Drake’s research and development initiatives center on ultra high-performance polymers, and our work encompasses multiple areas of technology. The key one – and the backbone of our company – is melt process technology. Our focus is on developing ideal conditions for injection molding and extruding new stock shapes configurations from materials in our portfolio as well as new formulations of high-performance plastics. The goal: preserve the optimum properties of each polymer we process so that we not only deliver parts to print, but also deliver materials that perform to their fullest in those parts.
The Drake Engineering Team uses polymer science know-how, the latest CAD/CAM packages, simulation software, advanced automation & controls, mechanical design expertise, and years of ultra high-performance plastics processing experience to design, develop, and construct machinery and mold and die tooling unique to these materials. This specialized no-excuses equipment approach leads to processes that produce materials with optimized properties and unsurpassed quality. It also establishes process methodology for extruding new stock shape configurations that extend the application range of ultra high-performance plastics. Results include Drake’s unique Seamless Tube® and the world’s largest commercially available extruded rod diameters and plate thicknesses.
The Drake Plastics Engineering Team also works collaboratively with customers to develop their proprietary polymer formulations into stock shapes for their own uses. This often encompasses several capabilities that Drake has on-site. Turn-key projects can involve converting multiple polymer formulations, validating the performance of the materials in our thermo-mechanical test lab, and producing prototype parts in our precision CNC machining operation for customer evaluation.
Our work with customers also includes application development. We apply over two decades of experience to help optimize their part designs, match the optimum polymer and grade with the performance required under end-use conditions, and choose the right production method for each part.
In all cases, we measure success by making products that consistently deliver the full potential of each polymer’s properties at the highest possible level of quality and consistency.
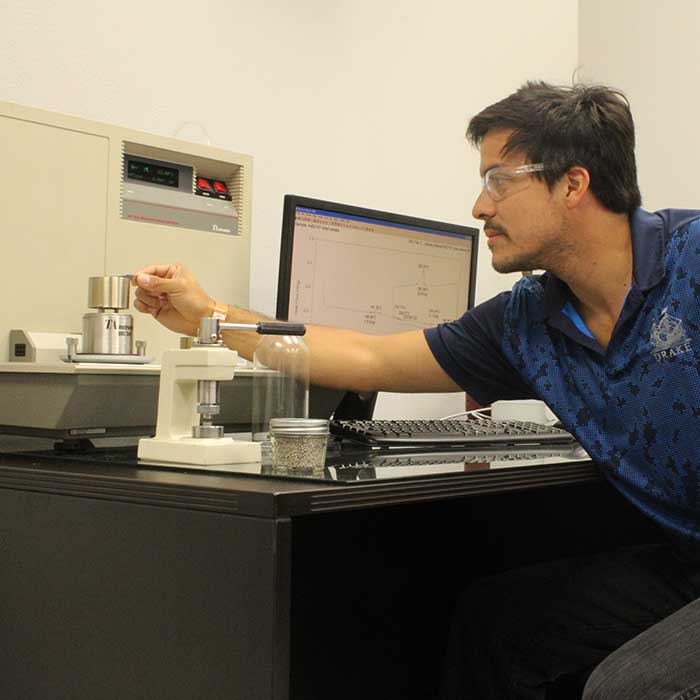
Extrusion: Breakthrough Technology Driven by Customer Requirements
Breakthroughs in technology and equipment design for extruding ultra high-performance thermoplastics characterize Drake’s history. Inventiveness does as well. The driver behind it all: every Drake shapes product stemmed from meeting needs and challenges posed by customers.
Over two decades of Drake technology “firsts” include the world’s largest rod diameters and plate thicknesses in Torlon PAI, PEEK and Ryton PPS. Since day one, our ongoing investment in development – all based on customer requests – has resulted in Drake’s offering the widest range of grades and efficient stock shapes sizes and configurations in all our ultra high-performance plastic materials.
