High-performance thermoplastic labyrinth seals improve centrifugal compressor efficiency by offering reduced running clearances. A new manufacturing development now lowers their cost.
High performance thermoplastics have become the materials of choice for OEM and retrofit labyrinth seals in many centrifugal compressor services. Though more costly initially than seals made from aluminum and other soft metals, the benefits they offer in efficiency, increased throughput, longer service life, corrosion resistance and in protecting the rotating assembly from damage can offset the premium within months.
Also referred to as advanced polymers, the major benefit driving the widening use of these thermoplastics is that engineers can design highly efficient rub-tolerant labyrinth seals with much tighter running clearances than soft metals allow.
These polymers eliminate the risks associated with metal rotor to stator contact and have inherent toughness even at cryogenic temperatures. Their resilience allows the labyrinth seal to deflect without permanent deformation even from hard rubs during rotor contact that can occur as turbocompressors traverse through critical speeds, or during upsets.
Despite their long term cost and efficiency benefits, the initial cost and multi-layered supply chain to obtain advanced polymer labyrinth seals compared to soft metals has created some resistance to their use. However, a new manufacturing technology simplifies seal manufacturing and dramatically reduces the cost to produce split labyrinth seals compared to those machined from traditional long lead time compression molded billets.
Two high-performance thermoplastics account for the vast majority of specifications of polymer materials for turbocompressor labyrinth seals: PEEK (polyetheretherketone), supplied by Victrex plc and by Solvay under its KetaSpire brand; and Torlon PAI (polyamide-imide), also produced by Solvay. Formulations of both polymers have been developed specifically for long term performance in rotating equipment applications.
Soft Metal Seal Designs
Soft metals such as aluminum have been used traditionally for stationary labyrinths in turbocompressors. The compressor shaft and impellers rotate within the labyrinth (Figure 1), and the soft metal seals are considered “sacrificial” relative to the rotating components made from steel or other harder metals.
Traditional compressor designs must allow adequate rotor-to-seal clearance to traverse critical speeds during start-up and anticipated upsets without rotor-to-seal contact. If contact does occur, the labyrinth teeth would be permanently deformed, and the designed pressure drop between the seal teeth would be permanently compromised. To lessen the risk of contact, designing for no rotor/ stator contact is the norm. However, this approach accepts diminished efficiency and reduced throughput as the consequence. Closing clearances to the point where contact can occur risks the possibility of a wide leak path and inefficient compressor operation until the next overhaul. A hard rub between metallic rotor and metallic seals also risks upsetting the rotor which can lead to a catastrophic failure.
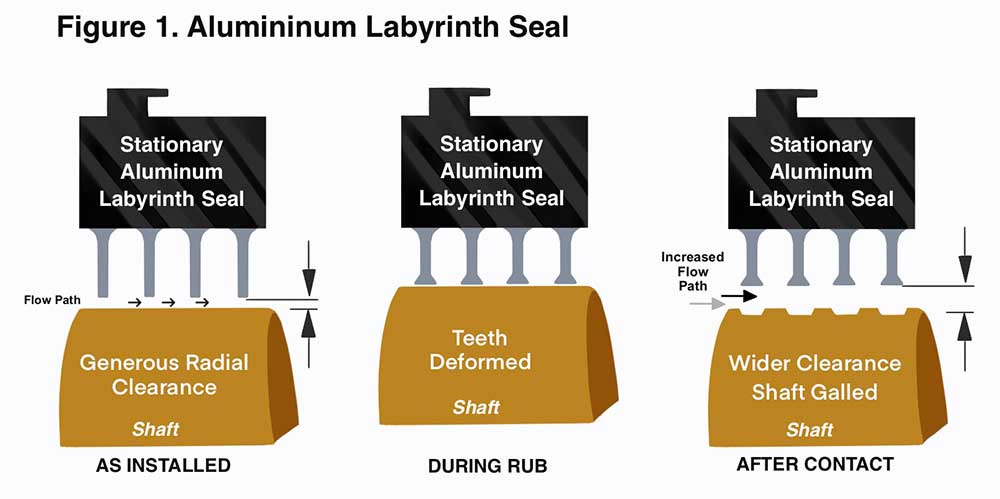
Rub-tolerant Thermoplastic Labyrinth Seal Designs
Rub-tolerant polymer seals are typically roll-in replacements for soft metal designs in applications such as shaft, impeller eye and balance piston labyrinths and case-end seals. Aluminum holders are commonly used to simplify installation. They also can reduce the amount of material used in cross-sections of seals made from advanced polymers, which are much more expensive than aluminum.
