Worldwide Technical Support for Customers Machining our High-performance Plastic Stock Shapes
Drake Plastics offers technical support to customers around the world who machine our stock shapes made from Torlon PAI, PEEK, Ryton PPS and other advanced polymers. Our goal: Assist in achieving the highest possible quality and performance in parts machined from these exceptional materials.
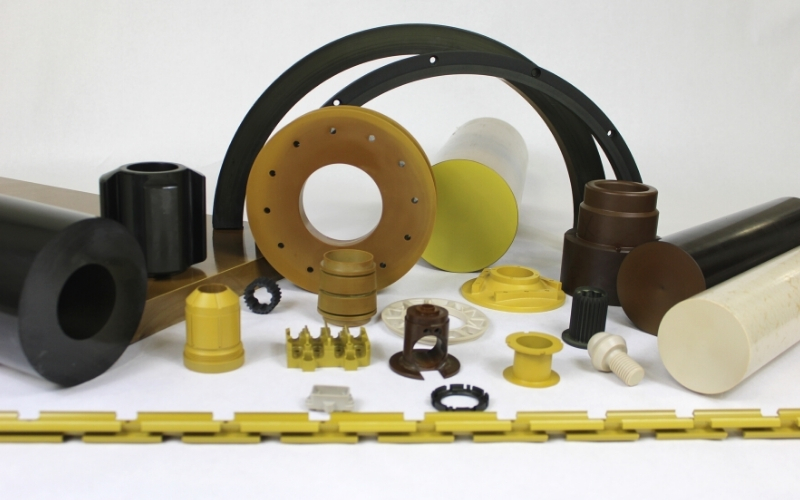
Sharing Our Machining Expertise
Customers around the world who machine our Torlon PAI, PEEK, PAEK, Ryton R-4 PPS and other high-performance plastics understand the need to produce parts at a consistently optimum level of performance and quality. The machined components are very often in severe and aggressive environments where long-term performance cannot be compromised. In addition, the value of these materials is very high based on the benefits they provide in each application, and quality problems in production can be very costly. Advanced polymers are often specified in formulations with different levels of carbon and glass fiber reinforcement to increase strength and stiffness and with solid lubricants to improve bearing and wear properties. These modifiers add another level of intricacy to machining precision parts properly from these materials.
Drake Plastics is committed to providing technical support to our machining customers faced with these challenges. Our investments in machine tools and our highly skilled machinist-programmers ensure that we stay on the leading-edge of equipment and technology required to machine consistently high quality parts. Our commitment is to share what we have learned and provide customers with technical information and support to produce consistently high-quality parts from the stock shapes we supply.
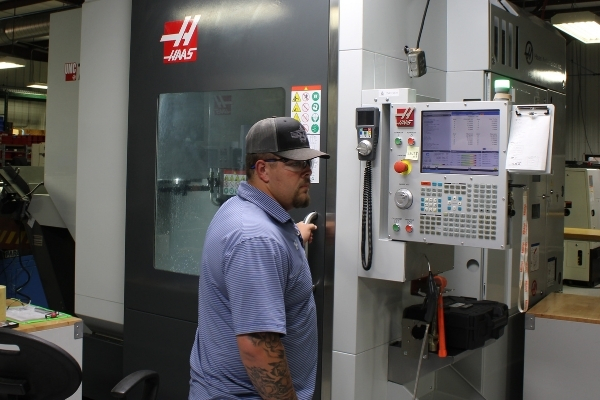
Cost-efficient Sizes and Shapes
Drake Plastics’ commitment to machining customers includes offering our advanced polymer stock shapes in the industry’s most cost-effective sizes and configurations. In addition to an unmatched selection of standard sizes in rod and plate, we supply custom sizes and lengths, precision blanks and centerless ground rods that improve machining efficiency, quality, and yield. As a cost-effective alternative to coring out rod for parts with a circular configuration, Drake Plastics also extrudes Torlon PAI and Ultem 2300 Seamless Tube in numerous OD/ID combinations.
Technical Support Based on Processing and Machining Experience
Drake understands how to achieve the optimum levels of performance and quality with advanced thermoplastics. This know-how comes from our many years of experience in both extruding and machining high performance polymer stock shapes from these high-performance polymers.
Our extrusion technology has been developed to avoid degradation, minimize stress, manage fiber-orientation and minimize camber; factors that contribute to high quality machined parts with reliable performance.
This expertise, and our practical experience gained from machining millions of precision parts from high-performance plastics, has given us unique insight into the best techniques for working with these materials. We freely share this technical information with our machining customers who have an equal commitment to the highest levels of quality in the parts they produce.
