Drake Plastics specializes in extruding, injection molding and machining ultra high-performance plastics. Our track record of successful application solutions with these materials spans more than two decades. Virtually all of what we do today in these materials originated with customers seeking solutions that others could not deliver or were unwilling to pursue.
Our ultra high-performance thermoplastics portfolio consists exclusively of materials characterized by a range of best-in-class properties. Among engineering thermoplastic materials, these high-performance polymers offer the highest levels of structural strength at elevated temperatures, the ability to withstand the broadest spectrum of aggressive chemicals, and exceptional resistance to wear and creep from high dynamic and static loads and stresses. Noteworthy properties of these high-performance plastics also include toughness at low temperature extremes, impressive resistance to radiation exposure, low thermal expansion and excellent flammability ratings and outstanding electrical and thermal insulative properties.
Our Materials
- Torlon PAI
- PEEK
- High-Temperature PEEK XT
- Victrex HT PEK
- AvaSpire PAEK
- Ryton R4 PPS
- Ultem 2300 PEI
These ultra high-performance plastics share another common trait: They are challenging materials to melt process via extrusion or injection molding. Deepening the processing challenges, carbon and glass fiber reinforced grades exhibit anisotropic behavior. Experience and expertise are required to understand, manage, and design for fiber orientation to optimize individual part performance. This applies to machined parts made from fiber reinforced extruded stock shapes as well as injection molded parts.
Drake has decades of experience processing the industry’s most difficult plastics, and an unmatched understanding of fiber flow and orientation.
Our technology team has been instrumental in developing processing parameters, designing and building innovative processing equipment and defining machining techniques precisely tuned to each of our ultra high-performance plastics. The result: customers around the globe call on us for shapes and parts with the maximum property levels these unique materials offer.
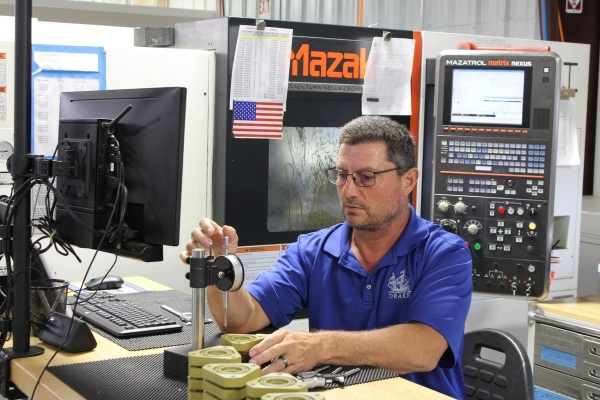
Industry Applications and Drake’s Material Selection Support
Application environments and operating conditions differ widely from industry to industry. Drake Plastics’ Development Team welcomes a collaborative approach with customers to help pinpoint the material grade and production technique best suited to each application. Our track record demonstrates our success in helping engineers and specifiers achieve the best balance of performance and production efficiency for countless applications in technology-driven industries including:
Polyamide-imide (PAI)
Compared to other engineering thermoplastics, PAI stands out as an ultra high-performance material that delivers unparalleled strength under load at high temperatures. Its structural strength remains high at temperature extremes due to its glass transition temperature (Tg) of 537°F (280°C). For those unfamiliar with Tg, it is the temperature at which a phase change occurs in plastic. The material transitions from a rigid form and enters a rubbery state. Above its Tg, the plastic begins to soften. Strength and stiffness fall rapidly, and thermal expansion increases dramatically. For a comparison to PAI, PTFE has a Tg near room temperature at 81°F (27°C) and PEEK Tg is typically reported at 289°F (143°C). Although the addition of glass or carbon fibers increase the strength and stiffness of a polymer along with its HDT (Heat Deflection Temperature), the host resin still dictates its Tg. Therefore, adding fiber to a base resin does not increase its Tg.
The superior compressive strength and creep resistance under high static loads place PAI in the top tier of engineering plastics for long-term structural integrity. Other notable benefits of polyamide-imide include its resistance to wear and the ability to withstand a wide range of chemicals and high levels of radiation exposure. Glass and carbon reinforced grades enhance the inherent strength of this ultra high-performance plastic material and bearing and wear formulations ramp up its long-term wear resistance. This combination of properties in a versatile range of formulations has led to numerous applications for polyamide-imide in extremely demanding end-use environments beyond the capabilities of other engineering plastics and many metals.