Polymer labyrinth seals allow engineers to design teeth-on-stator configurations with minimal clearances relative to the rotor. As the name implies, the seals are designed to tolerate rotor contact during start up and through upsets while maintaining their design clearance in operation. This provides maximum operating efficiency. The upgrade in sealing performance has the related advantage of providing increased production capacity in facilities where compressor output is the bottleneck.
Designing with components in close proximity means minor rubs between the teeth and the shaft are intended to occur as the compressor goes through critical speed phases. Contact is almost a certainty during upsets as well. Because of the inherent thermal capability, wear resistance and toughness of the polymers, the teeth deflect on contact, then rebound without wear or damage to the rotor or the seal. (See figure 2).
Rub-tolerance enables thermoplastic labyrinth seals to maintain design clearances from start-up through steady-state operation, reducing recirculation and decreasing power consumption. Conversely, the as-installed clearances on aluminum seals can be compromised minutes after start-up due to permanent damage from contact between the rotor and the seal.
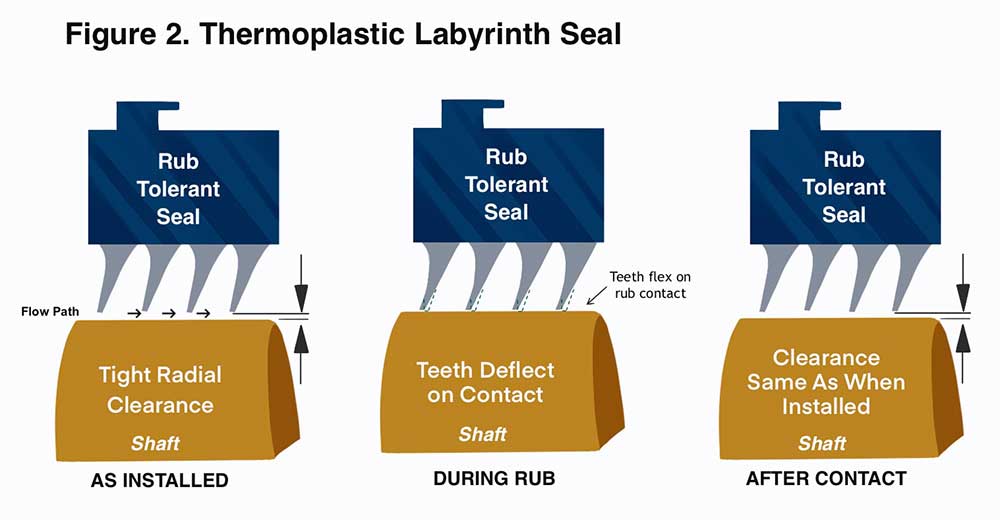
High Performance Polymers for Rub-tolerant Labyrinth Seals
Torlon PAI (polyamide-imide) and PEEK (polyetheretherketone) are widely specified for rotating equipment applications. They share several attributes that contribute to reliable performance in rub-tolerant seals. Both have a low coefficient of friction and high resistance to wear under dynamic loads, and they retain structural strength at high operating temperatures. Their inherent impact resistance and resilience is another key factor. This capability enables the design of rub-tolerant seals with teeth that deflect and rebound after rotor contact rather than incurring permanent damage which occurs with soft metals.
These advanced polymers also resist many chemicals that corrode metals and lead to more frequent shutdowns for repairs and replacements. However, as with all materials including metals, each has its own unique chemical resistance profile that must be evaluated relative to the operating environment of the compressor.
