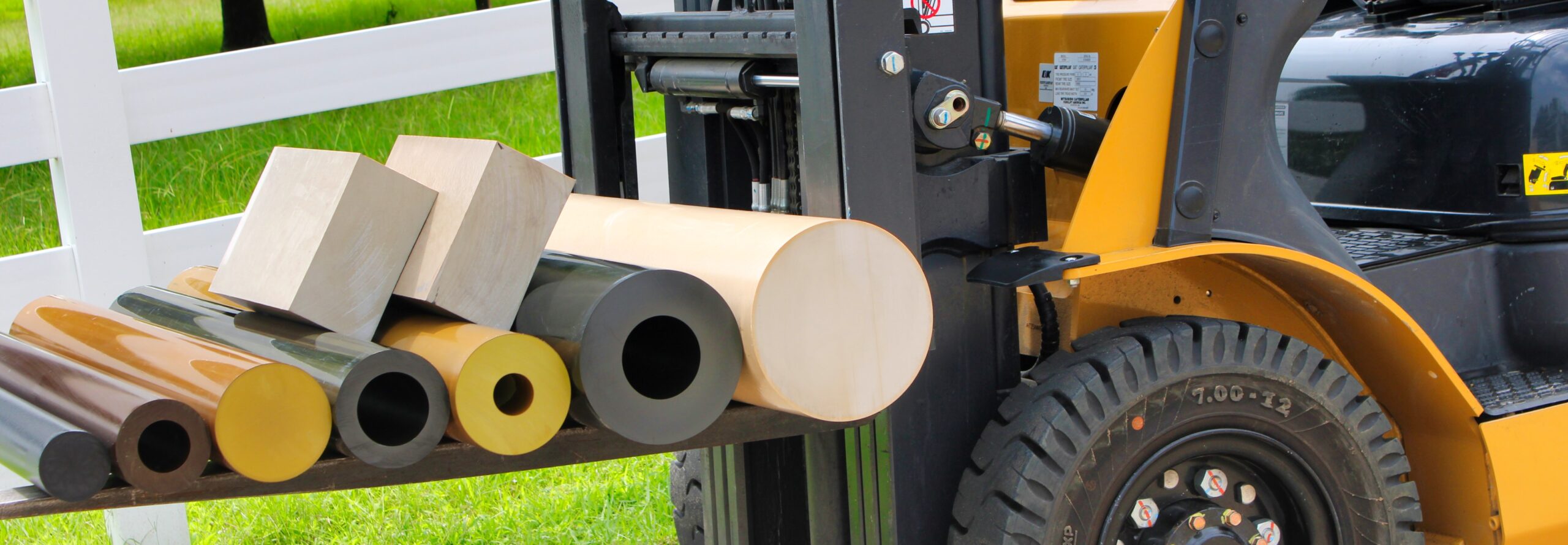
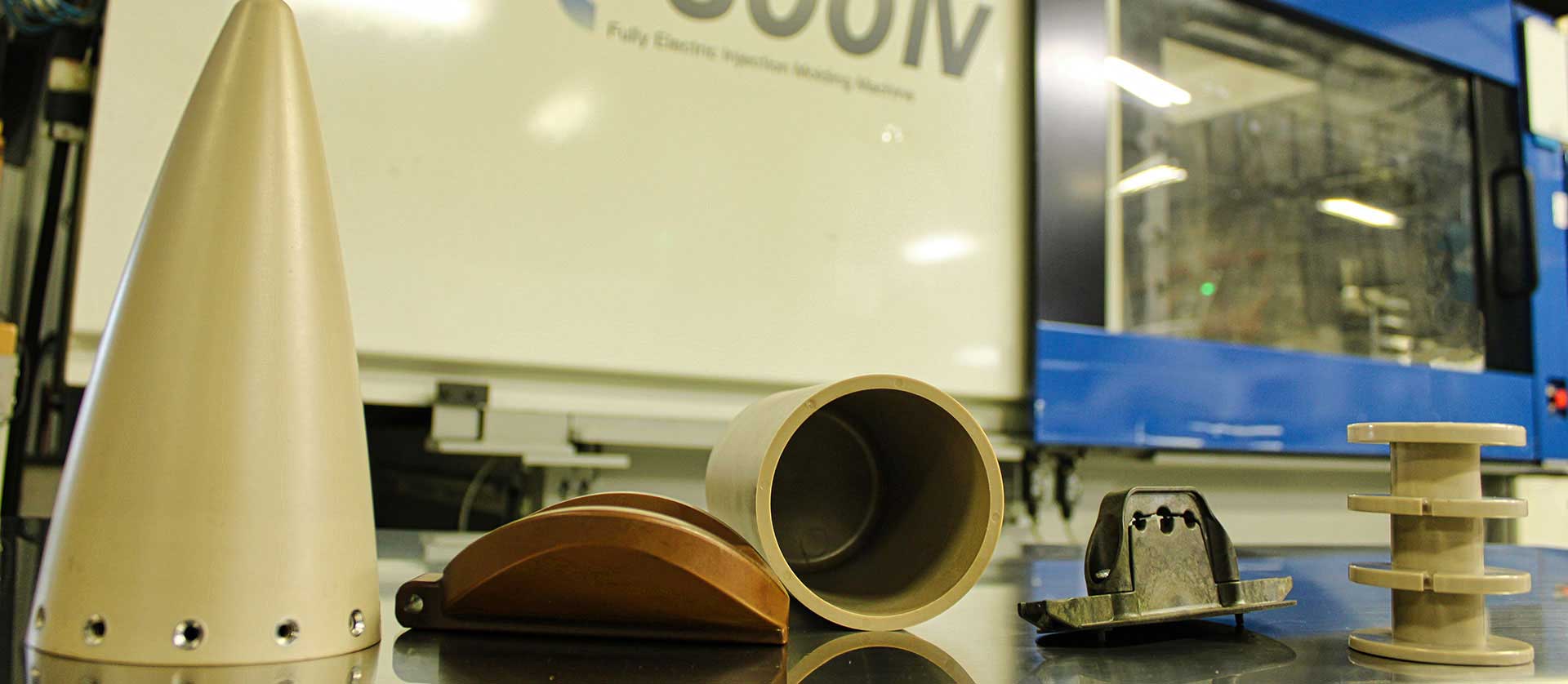
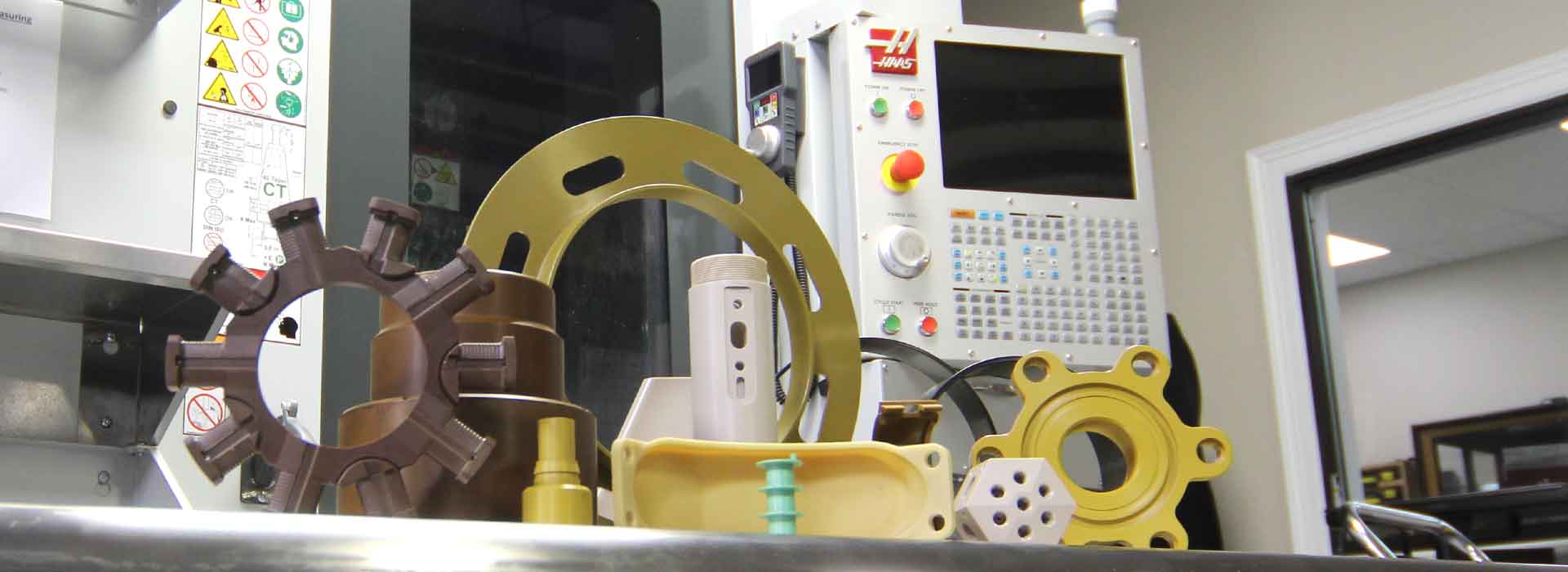
In the widest selection and most cost-effective forms available.
Polymer Processing and Precision Parts Manufacturing Experts
Drake Plastics leads the industry in developing and manufacturing ultra high-performance polymer stock shapes, injection molded parts and precision machined components.
