Aircraft and spacecraft applications place truly unique demands on materials. Drake Plastics’ ultra high-performance polymers have proven their ability to provide solutions to these extraordinary challenges.
Aircraft Applications for Ultra High-Performance Polymer Materials
Among all industries, aircraft has one of the most diverse and complex arrays of component parts and systems. The operating environments that aircraft materials have to withstand differ just as dramatically. Regardless of the component or system, reliability is paramount, and light weight and space-efficient design are ever-present priorities.
Operating conditions include exposure to jet fuels, de-icing chemicals and lubricants. Extreme temperature changes, high stresses and bearing loads and the need for thermal insulation and electrical insulation and EMI/RFI transparency- or shielding- are among the many challenges of specifying the optimal material for aircraft components.
These performance criteria for the precision designs of aircraft components represent an ideal backdrop for Drake’s ultra high-performance polymer products. Among plastics for aircraft applications, our Torlon PAI, PEEK, Ryton R-4 PPS, Ultem PEI and AvaSpire PAEK materials provide aircraft engineers superior physical properties in different combinations to satisfy the performance requirements of a diverse range of components. All of these polymer materials afford unique levels of mechanical strength and temperature resistance, chemical resistance, bearing and wear performance, thermal isolation and electrical insulation properties to meet exacting requirements effectively and efficiently.
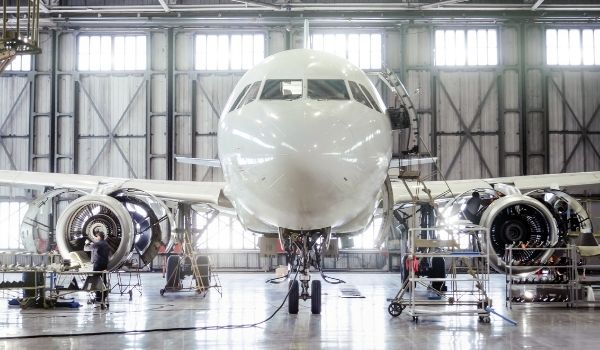
In aerostructure applications, Torlon PAI and PEEK provide the high strength and thermal isolation for dependable performance in reinforcements for composite panels including hard points, thermal isolators and fasteners. Bearing and wear components also capitalize on the wear resistant grades of ultra high-performance polymers for strength, long life and precision operation.
As an example, blocker door bushings made from Torlon PAI demonstrate how this ultra high-performance polymer performs in critical aircraft components under extreme temperature and load-bearing conditions. Blocker doors create the reverse thrust that slows jet aircraft during landing. The bushings attached to the door hinge assembly play a key role in the precise operation of these doors. Torlon 4301 PAI measured up to the demands. The bushings made from this PAI grade maintain their strength and stability at temperatures ranging from -40° to 500°F (-40° to 260°C), and they exhibit low friction wear while running without lubrication.
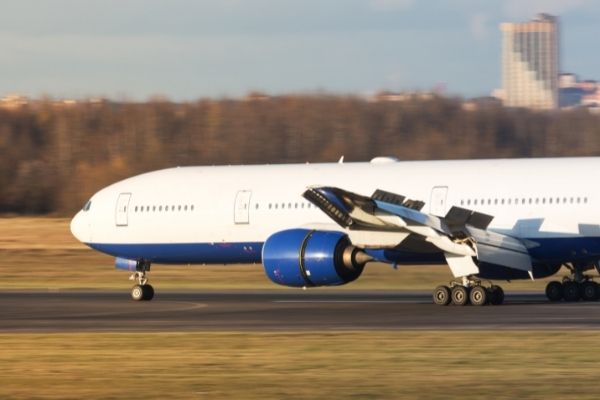
Components used in actuators and controls, thermal and power management, sensors, cable protection and other systems and support applications rely on Drake’s high-performance polymers for a different mix of properties. This is also the case in cabin interior applications for seating, chilling systems, oxygen systems, lighting, vacuum waste systems and cargo handling equipment. Torlon PAI, Ultem PEI and PEEK couple light weight and strength at high temperatures with dimensional stability and thermal and electrical isolation and insulation necessary for these precision parts.