The significant differences in temperature resistance and load bearing capability at thermal extremes also determine the suitability of each polymer for specific service conditions.
PEEK is recognized for its resistance to a wide range of chemicals that adversely affect many other high performance thermoplastics. The polymer also absorbs very little moisture, and performs well in hydrogen, wet coker and syngas environments.
It also combines toughness with high structural strength at elevated temperatures. On thermal performance, PEEK has a glass transition temperature or softening point of 149oC (300°F), and a continuous service temperature suitable for applications with an operating limit up to 121oC (250°F) in compressor seal applications. This allows for a thermal increase which should be anticipated after rotor contact. The intent is to keep seals made from PEEK below the polymer’s Tg of 149oC (300°F).
With a Tg of 280oC (536°F), and a continuous service temperature of 250oC (482°F), Torlon PAI extends the use of rub-tolerant labyrinth seals to thermal operating conditions well beyond the capabilities of PEEK or other advanced polymers. It also retains higher structural and load-carrying capabilities at elevated temperatures than any other melt-processable thermoplastic.
Torlon PAI performs particularly well in rotating equipment exposed to hydrocarbons, refinery wet gas and CO2. The polymer is somewhat hygroscopic, and reaches equilibrium with the moisture levels in its operating environment. Figure 3 charts its hygroscopic expansion. These effects must be considered when designing and fabricating seals from any PAI grade, as the effect of moisture over time is similar for all formulations.
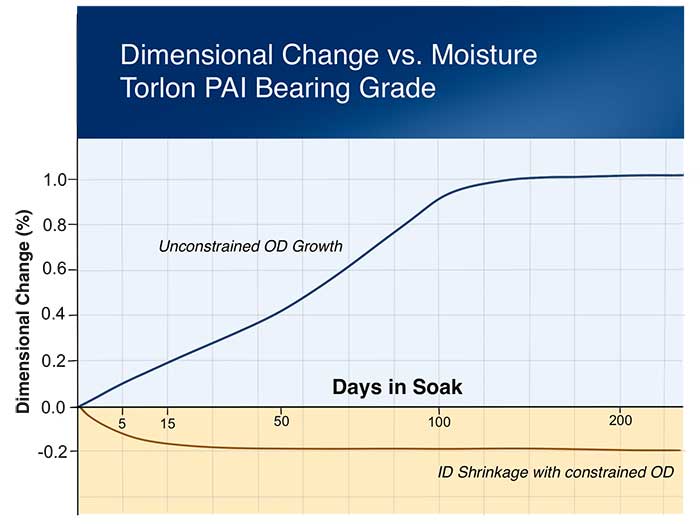
Torlon 4540 PAI Compression Molded Labyrinth Seal Grade
Developed as a compression molding grade for labyrinth seals, Torlon 4540 has properties that are well-suited to rotating equipment. The material combines impact strength with resistance to high temperatures, wear and deformation under high dynamic loads. The formulation is supplied in powder form for compression molding into tubular billets, which are then fabricated in several steps to produce seals.
The compression molding process itself, however, presents some drawbacks in overall cost, and in non-uniform forming pressure within the mold as well as degassing conditions that can create inconsistent properties through the cross-sections of machined parts.
A new development in processing a PAI formulation comparable to Torlon 4540 overcomes these drawbacks by providing a more cost-effective and performance-consistent alternative in extruded form. (See Seal Segments below).
Traditional Methods for Manufacturing Labyrinth Seals
There are two traditional methods for producing large seals from Torlon PAI and PEEK. One involves compression molding the materials into large thick-walled “master” tubes in various OD/ID combinations to accommodate different finished seal diameters. Current compression molding technology limits the OD to approximately 127 cm (50 in.).
To allow for finish-machining to specified dimensions, tubes are somewhat oversized to the seal’s specified OD/ID. Tubes are parted into rings that approximate the seal’s thickness. The rings are then split, and the halves are pinned and banded together. The two halves are machined to a round configuration, which is then finish-machined to the seal’s final dimensions.
