Semi-crystalline high-performance plastics such as PEEK and PPS as well as imidized amorphous polymers like Torlon polyamide-imide afford inherently good resistance to wear against mating surfaces under dynamic load. In addition, additives have been developed that enhance the load bearing and wear resistance of these and several other advanced polymers, such as Ultem polyether-imide. As a result, these plastics have replaced metals in many applications and provide the benefits of far longer service life, lower maintenance cost for repair and replacement, and greater productivity with fewer maintenance shutdowns.
Practical and widely used test methods give engineers a good basis for comparing the wear resistance of different plastics in the process of selecting materials for a specific application. The ASTM D3702 thrust washer test, for example, allows adjustments to the variables of speed and physical load to approximate actual conditions in use. However, the bearing and wear performance of a finished component when placed into service typically depends on several other variables as well.
What major factors affect bearing and wear performance of components?
Different polymers react differently to specific environments because of their distinct chemical make-up. The combination of environmental factors can also yield different effects on a material, and these factors can vary widely. These complex and variable operating factors reinforce the importance of testing under actual in-use conditions to validate the material candidates that are ultimately defined for each application.
Of course, it can be impractical to test many different materials and formulations in a component’s actual operating environment. To narrow the options, guidance is often available in resin suppliers’ data and design guides. In addition, an injection molder, machinable shapes extruder or machining company with an extensive history in high performance plastics and applications can help. Their practical know-how based on experience in polymers, special formulations and actual applications can help narrow the field to materials well-suited to performing reliably. They also will have close technical ties with major resin suppliers to facilitate customers’ access to the information required.
The following are major real-world variables that can impact performance and should be considered when evaluating bearing and wear resistant thermoplastics for specific applications:
Chemical exposure.
Certain chemicals can soften or embrittle specific materials. This can happen quickly, or take place over time, depending on chemical concentration and operating temperatures.
Each polymer has its own chemical resistance profile, and resin suppliers have the most in-depth information on their materials including the effect of chemical concentration and exposure times and temperatures. A components or extruded shapes supplier with experience in high performance polymers will have close ties with the major suppliers of these materials and can help customers get the specific information needed.
Moisture in the operating environment.
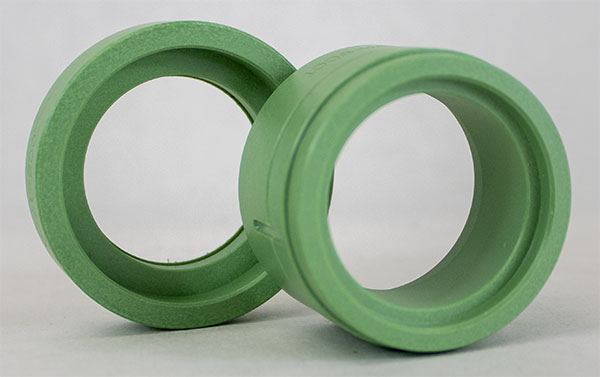
Operating temperatures.
Carbon fiber reinforcement of bearing and wear grades of polymers can have a significant effect on a material’s structural strength at elevated temperatures. However, a polymer’s inherent glass transition temperature (Tg) or the temperature at which it begins to soften is independent of additives and reinforcements, and should be factored into the selection of material candidates for an application.
Low temperature extremes can also impact the bearing and wear performance of materials for applications such as seals for cryogenic gas and liquid transfer. Not all materials perform well in these conditions. Fortunately, a cryogenic grade of PEEK has been developed for these types of components. In addition, Torlon PAI is available in bearing and wear formulations that do well in cryogenic temperatures.
The chemical structure of the polymer.
High-performance polymers with a semi-crystalline structure such as PPS and PEEK have inherently good bearing and wear properties as well as exceptional chemical resistance. Amorphous materials with an “imide” component in their polymer structure also exhibit good wear resistance. Torlon PAI (polyamide-imide) is a prime example, and its inherent wear resistance can be further improved by post-curing, as well as with additives such as carbon fiber and PTFE. Ultem PEI (polyether-imide) is another imidized amorphous material available in formulations with additives that significantly improve its wear resistance under dynamic load.