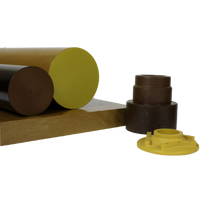
Stock Shapes for Machining
Drake’s unparalleled range of stock shape sizes and configurations extends the application range and maximizes machining efficiency of these ultra high-performance polymers.
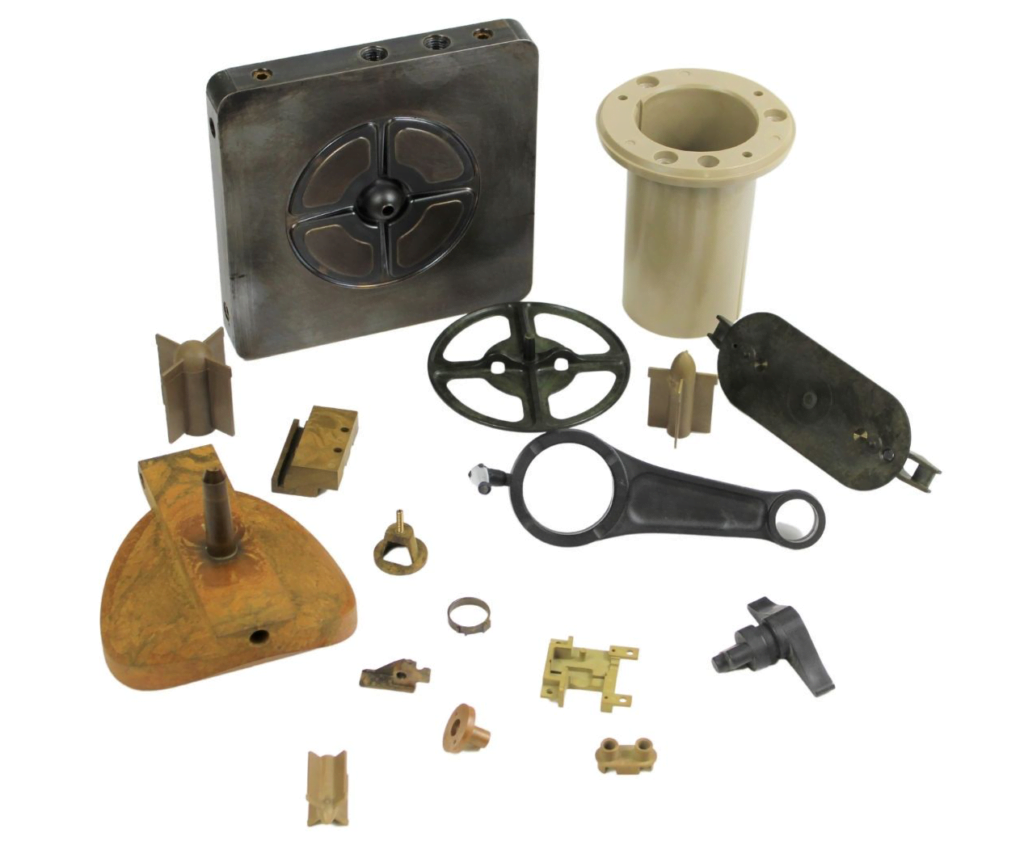
Injection Molded Parts
The science behind Drake’s state-of-the-art injection molding operation assures exceptional quality and