CYPRESS, TX–(Marketwired – March 07, 2017) – Drake Plastics is a leader in providing innovative plastic solutions to solve engineering challenges. Combining a love of cars with their passion for high performance polymers, Drake Plastics has announced a Race Team to facilitate the adoption of Torlon and PEEK components in the racing industry. Tyler Quance, Drake’s R&D Manager is leading the effort with a Mazda Miata equipped with a BP-4W, inline DOHC engine that he races on the NASA Texas circuit.
Background
Torlon’s pedigree in racing has long been publicized, but Torlon products have yet to become mainstream in the racing and performance markets. The automotive industry has adopted Torlon seal rings in many automatic transmission applications in North America and Europe with outstanding results.
In the 1980s, Amoco introduced Polimotor, an engine made with Torlon PAI components. Although it was more of a publicity endeavor, it ignited interest in the material. Torlon can provide strength and wear resistance for many demanding under hood and dynamic chassis applications. Drake’s ability to supply Torlon as machinable shapes or finished parts has helped many race teams maximize the performance of their vehicles.
Spec Miata is not Drake Plastics’ first foray with Torlon in the performance automotive industry. Drake has also worked with the Ferrari race team, Risi Competizione, who upgraded to Torlon 4435 suspension bushings supplied by Drake Plastics.
“The press-fit suspension bushings must withstand severe impact loading without fracturing, wearing or deforming,” said Steve Quance, president of Drake Plastics. Factory bushing materials required replacement between each race and according to Richard Taylor of the Risi Team, “Torlon PAI solved the problem.”
Torlon as Engine Bearings
Drake Racing’s first target is to replace traditional tri- or bi-metal engine bearings. These bearings are subjected to 4500 to 7200 rpms for hours while performing racetrack duty. Torlon 7130 is 30% CF reinforced. It was selected for this application because of its high compressive strength, high glass-transition temperature and minimal creep at elevated temperatures. Torlon 7130 also offers a coefficient of thermal expansion matching steel and a low coefficient of friction against polished metals, such as those in engine shaft journals. This is anticipated to effectively eliminate bearing wear upon engine startup, where engine oil pressure is momentarily unavailable to rotating components.
Drake’s flexible manufacturing capabilities will allow these prototype bearings to be machined from Seamless Tube™ stock material in small quantities, with injection molding available for higher future demand. Both processes can offer superior fiber alignment. After manufacture, these bearings are post-cured as a finished part, creating a cured skin that offers superior wear characteristics.
To follow the Drake Race Team please click to subscribe to the Drake Plastics Blog for updates.
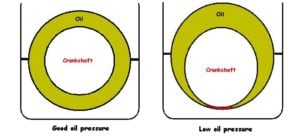
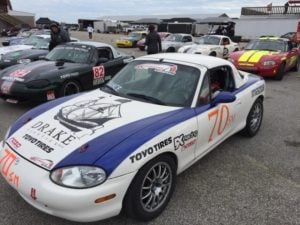