One example of our specialized technical support is the information we share about how material properties differ between linear and transverse dimensions in extruded shapes. This differential occurs with both reinforced and unfilled polymers and is the result of internal forces that occur during forming and cooling of extruded stock shapes. It is especially pronounced in glass fiber or carbon fiber reinforced polymer formulations, where the difference in strength measured on the X to Y axes is substantial.
During Drake’s stock shape extrusion processes for glass and carbon fiber reinforced advanced polymers, the fibers reliably align in the same orientation relative to the extrusion direction and each shape’s size. This occurs with every stock shape we produce, production run after production run. Our knowledge of fiber orientation in a stock shape enables us to recommend how to best position parts during machining to yield the highest strength where it is needed most.
In this example, the part machined from 30% carbon fiber reinforced Torlon 7130 plate is positioned so that the gear teeth exposed to the highest stresses are parallel with the direction of the carbon fibers. This results in optimum strength in those high stress areas. To ensure precise positioning of future parts, we created a ‘parent’ drawing that can be superimposed over our extruded Torlon 7130 plate and used as a template by the machinist.
Understanding our various polymers’ flow profiles and the resulting fiber orientation enables us to recommend how the strength, toughness, and dimensional stability of the parts machined from our stock shapes can be optimized.
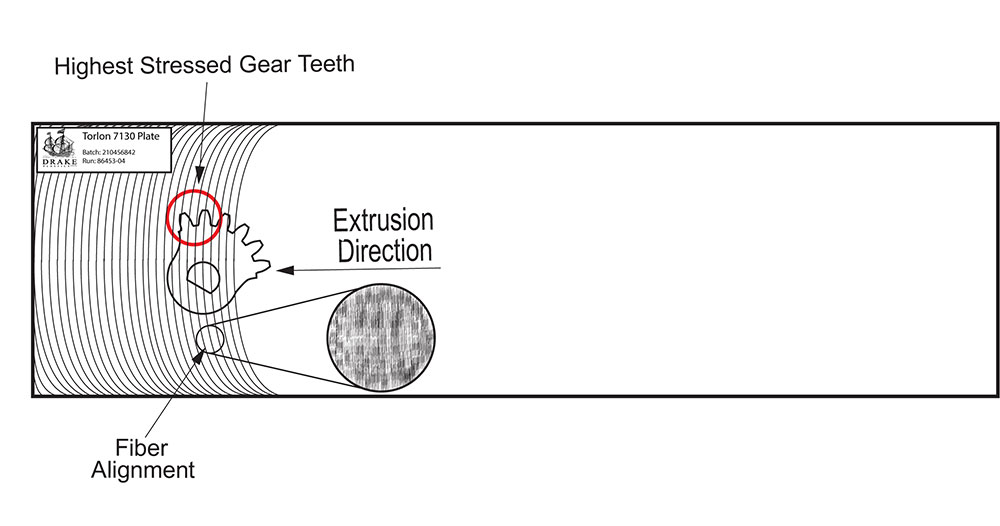
Drake Plastics welcomes the opportunity to support customers with the experience we have gained from years of machining our stock shapes made from polymers that include:
- Victrex PEEK
- Victrex HT PEK
- KetaSpire PEEK
- KetaSpire High-Temperature PEEK XT
- AvaSpire PAEK
- Ryton R-4 PPS
- Ultem PEI
- Vespel PI
- Celazole PBI
- High strength composites
- Specialty polymer formulations
Production Support for Problematic Components
Drake Plastics offers to machine parts with a very high material content where customers may wish to avoid economic risks should problems occur. To eliminate the potential for material loss or rejects in such situations, Drake Plastics offers to produce the components and supply them directly to our machining customers on request.
Post-Machining Services
Drake Plastics offers our machining customers testing services to meet different industry compliance standards, and several post-production capabilities:
- Laser etching
- Specialized coatings
- Precision-machined custom finishes
- ASTM test specimens machined from specified material
- ASTM mechanical properties testing
- CT scanning to validate internal part integrity
- CMM: Coordinate Measuring Machine part inspection
- Post- annealing and curing to optimize part performance
- Ultrasonic cleaning, specialty packaging
- Material and process certification templates
Post-Curing and Annealing Machined Part
Drake offers our post-curing capabilities to customers who machine our Torlon stock shapes. This service gives machining companies the ability to supply Torlon components at optimum performance levels to their customers. We also anneal machined parts made from PEEK on request to meet specialized requirements.