consistency in molded parts. When critical tolerances and other features are impractical or impossible to achieve with injection molding alone, we can deploy our precision machining capabilities to provide hybrid molded/machined part solutions to meet the specifications required.
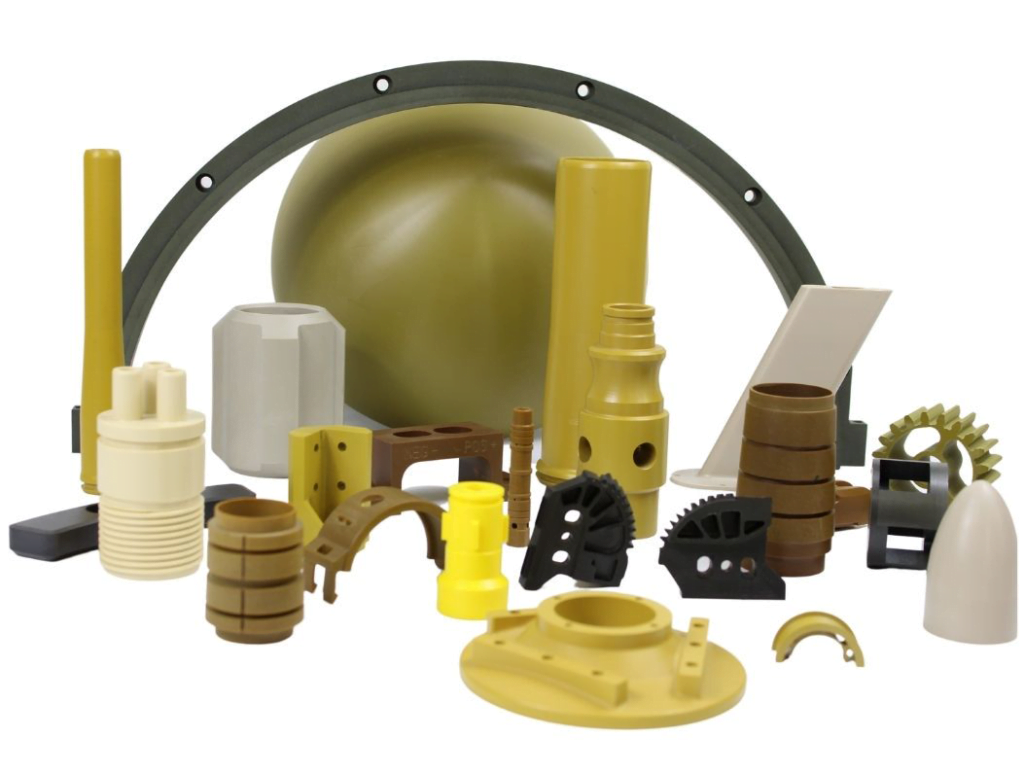
Precision-Machined Parts
Drake supports and supplies the best polymer-focused machine shops in the world, but some circumstances dictate a direct connection with Drake as the shapes producer. In those cases, our state-of-the-art precision machining, intimate material knowledge, re-curing and annealing, priming, coating, laser engraving, CT inspection, CMM part inspection, mechanical testing, and material and process certifications stand ready to serve challenging and complex customer requirements.