Our technology team engages with customers to develop unique extruded products that extend the problem-solving potential of these high-performance polymers into entirely new areas. Drake PAI thin sheet and film, for example, now afford a uniquely hard, durable high-temperature and chemically resistant thin bondable substrate with exceptional wear and electrical properties without the expense of starting with thicker plate stock and milling it to the thin dimensions needed.
Drake’s continuing investment in development assures that our customers have access to the widest range of efficient stock shapes sizes and configurations in all our ultra high-performance plastic materials. In addition to development work, our major ongoing investments in extrusion capacity sustain our decades-long track record of dependable and responsive customer service.
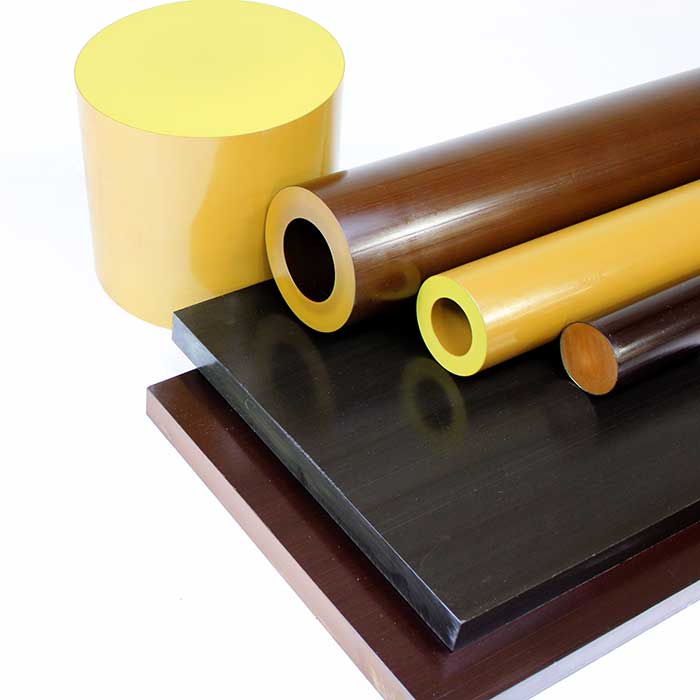
Seamless Tube®
An inventive approach to extruding tube led to the development of Drake’s unique Seamless Tube® made from Torlon® PAI and Ultem™ 2300. As its name implies, Drake extrudes tube in these ultra high-performance plastics with no seams, also termed weld lines. Weld lines are prone to cracking, porosity, and dimensional stability problems. In fact a weld line in PAI can have as little as half the strength of the homogeneous material surrounding it. The uniformity of the polymer throughout the tube also contributes to consistent performance of finished parts in use. Seamless Tube also delivers a substantial cost savings in high volume OD/ID part applications vs. machining the ID from rod by reducing material consumption, machining time and tooling wear.

Drake’s intense drive for lean production methods also led to the development of Seal Segments®. These unique extruded arcs are available to achieve any diameter over 16”/ 400 mm. Custom, unlimited sizes are available with very economical tooling thanks to Drake’s modular die design.
Seal Segments can be machined to the required finished tolerances for split seals and segmented seals and bearings. The resultant reduction in material loss cuts costs by 50% or more vs. making the same part from compression molded tube, and the savings is four-fold or greater compared to machining parts from plate. In addition, Drake provides Seal Segments in arcs that are over the required part length, so mating halves or segments can be made up quickly and easily. This eliminates the need to split compression molded tubes, pin and band the sections together and machine the entire assembly to a round configuration suitable for final machining of the finished parts.
Drake’s Seal Segments® are available in all grades of Torlon PAI and PEEK . Unlike compression molded tubes, Seal Segments are supplied with melt-processed properties and resin manufacturer certifications to AMS, ASTM and Mil-P standards.