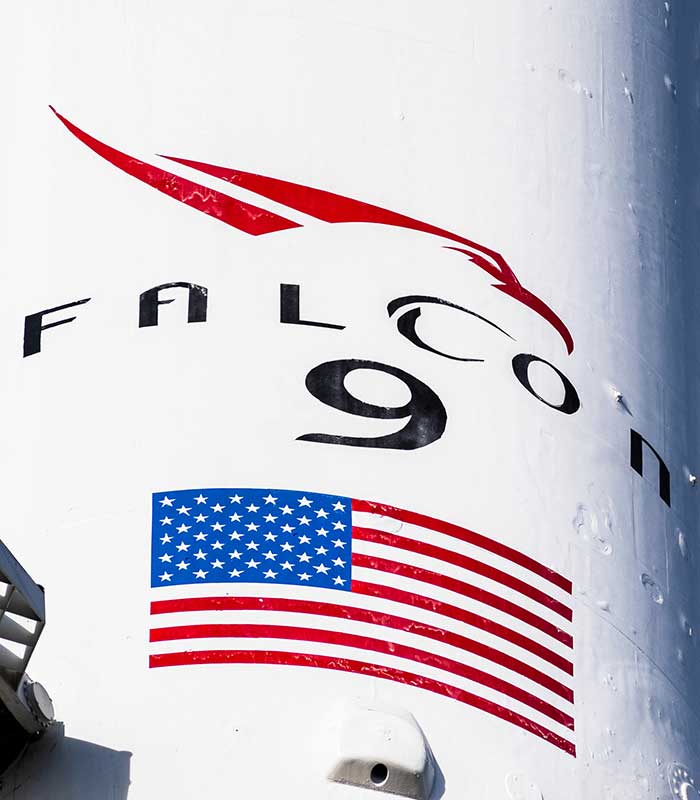
PAI Trade Names
is the most common commercial designation for PAI resins for injection molding and extrusion. A powder form is available for compression molding, but compression molded forms fall short of the properties of melt processed shapes and parts. Drake offers extruded PAI rod, plate and Seamless Tube® stock shapes made from commercially available Torlon resins under the Torlon PAI brand, and injection molded parts in all Torlon grades.
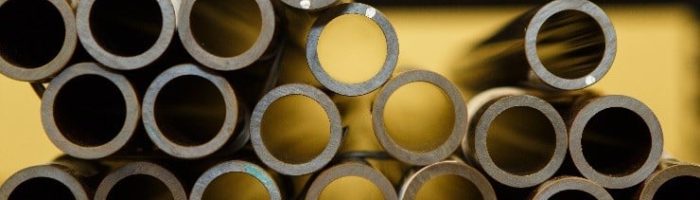
Some Drake polyamide-imide products are also designated as Drake PAI where commercial Torlon resin formulations necessary to produce specific grades or configurations our customers require are not available.
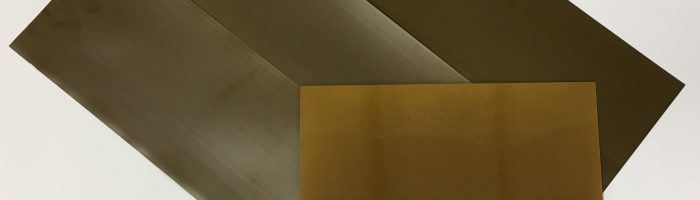
Commonly Requested PAI Technical Resources:
Polyetherketones (PEEK, High Temperature PEEK, PEK, PEKEKK, PAEK)
In addition to PEEK, the polyetherketone family includes PEK, PEKK, PEKKEK and PAEK. These polyetherketone polymers offer increased strength and high temperature performance over standard PEEK but lack the chemical and fatigue resistance of PEEK or High Temperature PEEK. This is because these polyketone variants lack the 2:1 ether (E) -to-ketone (K) ratio of the true PEEK polymers. The ratio is the basis of PEEK’s and High-Temperature PEEK’s superior chemical resistance compared to other polyetherketones. This and their relative ease of processing are the key reasons behind the far greater acceptance of PEEK polymer grades over alternate polyetherketone chemistries.