In propulsion system components, Torlon PAI and PEEK combine exceptional chemical resistance and high strength with the added benefit of weight reduction, a pervasive goal in aircraft design. Their application versatility can also contribute to innovative system designs that reduce weight and cost.
Boeing engineers, for example, determined that running hydraulic lines through fuel tanks instead of around them would provide a substantial weight reduction in their composite aircraft. The challenge was that the hydraulic lines had to be insulated with a material capable of withstanding punishing amounts of thermal and electrical energy. Torlon 4203 PAI provided the solution. Its extremely low thermal conductivity isolates thermal energy between the bulkhead and the composite. It also prevents electrical arcing and maintains its strength at the temperatures the applications demanded -40° to 350°F (-40° to 177°C).
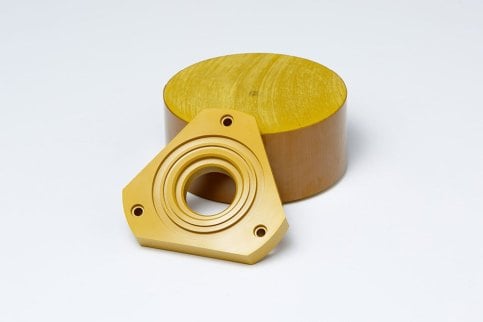
Drake Plastics is a recognized specialist in ultra high-performance polymers. Our decades of collaborative experience has helped engineers develop material selection and parts production solutions to numerous aircraft application challenges such as these.
Typical Applications of Drake’s Ultra High-Performance Polymers In Aircraft
- Insulators and isolators in Torlon 4203, PEEK, and glass-reinforced Torlon 5030, GF PEEK and Ryton R-4 PPS afford excellent electrical barrier properties. The unreinforced Torlon PAI and PEEK grades offer the lowest thermal conductivity for optimum thermal isolation.
- Sector gears in injection molded Torlon 4203 flawlessly move inlet guide vanes in gas turbines
- Battery connectors in 30% glass-reinforced PEEK provide electrical isolation in propulsion systems
- Blocker door bushings in Torlon 4301 survive high loads and excursions to 500°F and resist wear with no lubrication
- Screws in Torlon 4203 provide high strength, EMI/RFI transparency and reduced weight vs. metallic fasteners
- External light housings in fiber-reinforced Torlon PAI and PEEK maintain dimensions at temperature extremes and resist damage from fuel spills and de-icers.
- Fuel and air connects machined from Torlon 4203 Seamless Tube® extend the flying range of fighter jets
- Terminal blocks made from glass-reinforced Ultem 2300 have the dimensional stability and electrical properties needed for reliability in on-board generators
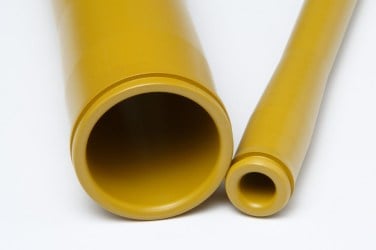
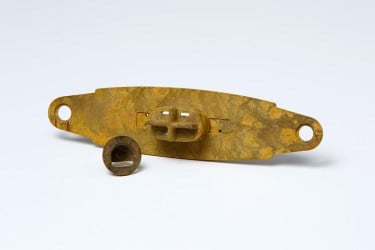
Ultra High-Performance Polymer Materials in Spacecraft
Manned and unmanned spacecraft capitalize on many of the same properties that have made Drake Plastics’ ultra-high-performance polymers a proven choice in aircraft. But while some performance factors are common, some come into play at more intense levels and others are completely unique to spacecraft. These include extreme cold, the effects of zero gravity and the potential for vacuum outgassing, sudden severe transitions from high to low temperatures, exotic propellants and chemicals, and higher stresses, vibration and loads. Torlon PAI and PEEK both measure up to these performance challenges for materials applications in satellites and manned and unmanned space vehicles.
Radiation levels in space are another key consideration related to the long-term performance of polymers in these applications. While many materials embrittle, Torlon PAI, PEEK and Ultem PEI are proven to have far greater resistance to property degradation even at high levels of radiation exposure.