In general, however, amorphous polymers like polycarbonate and polysulfone exhibit high wear rates under dynamic load, and are usually ruled out for use in bearing and wear applications.
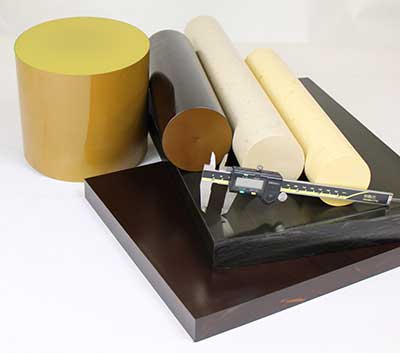
Lubricants and other formulation additives.
Adding lubricants such as PTFE and carbon fibers to a polymer can significantly improve the performance of bearing and wear-resistant polymers. Carbon fibers do as well, and also provide the added benefit of increased structural strength. Formulations with these additives are available with most bearing and wear polymer families.
External lubrication compatible with the polymer can also enhance wear life when required.
The process used to make shapes for machined parts.
Melt extrusion yields shapes with an even distribution of additives and a uniform overall composition because of the mixing that occurs with the melt. With compression molding, fibers and additives are mixed with a powder form of the polymer, and shapes for machining are formed under high pressure and temperatures. They are usually less uniform in composition than extruded shapes with additives distributed unevenly, resulting in inconsistent wear and load-bearing properties.
The plastic processor’s expertise.
High performance polymer components are typically made by injection molding or are machined from extruded shapes. Both injection molding and extrusion are melt processes, and high-performance plastics usually have a high temperature melt profile. An experienced processor will have capabilities to analyze the melt characteristics of polymer formulations, and monitor and control process conditions to avoid degrading the polymer and its properties.
Which high-performance polymers have inherently good tribological properties?
Torlon PAI, PEEK, PI and Ryton PPS have excellent overall property profiles and even without additives, they offer exceptional bearing and wear characteristics. Formulations with lubricants and additives that improve wear life are also available. Some bearing and wear grades are formulated with carbon fiber reinforcement that increases their structural strength.
What are the initial and long term costs of high performance polymers vs. metals?
What Are the Major Benefits of Bearing and Wear-Resistant High-Performance Plastics?
Optimizing a component’s performance by specifying the optimum wear-resistant and load bearing thermoplastic for the application environment can provide the following benefits:
Lower maintenance costs:
Wear-resistant plastics extend the life of equipment components. They can also eliminate the need for lubrication paths in dynamic mating parts. These factors add up to less maintenance and fewer replacements.
Greater productivity:
Extending the time span between scheduled maintenance shutdowns to replace worn components means more productivity.
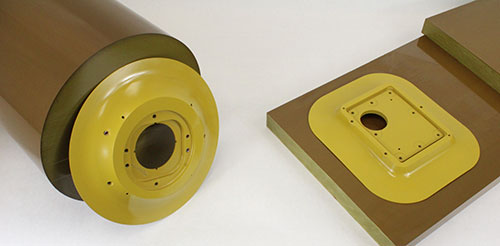
Enhanced efficiency:
Improving tribological properties means improving the operating efficiency of equipment. Less energy is lost as a result of friction.
Less risk of unplanned shutdowns:
Reliable operating performance and better predictability of maintenance and repair cycles reduces the risk of equipment failure that can shut down production.
Design versatility:
High-performance polymers like Torlon and PEEK combine excellent bearing and wear properties with toughness and resistance to chemicals and extreme temperatures. Within each of the polymer families, formulations are available that combine different levels of wear resistance, physical strength and thermal properties that open a wide range of application design options.