PEEK (Polyetheretherketone)
PEEK is recognized as one of the highest performing semi-crystalline polymers available.
In addition to fiber-reinforced and wear-enhanced grades of the traditional PEEK polymer, a High-Temperature PEEK grade is also available. It retains the chemical and wear resistance of standard PEEK and adds higher thermal performance, which improve elevated temperature mechanical and electrical properties.
Relative to other engineering plastics, standard PEEK offers an unmatched combination of chemical, wear and high temperature resistance. Its thermal properties include a Tg (glass transition temperature) of 289°F (143°C) and its non-fiber reinforced heat deflection temperature of 306°F (152°C). It retains its toughness at low temperatures. This ultra high-performance plastic material also ranks high on structural strength, and glass and carbon fiber-reinforced grades add greater rigidity and reduced thermal expansion. As a semicrystalline material, it has excellent fatigue resistance in addition to its exceptional ability to withstand a wide range of chemicals. PEEK also withstands exposure to high levels of radiation without serious degradation of its physical properties. Its low flammability characteristics and industry certifications make it a frequent choice for electrical, chemical and aerospace applications.
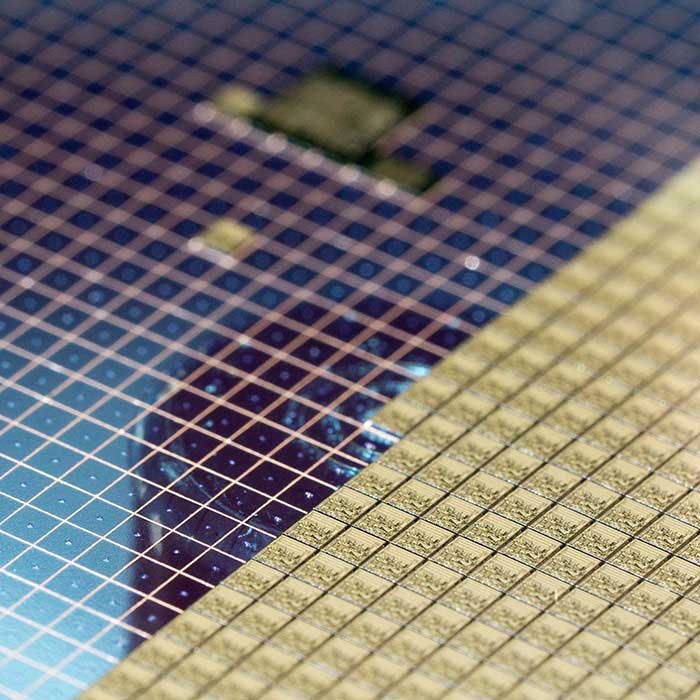
PEEK Trade Names
Victrex® PEEK; KetaSpire® PEEK:
Victrex plc and Solvay are the leading worldwide PEEK resin producers. They supply unreinforced, glass and carbon fiber-reinforced and wear-resistant grades under the Victrex PEEK and KetaSpire® PEEK brands respectively. Drake Plastics supplies PEEK stock shapes under these companies’ brands from 100% prime resin, so customers know exactly what they are getting.
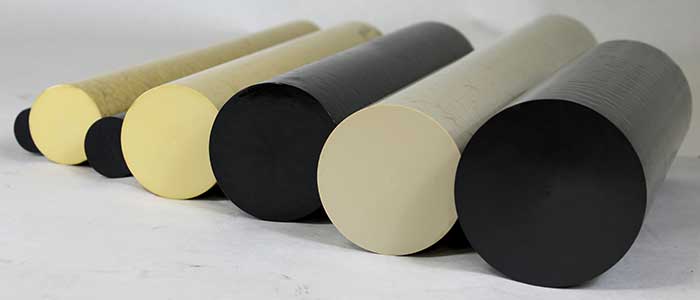
Drake supplies economy grade stock shapes designated as Drake Industrial Grade PEEK. We also offer precision-machined and injection molded parts in a wide variety of PEEK grades, and all products carry full traceability to the raw material used.
