Wafer Handling Tools, Fixtures, Hardware and Chamber Probes
Material choices for these applications are driven by concerns about contamination of nano-scale circuitry topography from particulates and from the negative effects of outgassing and chemical or plasma erosion of materials used. This is especially relevant for applications in vacuum chambers. The environment poses exceptionally severe process conditions and requires ultra high-performance polymers that withstand aggressive chemical and various plasma environments minimize the risk of off-gassing and particulate contamination. In many cases, wafer handling and fixturing applications must also maintain their stiffness and dimensions at high process temperatures. Performance demands are also increasing as the industry pursues new designs and increased productivity involving higher levels of plasma energy and more aggressive chemicals.
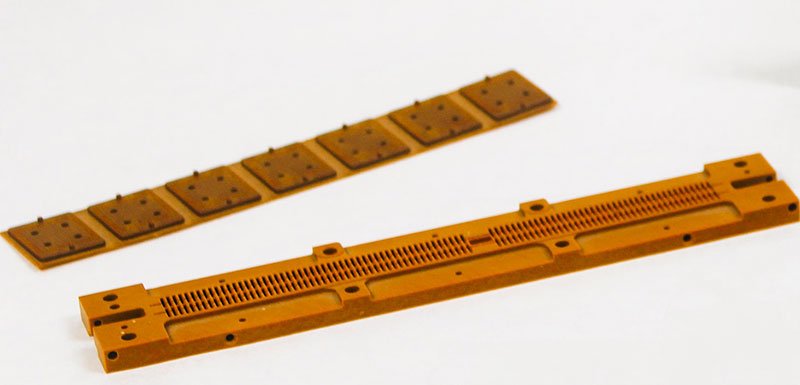
Drake offers a range of high-performance stock shapes for machined components that meet these requirements. They also offer advantages over other materials that may be considered. Compared to ceramics, for example, these ultra high-performance polymers are easier to machine and far more durable and resistant to breakage. Drake’s range of products also offers cost-effective performance options based on specific application requirements:
Torlon 4203L (also designated 4203), an unreinforced, TiO2 pigmented polyamide-imide, offers toughness and wear resistance. It has been used successfully for many years in wafer handling and chamber hardware including chamber probes.
Drake 4200 PAI was developed with zero TiO2 content. Similar to 4203L in physical performance, 4200 eliminates problems associated with the release of titanium dioxide particles during plasma etching that could contaminate the nano-scale topography of today’s micro circuitry.
Torlon 5030 reinforced with 30% glass fiber content is also used extensively in ferrules that must hold wafers steady during plasma etching. This material lasts longer than polyimides in the plasma environment, thereby releasing fewer ionic impurities into the chamber.
PEEK 450 CA30 and KT-820 CF30, both with 30% carbon fiber reinforcement, offer the highest strength and stiffness of all PEEK polymers. Inertness in a wide range of chemicals makes all PEEK grades a great fit for wet process use within semiconductor processing.
PEEK provides good chemical inertness in tools used to handle and fixture wafers during washing. It can also be used in applications that see temperatures up to 150°C. An advantage especially in semiconductor manufacturing, PEEK’s inherent purity minimizes ionic contamination from leaching when exposed to chemicals in production. PEEK also minimizes process contamination with its very low erosion in plasma gases.
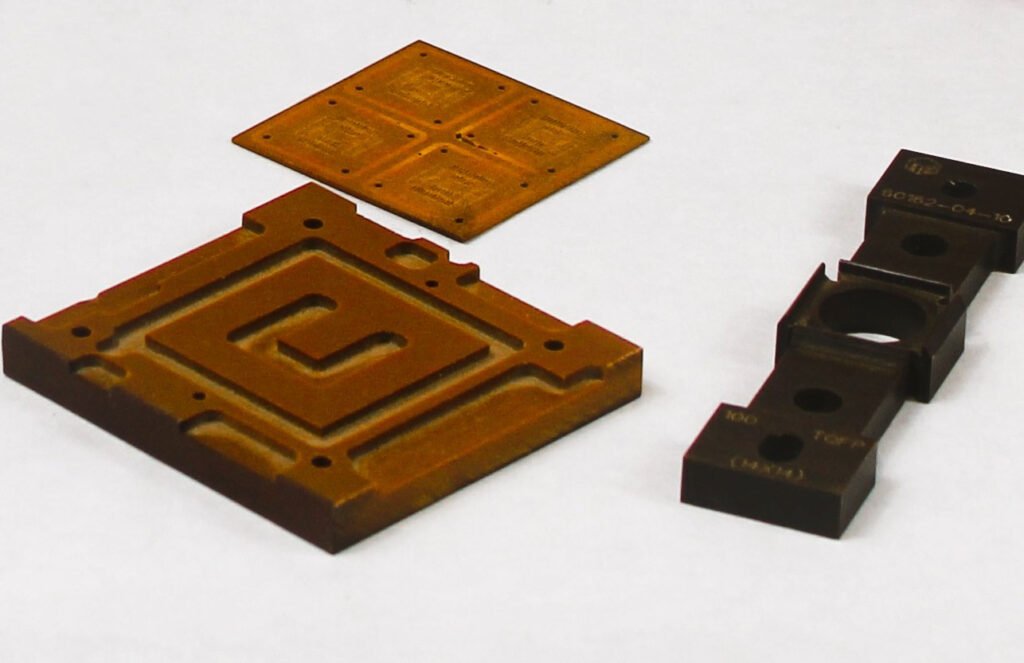
Contact Drake Plastics
"*" indicates required fields