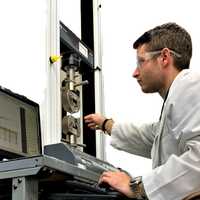
Drake extends the application range of high-end polymers by developing new sizes and unique configurations to serve new applications. Our technology also allows us to develop cost-effective custom sizes and shapes to hold material loss in fabrication to an absolute minimum.
Why Drake Plastics?
Drake Plastics leads the industry in ultra high-performance polymers with the widest array of rod, plate, and rigid tube stock shapes for machined parts. Many sizes were developed to closely approximate the dimensions of a final part. The benefit of these “leaner” sizes: minimal material loss when machining our line-up of Torlon PAI, PEEK, Ryton PPS, Victrex HT, Ultem PEI and AvaSpire PAEK stock shape products.
Product and process development investments coupled with our culture of invention have yielded sizes and configurations many thought impossible in ultra high-performance polymers.
With more than 25 years’ experience in our field, engineers often consult with us to determine the best material for their applications. Once specified, they know our products will perform consistently through their application’s life cycle, thanks to our rigorous AS9100D/ISO9001:2015 Certification Quality Management System and unique process control technology. In addition, our in-house machining and injection molding operations afford hybrid molded/machined parts when needed for precision tolerances and allow an easy transition from machined to molded parts.
On service, Drake’s on-time delivery is typically 98% or better, and 100% customer satisfaction is the norm. Our friendly and knowledgeable team look forward to adding you to our long list of happy customers.
Why Torlon?
Torlon polyamide-imide is recognized as the highest performance polymer that can be melt processed. Drake Plastics extrudes machinable shapes and injection molds both parts and shapes in all Torlon grades and offers the widest selection of sizes and configurations in the industry.
With a heat deflection temperature of up to 539°F (282°C), Torlon PAI offers unmatched strength at elevated temperatures. It has been used in many applications with extended exposure to 500°F (260°C) and is stronger at 400°F (204°C) than most engineering polymers at room temperature.
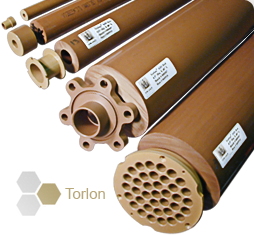
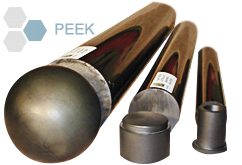
Why PEEK?
PEEK is recognized as having the best balance of chemical resistance, wear-resistance and heat resistance among all thermoplastics. It has a Tg of 143°C/289°F. Drake processes all PEEK grades into extruded stock shapes as well as injection molded parts.
Technically PEEK is part of a family of polyarylether ketones (PAEK) but PEEK is the recognized designation. Related chemistries based on PEK and PEKK offer unique thermal benefits to traditional PEEK and are also offered by Drake
Why Ryton?
Ryton R4 has a Tg of 88°C/190°F and delivers impressive mechanical strength, electrical insulation, and exceptional chemical and hot water resistance. In fact, it has no known solvents below 392°F/200°C. Its performance and cost make it an excellent choice for applications in aggressive chemicals at elevated temperatures.
Previously limited to injection molded parts, Drake’s development of Ryton R4 stock shapes has led to its expanded use in precision-machined electrical, fluid handling, transportation and oil and gas equipment components.