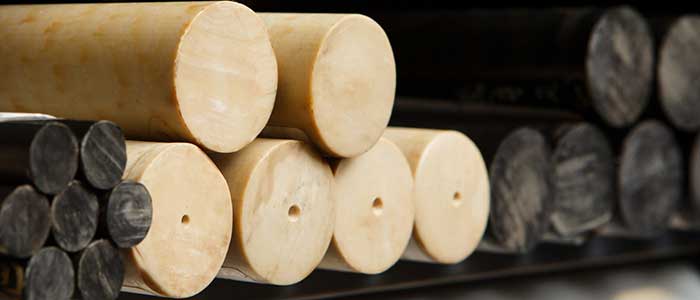
High Temperature PEEK (Polyetheretherketone)
Because it has the same polyetheretherketone (P-E-E-K) structure, the High Temperature grade of PEEK delivers the impressive chemical resistance of standard PEEK. As the designation indicates, it raises the performance of PEEK on temperature resistance, and also offers improved mechanical and electrical properties at high temperatures.
Compared to the standard grade, High Temperature PEEK has a 36°F (20°C) higher glass transition temperature of 338°F (170° C) and an 81°F (45°C) higher melting temperature.
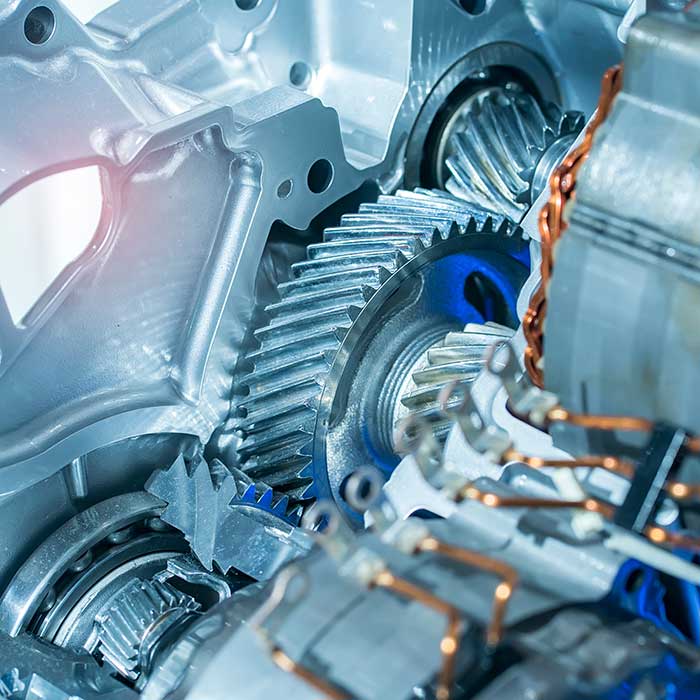
High Temperature PEEK Trade Names
KetaSpire® PEEK XT-920:
Solvay supplies injection molding and extrusion resin grades of High Temperature PEEK under the KetaSpire® PEEK brand with the designation XT-920. The product line includes an unreinforced grade and 30% carbon and 30% glass-reinforced grades designated KetaSpire PEEK XT-920 NT, XT-920 GF30, and XT-920 CF30. Initial applications are capitalizing on improvements in thermal performance and ablative properties over standard PEEK.
Drake Plastics injection molds parts from KetaSpire High Temperature PEEK and is developing stock shapes in unfilled XT-920 NT, glass fiber-reinforced XT-920 GF30 and carbon fiber-reinforced XT-920 CF30 grades under Solvay’s KetaSpire XT-920 brand.
Commonly Requested PEEK Technical Resources:
Polyetherketone (PEK)
Chemically a polyether ketone (PEK) polymer, Victrex supplies this high-performance plastic material for extrusion and injection molding. It has a higher glass-transition temperature (Tg) of 306°F (152°C) and more creep resistance than unfilled PEEK polymers and retains its strength at 54°F (30°C) higher temperatures. Drake Plastics extrudes the high viscosity G45 grade which allows large cross-sections with high impact resistance and ductility.