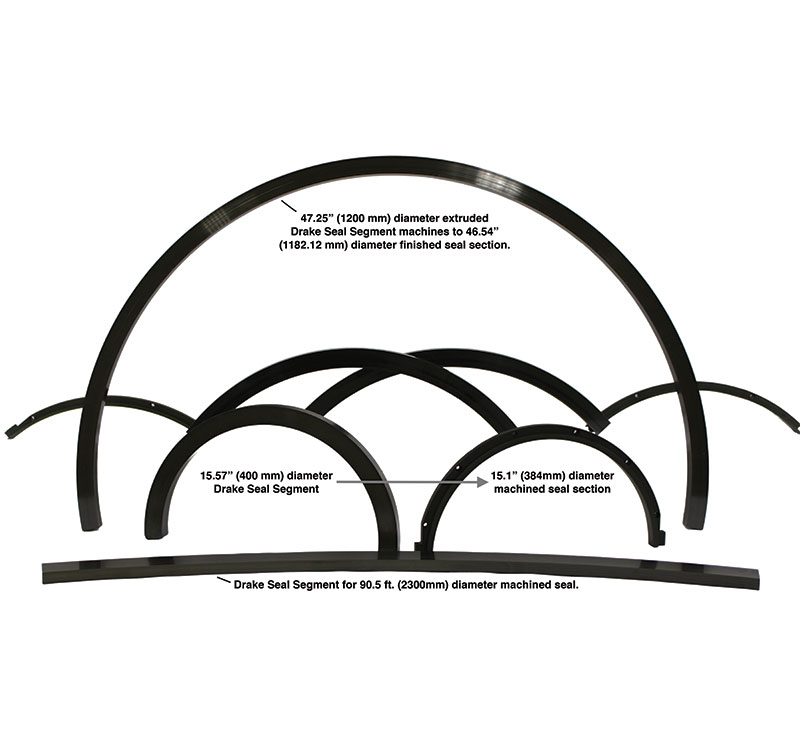
Custom shapes represent another customer-driven capability Drake offers. This includes shapes for high volume parts in sizes very close to final part dimensions. This improves efficiency and reduces material loss in machining. Drake also extrudes cost-effective custom lengths ideal for high volume screw machine applications. Some machines require nearly a linear foot (300mm) of chucking material, heavily impacting yield on standard meter length or 4-foot (1.22M) rod. To alleviate this significant material loss, Drake offers custom lengths up to 10ft. (3.0M) on request.
Drake also extrudes custom shapes for customers who provide their proprietary resin formulations and wish to offer their products in extruded shapes or machined parts for their own specialized requirements.
All of these custom services underpin our drive to support customers with products, sizes and services unavailable elsewhere in the extruded shapes manufacturing industry.
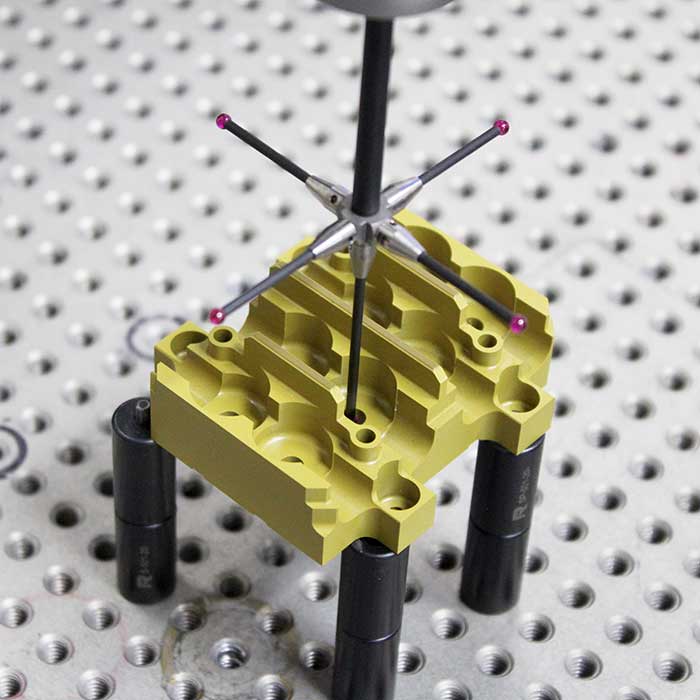
Drake’s precision-machining capabilities and expertise are fully dedicated to producing consistently high-quality parts from ultra high-performance plastics stock shapes. This includes Drake-produced shapes extruded from Torlon PAI, Victrex and KetaSpire PEEK including high-temperature XT-920 PEEK, Ultem PEI, AvaSpire PAEK, Ryton R4 PPS and Drake PAI, as well as Vespel, Meldin (PI), Celazole PBI and other ultra high-performance polymers.
