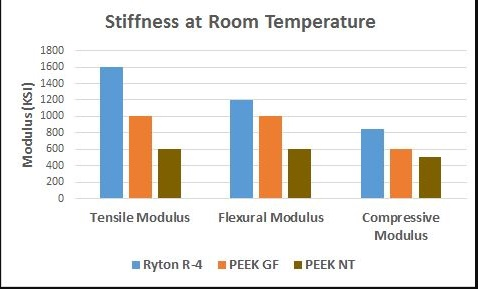
Ryton® PPS was first commercially produced in 1972 by Phillips Petroleum making it the first of the high strength, high temperature melt-processable polymers. Ryton R4, a 40% glass fiber reinforced grade that was the “go to” polymer when high strength in aggressive service conditions existed. The 40% glass fiber reinforcement increased an inherently low glass transition temperature of PPS turning it into an exciting high performance polymer.
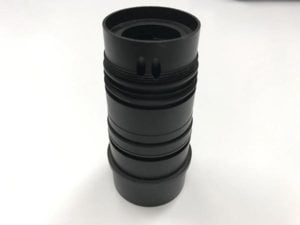
Ryton’s strength, stiffness and chemical inertness (there are no known solvents for Ryton PPS under 200°C) make it suitable for applications in oil and gas, transportation and aerospace. Additionally, Ryton R4 offers a heat distortion temperature of 509°F/ 265°C, which is among the highest of the thermoplastics as well as room temperature stiffness that exceeds glass reinforced PEEK at a much lower cost.
Ryton’s dielectric properties are also among the best of the high temperature polymers offering a high dielectric strength and a low dielectric constant and dissipation factor over a range of temperatures and frequencies.
Ryton has been widely specified for more than 30 years but primarily for injection molded parts. Its potential for parts needed in smaller volume applications has been limited by the lack of high quality stock shapes with corresponding resin certifications for machined parts and prototypes. Both injection and compression molded shapes and have been tried but neither provided the same strength and stiffness as Ryton R4 PPS.
Today Ryton PPS acceptance is growing through the development of new compounds that offer improved toughness and steam resistance. Ryton competes with both PEEK and high temperature nylons for designer’s attention in many industries where cost effective solutions are paramount Drake’s Ryton R4 shapes are based on Ryton R4-240
Plasma torch insulators, downhole connector insulators, valve seats and high temperature seal.