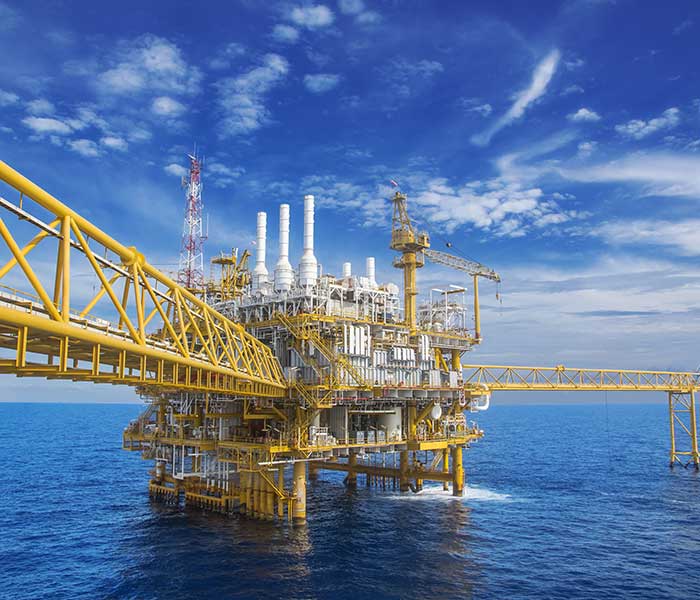
PEK Trade Names
Victrex® PEK HT:
Victrex supplies this ultra high-performance plastic with the designation Victrex PEK HT.
Drake Plastics offers standard shape products made from Victrex PEK HT G45 resin. Reinforced version of this material are available on a custom basis.
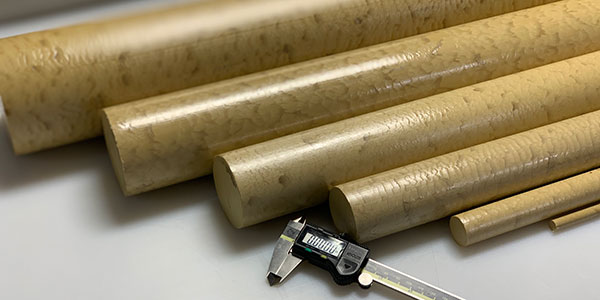
Commonly Requested PEK Technical Resources:
Polyaryletherketone (PAEK)
PAEK (polyaryletherketone) describes a family of advanced polymers. The version referenced throughout this website was commercialized by Solvay as AvaSpire PAEK. It offers more ductility and a 27°F (15°C) higher glass-transition temperature (Tg) than PEEK but with some compromises in chemical resistance. While its Tg of 316°F (158°C) is higher than PEEK, it is well below the 537°F (280°C) Tg of PAI. The ability of PAEK to retain stiffness over 300°F (150°C) and its impact strength can make it an economical alternative to PEEK depending on the operating conditions and chemical environment.
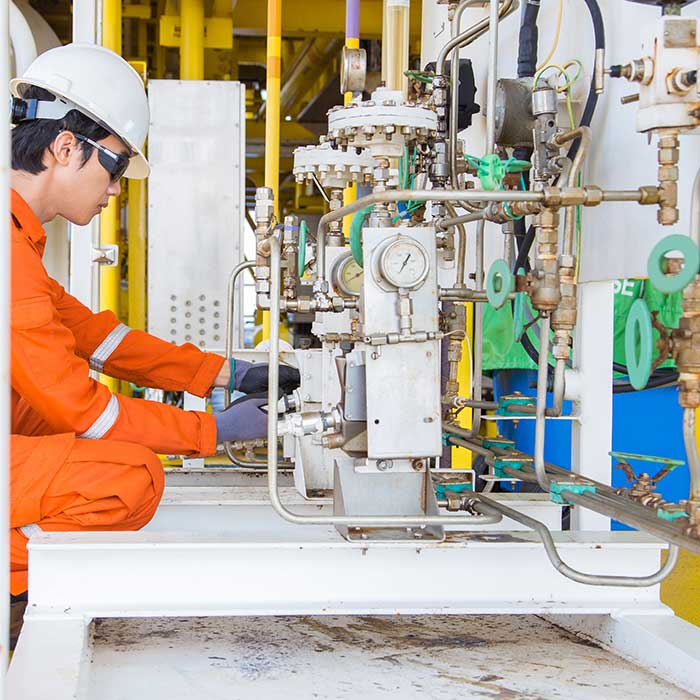
PAEK Trade Names
AvaSpire® PAEK:
Solvay offers this high-performance plastic material under the tradename AvaSpire® PAEK. Formulations include unreinforced and glass and carbon fiber reinforced grades. Drake Plastics offers stock shapes produced from all PAEK grades under the AvaSpire AV grade designations, and also supplies precision-machined and injection molded components made from the polymer.