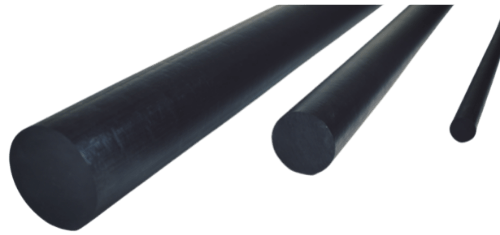
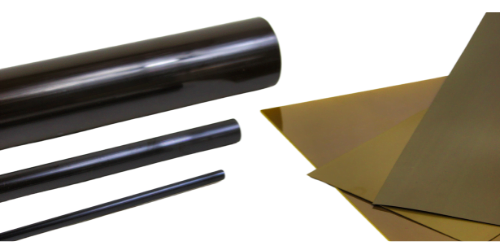
Why Drake PAI?
Several Drake PAI products including thin sheet and film, 4200 and others in development originate from PAI that is not a standard Solvay Torlon resin.
For example, when Solvay discontinued the pelletized resin for extruding Torlon 4200 shapes, we developed technology to produce Drake 4200 PAI shapes from PAI powder as equivalents. Drake 4200 PAI shapes and parts meet the physical properties and quality specifications of those sold as Torlon 4200 while providing customers long-term supply assurance for exisiting and new applications.
Why Ultem?
Ultem PEI has a Tg of 217°C/422°F and retains its strength and rigidity up to 390°F/200°C. Highly dimensionally stable, 30% glass fiber reinforced Ultem 2300 has an in-flow coefficient of linear thermal expansion (CLTE) comparable to aircraft-grade aluminum.
Other key properties include flame resistance, high dielectric strength, hydrolytic stability, and resistance to long-term exposure to steam and many chemicals. Drake offers Ultem 2300 in Seamless Tube, and specialty Ultem formulations in custom shapes.
Seamless Tube is a registered Trademark of Drake Plastic Products Inc.
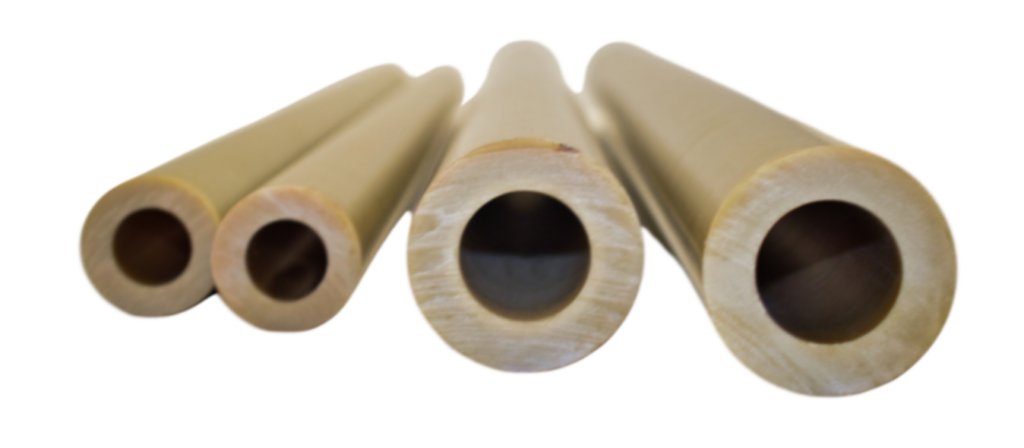
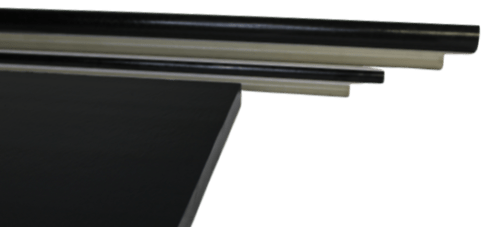
Why AvaSpire?
AvaSpire polyaryletherketone (PAEK) is a PEEK-based polymer blend with a notably higher Tg than PEEK at 158°C/316°F. Depending on the chemical environment and stress load, its greater ductility and its stiffness over 150°C/300°F can make it an attractive alternative to PEEK. The unreinforced grade’s light color also enhances part aesthetics and colorability.
AvaSpire is FDA compliant in all grades including the carbon and glass-reinforced formulations that provide higher mechanical strength over the unfilled material.