Components machined from these ultra high-performance plastics must withstand extremely severe application environments long-term. Achieving maximum performance from each material and ensuring finished parts perform consistently depends heavily on processing and machining experience and expertise along with first-rate machinery in a controlled environment. Drake offers a uniquely high level of know-how in combining shapes production with precision machining. It’s based on decades of successful experience extruding then dissecting and analyzing shapes and developing techniques and methods for CNC-machining ultra high-performance plastics for customers around the world.
Engineers routinely work with Drake on the multiple related factors necessary to produce the optimum machined components. Our expertise in polymers and their properties, shapes and parts manufacturing, fiber-orientation, tolerances, surface finishes, and annealing and post cure operations, all come into play in maximizing performance of each component we machine.
Many applications also require prototypes to assure fit and finish and often to validate that materials and part designs perform under rigorous end-use conditions. Drake is committed to on-going investments in state-of-the-art 5-axis CNC machines and live-tool lathes to assure part quality and conformance and the capacity needed for the fast turn-around prototype parts often require, and dependable delivery of production parts regardless of where they are destined globally.
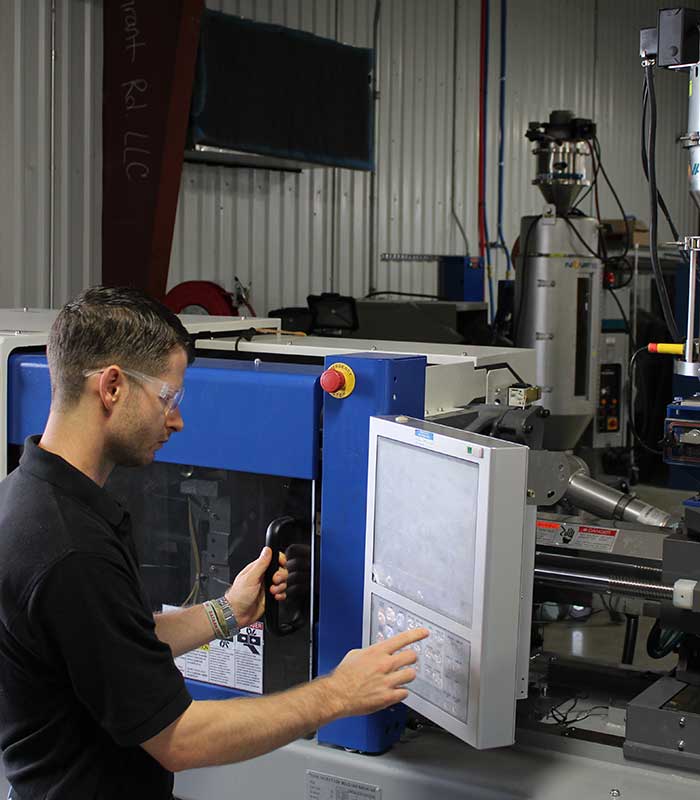
Melt-processing ultra high-performance plastics demands a solid understanding of each polymer’s behavior to achieve its optimum performance. This is particularly true for injection molding. High melt temperatures and mold cavity geometry and processing conditions have a dramatic effect on physical properties. Each polymer is also unique, and its melt stability, fiber-orientation and flow behavior have to be factored into process conditions and hardware.
We start each molding project by developing a thorough understanding of the customer’s part requirements and the performance expected from the specified resin. Next we employ a combination of experience, mold flow simulation software and FEA analysis to achieve a well-designed mold for the specific material , part design and production volumes. Then we construct the mold from specialty alloys for long and dependable life and back it with our Drake warranty, typically for 10 years.