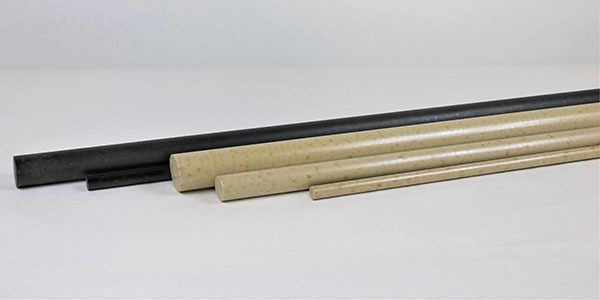
Commonly Requested PAEK Technical Resources:
Polyphenylene Sulfide (PPS)
Semi-crystalline PPS affords exceptional chemical resistance with no known solvents at temperatures below 392°F (200°C). For decades, unreinforced or neat PPS was used primarily for injection molded parts. The development of a 40% glass reinforced grade designated Ryton® R-4 increased the glass-transition temperature (Tg) of PPS to 190°F (88°C) and boosted its toughness and rigidity significantly. These elevated properties opened numerous specifications for the material in structural components for hot, aggressive chemical as well as demanding electrical environments.
Drake Plastics technology team’s development of process parameters to extrude 40% glass-reinforced PPS into machinable stock shapes expanded uses of this ultra high-performance thermoplastic into functional prototypes and precision machined parts that have low production volumes or heavy cross sections that cannot be molded reliably without cracks or porosity. Typical PPS applications include components in equipment for the oil and gas, aircraft electrical systems and chemical processing industries.
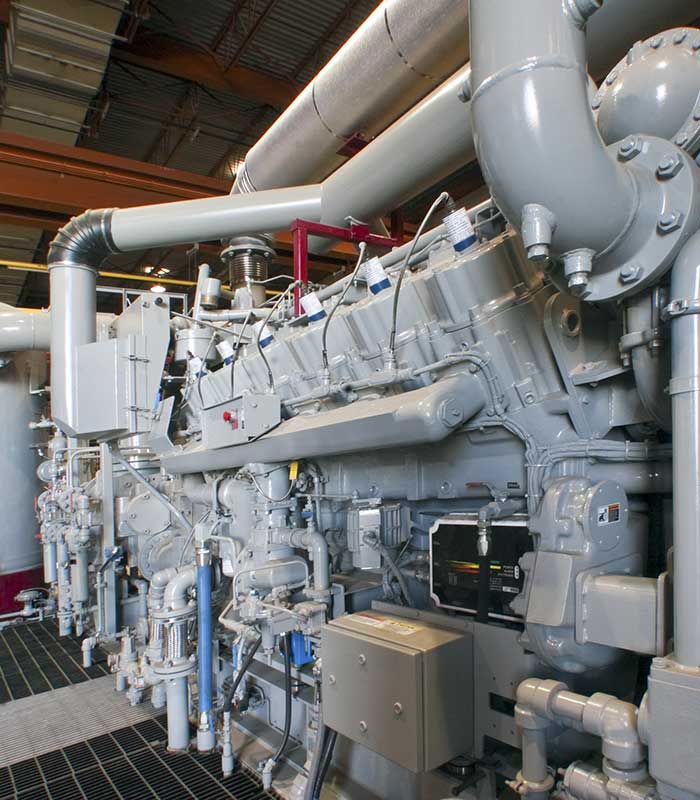
PPS Trade Names
Solvay supplies 40% glass-reinforced PPS with the trade name Ryton® R4-240 PPS. Drake converts the ultra high-performance thermoplastic resin into the industry’s widest range of machinable stock shapes under the designation Ryton® R-4 PPS.
Drake Plastics also supplies precision-machined and injection molded components made from this high-performance material. Solvay’s R4-240 resin has the highest molecular weight of among all the available PPS grades, indicative of a long polymer chain. This translates to optimum toughness which in turn improves stock shapes’ machinability and the performance of machined parts in demanding service environments. The properties of this 40% glass-reinforced high-performance plastic material often make it a lower-cost alternative to glass-reinforced PEEK and other high-performance plastics.
