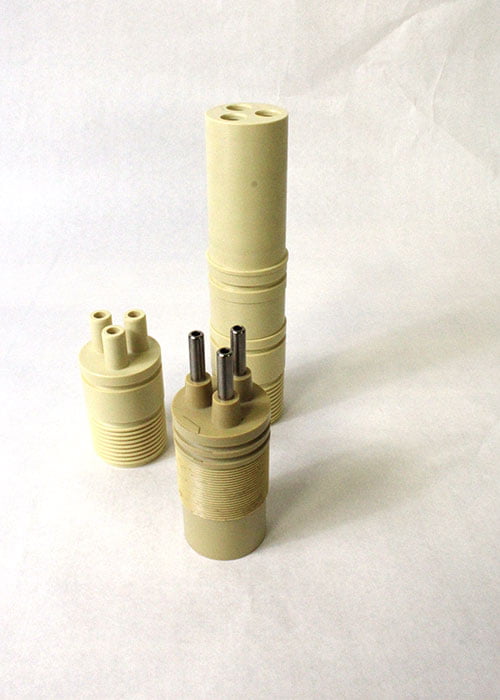
Ryton PPS, Ultem PEI and AvaSpire PAEK: High Performance Material Options for Electrical and Electronic Applications
Drake offers comprehensive range of ultra high-performance materials in stock shapes for machining and in molded parts, to provide engineers the most effective balance of cost and performance for their specific applications. In addition to Torlon PAI and PEEK, consider the unique performance profiles of these other polymers in the Drake line-up that are well-suited to many applications:
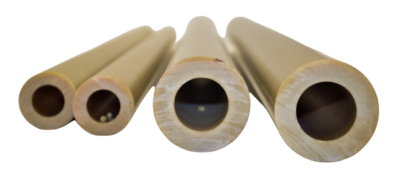
This versatile high-performance amorphous thermoplastic polymer is specified for a wide variety of electrical and electronic applications in the automotive, aerospace, telecommunications, and other industries. Typical uses include fiber-optics connectors, connector blocks, automotive lamp sockets and ignition components, insulators, metallized reflectors, and electrical enclosures.
Performance benefits supporting Ultem PEI’s use in electrical and electronic applications include its dielectric strength, a UL94 VTM-0 flammability rating, and broad chemical resistance. On thermal performance it has a 200°C / 392°F heat distortion temperature, retains its high mechanical strength at elevated temperatures and maintains its properties after long-term heat exposure.
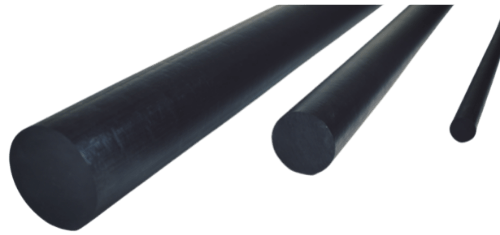
A semi-crystalline polymer, Ryton R-4 PPS is an excellent electrical insulator. Combined with its resistance to high temperatures and chemicals, its retention of insulating properties in high humidity makes Ryton R-4 a good choice for electrical and electronic components in automotive engine compartments and other severe service environments. Proven applications across many industries include insulators, connectors, sockets, bobbins, housings, switches and relays. Its use has grown rapidly, replacing lower performance materials as operating temperatures have risen due to the addition of many more electronic functions in the same or smaller-sized engine compartments and electrical equipment housings.
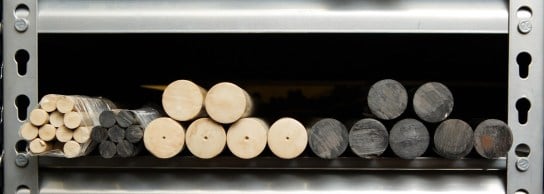
A hybrid PEEK polymer with a Tg of 158°C/ 316°F and heat distortion temperature of 217°C / 422°F, AvaSpire PAEK offers a valuable increase in thermal- mechanical performance over PEEK, with similar broad chemical and hydrolysis resistance. Depending on application requirements, its electrical and insulation properties can make it a good choice for capacitors, bobbins, switches, connectors, and sensor housings.
Process expertise: Critical to Material Performance for Electrical and Electronic Applications
Based on their physical properties, ultra high-performance Torlon, PEEK, Ryton PPS, Ultem PEI and AvaSpire PAEK polymers can satisfy the performance demands of a host of electrical and electronic applications even under the most severe service conditions. However, actual performance of components, and their performance consistency batch to batch, also depend on how these materials are processed.
Drake specializes in these ultra high-performance polymers. Their benefits should not be compromised. Our ongoing investments are focused on acquiring – and more often improving and developing – leading edge process technology and production methods exclusively for Torlon, PEEK, Ryton PPS, Ultem PEI and AvaSpire PAEK. Our customers have come to learn and trust that this degree of dedication and process expertise ensures stock shapes and molded and machined components provided by Drake consistently meet their expectations on performance and quality.
- Polymer-specific process technology: Each of these high-performance polymers has a different composition and structure. All vary in how well they tolerate process temperatures and machining methods. To maximize their individual performance benefits, each requires its own ideal production conditions. Understanding and dealing with fiber reinforcement orientation is also essential to achieving expected performance. For example, Torlon requires extended curing post-production to lock in its excellent strength, and we do not ship Torlon stock shapes or injection molded parts until they have undergone thorough post cure.With decades of experience exclusively in extruding stock shapes and molding and machining in these ultra high-performance polymers, Drake’s manufacturing team knows how to preserve each material’s performance and quality so that customers receive parts with the strength, durability, and performance they expect shipment after shipment.
- Versatile solutions: Our production engineers always choose the optimal process for every polymer we handle. Unlike many plastics processors, we are not locked into any one production method. Drake is invested and experienced in machining, injection molding and extrusion of high-performance polymers. Over the years, our customers have recognized that this versatility affords the best possible solution for their requirements.
- Client Satisfaction: For applications in high-performance polymers, every customer’s needs pose unique challenges. Drake collaborates actively with clients, very often at our site, to develop the optimum material, design and production solution. In some cases, we’ll provide additional prototyping to fine-tune components before full production can begin. Customers’ application requirements can also change with time, and they have learned that Drake adapts rapidly. We’re big enough to work with a variety of clients and handle large production runs, but small and flexible enough to act quickly as things change. Our customers validate this based on their years of ongoing relationships with us.
- Certification – Drake facilities and processes are certified, and we ship our products with certifications free of charge. ISO 9001:2015 certification, as well as AMS 3670 and ASTM D5204 are standard. Hamilton Sundstrand MS29.04, Boeing’s BMS 8269, Honeywell’s MCS 7004 and General Electric’s A50TF190 certifications are also available if required. Also, because we do not mix additives or substances during processing, we are compliant with al RoHS, REACH and California Prop 65 declarations made by resin suppliers
Torlon PAI, PEEK, Ryton PPS, Ultem PEI and AvaSpire PAEK high-performance polymers all can deliver exceptional performance benefits over metals, ceramics, and other traditional materials in a growing list of applications. Drake Plastics’ unique dedication to assisting with material selection and the optimum processing technology and conditions for each one assures that customers realize their optimal performance in every component.