To shorten the time it takes to build, maintain and repair injection molds, Drake has invested in our own mold-making shop in our Engineering department. In-house capabilities include precision grinding and machining as well as EDM capabilities for achieving fine details and finishes as required for injection mold cavities.
Drake Plastics brings unmatched expertise to this field, with over two decades of proven results in processing ultra high-performance polymers. Our injection molding experience spans an extensive range of formulations of Torlon® PAI, Victrex® and KetaSpire® PEEK, High Temperature XT-920 PEEK, Ryton® R4 PPS, AvaSpire® PAEK and Ultem™PEI. It also includes specialty high-performance polymer compounds from companies like RTP and Foster Corp. as well as customers’ proprietary formulations.
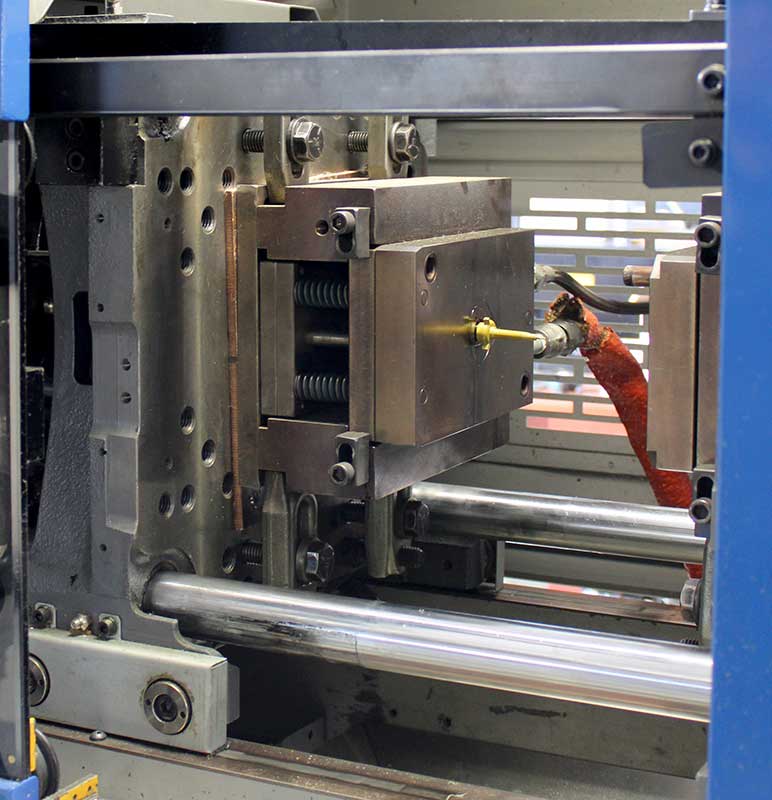
Our Toyo injection molding machines range from 35 to 300 tons provide a versatile range of precision-tolerance parts from .03 oz. to 20 oz. (0.85 to 570 grams). The all-electric machines are equipped with RJG’s eDART® System which monitors and controls in-cavity conditions to deliver highly consistent injection molded parts, shot to shot, run to run year after year.. By sizing barrels and screw profiles appropriate to each polymer, formulation, and shot size, our molding specialists minimize each material’s dwell time at high melt temperatures to avoid degradation and preserve its optimum properties in every part we mold. Our machines are also configured to allow compression coining of parts in the mold cavity after the injection step. This capability enables us to offer injection molded parts from ultra high-performance polymers with cross-sections up to 2.0”/ 50mm without cracks or porosity.
With injection molding and precision part machining capabilities both in-house, Drake can injection mold parts with tolerances or features that cannot be molded effectively but can be achieved by finish- machining after molding.
Also, Drake offers near-net injection molded shapes that can be finish-machined into parts with precise tolerances. This serves as a cost-effective step for customers whose machined part volumes increase to a level that allows investment in low-cost near-net shape tooling, but not a fully injection-molded part.
Drake’s unique competency in molding parts with zero draft and with heavy cross-sections, our ability to manage fiber orientation, and our insert molding capabilities complement our ability to consistently deliver parts molded from ultra high-performance thermoplastics at the highest levels of quality and performance attainable.