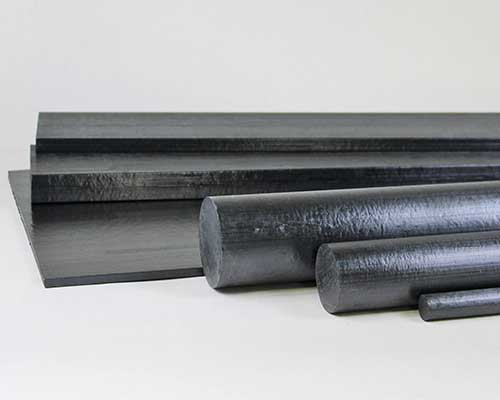
Commonly Requested PPS Technical Resources:
Polyether-Imide (PEI)
Polyether-imide is a member of the imide polymer family that includes polyamide-imide (PAI), another high-performance plastic material available from Drake Plastics. The high-performance thermoplastic withstands temperature extremes better than most engineering thermoplastics. It retains its rigidity at temperature extremes up to 390°F (200°C). Another notable feature of this high-performance plastic is its hydrolytic stability: its physical properties remain remarkably unaffected even when subjected to steam and long-term exposure to water.
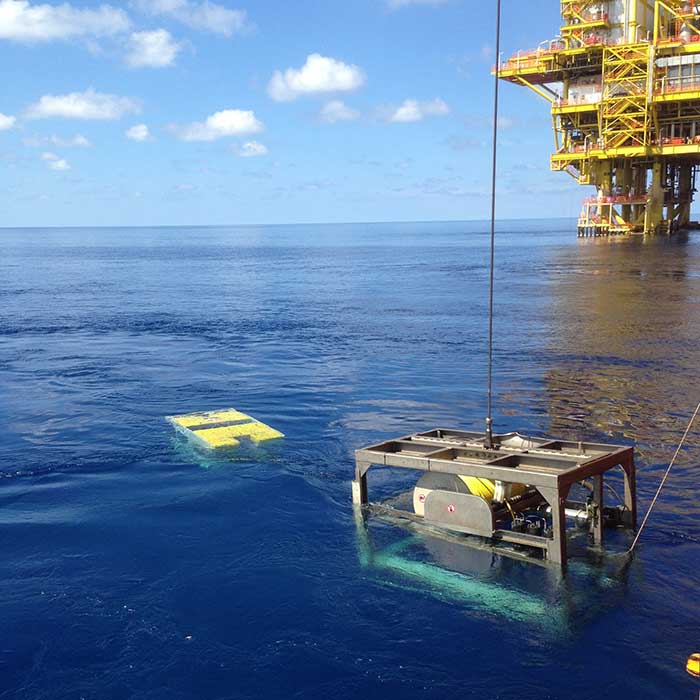
PEI Trade Names
Sabic is the primary producer of PEI and supplies the high-performance thermoplastic for injection molding and extrusion in several grades including fiber-reinforced formulations under the Ultem™ PEI brand name. Drake primarily extrudes 30% glass-reinforced Ultem 2300 PEI in Seamless Tube® configurations. A wide range of extruded tube sizes provides attractive economics for bobbins, insulators and other components that otherwise would be machined from rod or plate with far higher material waste.
Ultem 2300 PEI has a glass transition temperature (Tg) to 419°F (215°C) and is highly dimensionally stable with an in-flow coefficient of linear thermal expansion (CLTE) of 1.1 E-5/°F (1.98 E–5/°C), comparable to aircraft grade aluminum.
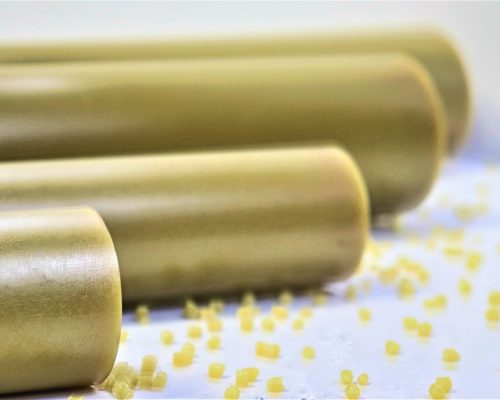