This was confirmed in a report from the American Composites Manufacturing Learning Center in tests they conducted to determine how radiation might degrade the physical properties of a comprehensive group of thermoplastics. The tests were done at exposure levels from 103 to 109 rads. High strength Torlon 5030 PAI, a 30% glass-reinforced polymer extruded into shapes and machined into parts by Drake Plastics, retained the required level of mechanical properties to pass testing satisfactorily at 109 rads, the highest level of exposure in the testing procedures. Victrex PEEK, another polymer converted by Drake Plastics into high performance stock shapes and machined and molded parts, also passed at 109 rads. 30% glass-reinforced Ultem 2300 PEI which Drake supplies in its unique and efficient machinable Seamless Tube® configurations, demonstrated impressive property retention at 108rads.
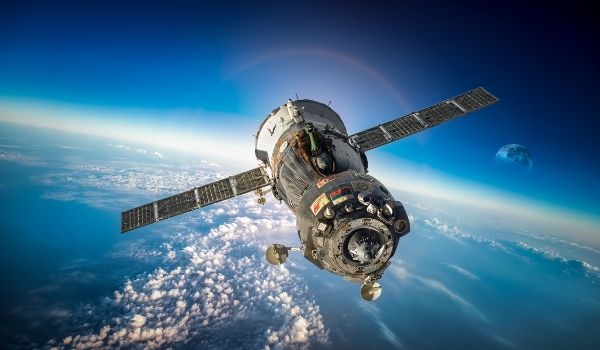
Another significant advantage of Torlon PAI and PEEK over many other polymers for spacecraft applications is their alleviation of concerns regarding vacuum outgassing in zero-gravity environments. Based on thorough testing, specific grades of both these polymers qualify as low-outgassing materials with TML (Total Mass Loss) levels that measure below 1% and a CVCM (Collected Volatile Condensable Material) of less than 0.1%. Thermoplastic materials with these low levels are especially important in many critical aerospace applications to prevent contamination caused by outgassing in high vacuum environments. NASA includes the select grades of Torlon PAI and PEEK and the specifics on their test results on its list of low-outgassing materials that the agency maintains for applications in spacecraft.
Another compelling factor behind the use of Torlon PAI and PEEK in aerospace applications is their ability to retain their toughness and ductility at the cryogenic temperatures that critical components experience in this environment. Given the risk of accidental impact in the restricted workspaces and the cold temperature extremes and zero gravity conditions of space, the resistance to breakage is high on the list of performance priorities for materials used in components, tools, liquid and gas lines, couplings and other applications.
With their growing list of application successes, Torlon PAI, PEEK, Ryton R-4 PPS, high temperature PEEK HT and Ultem PEI are proving their value as light weight and dependable high-performance materials for spacecraft components. Drake Plastics’ comprehensive family of light weight polymer materials provides engineers with the ability to choose the optimal combination of strength, stability, bearing and wear properties and chemical and temperature resistance best suited to their application requirements. In particular, the toughness of Torlon PAI and PEEK polymers at cryogenic temperatures, coupled with their low outgassing qualities and resistance to property degradation from exposure to high levels of radiation, has already made them the preferred materials for a wide variety of aerospace components.
Typical Applications of Drake’s Ultra High-Performance Materials in Spacecraft
- Sector gears in high strength, dimensionally stable Torlon 7130 deploy satellite solar arrays
- Insulators and isolators in Torlon 4203 and PEEK serve as excellent thermal and electrical barriers
- Mounting hardware in Torlon PAI and PEEK secure everything from antennas to windows and fluid and gas piping and insulation panels
- Fasteners and screws in Torlon 4203 resist degradation from radiation exposure, maintain high strength and are lighter weight compared to those made from metals.
- Satellite hardware components in Ultem PEI provide high strength and EMI/RFI shielding
- Wear shims in bearing grades of PEEK and Torlon PAI maintain functionality in orbiting satellite propulsion systems
- Oxidizer valve seals and bushings on rocket engines rely on the chemical resistance, strength and dimensional stability of Torlon 4301 under extreme conditions