Custom Finishing and Sizing Capabilities
Backing up Drake’s primary capabilities are the secondary operations we’ve added in response to customer requests. These services provide solutions when products require precise production-ready custom sizes, more exacting dimensions and tolerances, exceptionally fine surface finishes, or any combination of these capabilities.
Drake provides labor and yield-saving blanks cut from our sheet or plate. This service eliminates saw-cutting and allows our customers’ machinists to focus on high-value work. From complex near-net blanks to simple shapes such as circles, squares, or rectangles we have you covered. These shapes are cut with a narrow kerf (0.03”/.0762 mm), high positional accuracy (.003”/.0762 mm) and CNC repeatability. At 50,000 PSI/ (345 MPa), Drake’s waterjet has the ability to cut shapes up to 4.0”/ 100 mm thick.
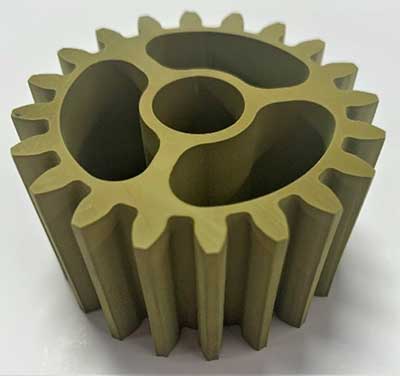
Precision Lapping & Polishing
Drake Plastics’ new double sided lapping equipment uses CNC controls to lap blanks efficiently and accurately. Our operation is capable of precision lapping and polishing part surfaces that are flat and parallel to tight thickness and finish requirements. The size capability for blanks or parts covers rod diameters up to 8.0 inches (203mm), and pieces up to 6.25 inches (158.75mm) square.
Typical parts where these operations are beneficial include:
- Parts that need extreme flatness and parallelism with polished surface finishes
- Burn-in sockets, nests and contactor blanks used in the semiconductor industry from materials such as Torlon 5030 and 4203 PAI, Ceramic filled PEEK, Vespel SP-1 and others
- Valves and components used in HPLC (High Performance Liquid Chromatography)
- Compressor valve plates
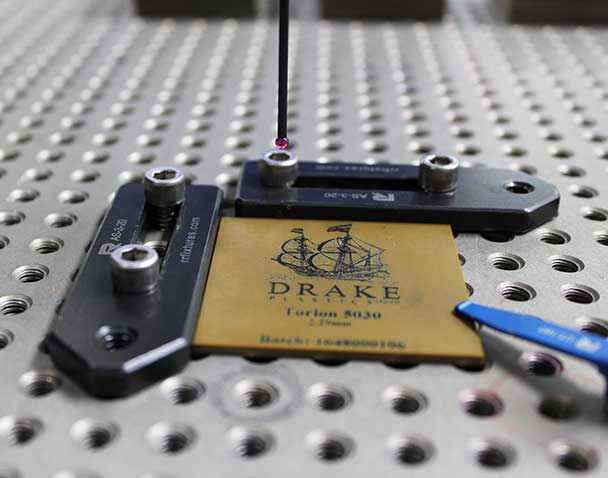
Centerless Grinding
Drake provides centerless ground rod for its customers’ CNC swiss screw machining operations or for collet work-holding or for customers who need long, cylindrical part ODs ground to precise sizes and finishes. Our centerless grinding capability ranges from 0.125 to 2.0-inch (3.0 to 50mm) diameter rod.
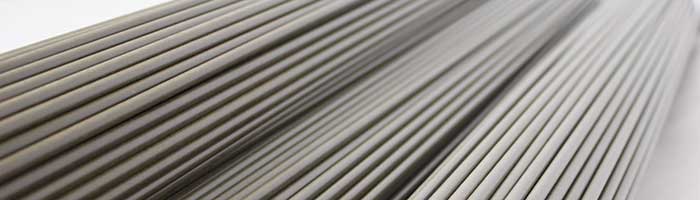