Post-curing machined Torlon PAI parts
All Drake Plastics Torlon PAI machinable stock shapes go through our post-curing processes to achieve their full performance potential. Our post-cure protocol brings Torlon PAI’s typical core Tg (glass-transition temperature) midpoint value to 282°C (540°F). During post-curing, the PAI polymer chains extend and optimize the material’s toughness, wear resistance and mechanical properties. These high performance levels are then inherent in components machined from Drake Plastics’ Torlon PAI rod, plate and Seamless Tube.
Some parts benefit from a secondary post-cure after machining. Re-curing restores the imidized outer layer or “skin” that forms on Torlon PAI stock shapes at high cure temperatures. This outer layer optimizes resistance to wear and chemical attack, which can be a benefit for machined components used in severe service environments.
Annealing parts machined from advanced polymers
Drake Plastics anneals its extruded stock shapes to minimize internal stresses that occur as polymers rapidly change from a hot melt phase to ambient temperature during processing. During annealing, the part or shape is heated to a temperature well above its Tg (glass transition temperature) where the polymer chains can move and relax the stress that was induced during processing. Then it is cooled very slowly and uniformly, resulting in low stress parts that are tough and capable of maintaining very precise dimensions.
Drake Plastics custom anneals parts machined from PEEK and other advanced polymers on request. It can be useful to achieve specific crystallinity targets or highly precise dimensional control sometimes necessary for parts with particularly thick or varying cross-sections.
Note: Torlon PAI extruded stock shapes are always post-cured instead of annealed. For annealing to be effective, it must be conducted over the polymer’s Tg (glass transition temperature). This allows for polymer chain relaxation which translates to reduced stress. It is not possible to heat Torlon PAI over its Tg without risk of distortion or blistering. Heating Torlon PAI to its post-cure temperature of 260 °C /500 °F has a minimal effect on reducing stress because its Tg is even higher. Consequently, Drake Plastics goes to extreme measures to minimize stress in our extruded Torlon PAI stock shapes. Our precisely controlled processes are critical to producing shapes with the lowest possible stress since it cannot be effectively relieved after production.
Machining Guidelines Available to Customers
Machining guidelines are available to assist customers with proven techniques for producing parts from our advanced polymer products. Other technical information available on our website includes typical applications of our high-performance thermoplastics in major industries, and properties data on each material.
Cost-Effective Transition from Machining to injection Molding
When machined part production quantities increase significantly but are still below levels that justify precision-tolerance injection mold tooling, molded blanks or near-net stock shapes that are then finish-machined can serve as an efficient, cost-saving next step. Because they only approximate a part’s actual dimensions, they can be produced in low-cost injection molds, then machined to the specified part dimensions. The reduction in material loss coupled with low-cost molds can result in a far more cost-effective option vs. machining from rod or plate.
Drake Plastics supports our machining customers with injection molded parts or near net blanks for finish machining, so they can always offer the highest value to their customers.
Application Development Support
Many customers come to Drake Plastics with a general description of what they need. Our support engineers can assist in several ways:
- Material selection: Drake Plastics’ engineers offer many years of experience with applications in Torlon PAI, PEEK, Ryton PPS, Ultem PEI, Vespel PI and other ultra high-performance thermoplastics used in demanding environments. Their experience in industries where these parts are used includes aerospace and defense, oil and gas and chemical processing, electrical and electronics, semiconductor manufacturing, medical and other high tech sectors.
- Application review: Customers can rely on Drake Plastics to help define various key factors that affect the performance of a machined part. For example, defining the best fiber orientation for parts produced from glass or carbon fiber reinforced stock shapes can have a major impact on the strength and durability of components. Drake Plastics also offers expertise in annealing and post-curing and surface finishes, all of which can improve performance in use.
- Prototyping: Once the design and material are defined, our machining team can provide precision prototype parts in Torlon PAI, Vespel PI, PEEK, Ryton PPS, Ultem PEI and other advanced polymers to validate component performance in the actual end-use operating environment. Drake Plastics is well-equipped to provide our machining customers with prototypes quickly and economically in advance of full-scale production.
- Testing and validation: Drake Plastics’ Differential Scanning Calorimetry (DSC) can help thermally characterize materials when required. In addition, the services of our mechanical testing lab are available to evaluate mechanical properties.
Drake Plastics as a Custom Material Development Partner
Companies often work with us on a confidential basis as a development partner to produce prototypes and test parts from their own proprietary material compositions. Our feedback on processing and machining characteristics helps fine-tune formulations to improve machinability and enhance finished part performance. We also provide support with parts production to help these companies launch new products and systems that incorporate critical components made from their exotic materials.
"*" indicates required fields