Another method uses pieces that are cut from compression molded or extruded plate in PEEK or Torlon PAI. These cut pieces require the same steps as the split tubes for sizing and finishing.
Both approaches involve substantial labor hours to cut, fixture, and machine the rough seal sections to a specified blank configuration prior to machining to final dimensions. The inability to start with efficient sizes that approximate final dimensions creates significant loss of high-value material to achieve a blank ready for finish-machining.
A new development in extrusion technology produces near-net sized arcs that dramatically reduce the cost to produce large seals including split polymer labyrinth seals compared to compression molded billets. Branded commercially as Seal Segments®, the innovation comes from Drake Plastics Ltd. Co. based near Houston TX.
The technology narrows the up-front cost differential that exists between compression molded thermoplastic labyrinth seals and those made from soft metals. This gives users faster payback on the long-term operating efficiency that thermoplastic rub-tolerant seals provide.
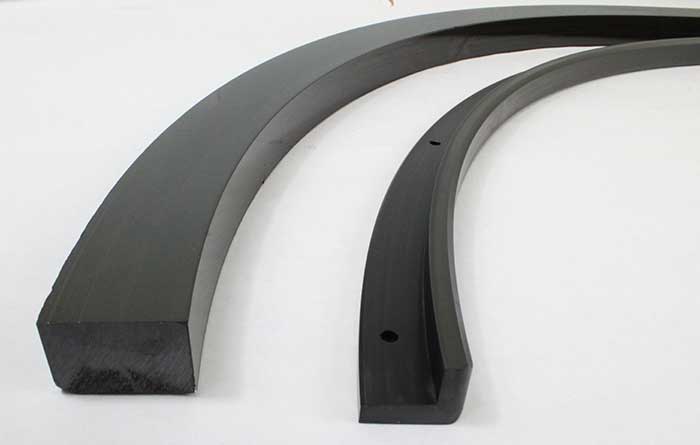
Seal Segments are produced by melt-pressure extrusion. Each as-extruded arc is typically*provided to 180o(plus tolerance) and matches the radius, thickness and height of the seal. This yields two halves that are then mated into a perfect circle. It eliminates the hours of labor and material loss involved with preparing blanks from compression-molded ingots for machining to specification.
*Seal Segments for certain very large seals and bearings are provided in multiple sections rather than two halves to facilitate handling and assembly.
Drake 4340 PAI Extruded Labyrinth Seal Grade
Drake Plastics has developed technology to extrude a PAI labyrinth seal grade made from Torlon PAI resin with a formulation comparable to Torlon 4540. It differentiates the material from the compression molding powder grade by using the designation Drake 4340 PAI. As expected with melt-extrusion, testing demonstrates that the extruded 4340 PAI formulation affords more consistent and higher property values throughout the cross-section of a seal compared to parts made by compression molding. Seal Segments extruded from Drake 4200 PAI couple its performance benefits with a material form or shape that is more cost-efficient for machining into seals.
Process Differences Determine Seal Performance
The compression molding process relies on compaction sintering of PEEK or Torlon PAI polymer formulations in powder form at high temperatures. The process is especially challenging for making large sizes that are consistent and heavy cross-sections that are uniform. This is due to the polymers’ low 3:1 bulk density, low thermal conductivity, and high melt temperatures.
In compression molding, the polymer is melted from the outside surfaces. Air and gas become trapped within the material as it begins to melt in the core of the billet. High pressure is used to consolidate this trapped gas to eliminate visible porosity. However, because of inconsistent melting through the cross-section, properties in the center of large billets can be lower than at the outside extremities. Symptoms such as powdery material evident during machining, and lower toughness when the core section is tested indicate the effects of the inconsistency.
During the melt extrusion process, the polymer formulation is converted into machinable semi-finished shapes under tightly controlled temperatures, pressures, and rates. The solid lubricants which provide the low coefficient of friction are pre-compounded into the resin and further dispersed in the extrusion process to provide consistent properties throughout the cross-section of extruded seal segments.
As Table 2 shows, physical properties of the melt extruded labyrinth seal PAI grade are significantly higher than those of the compression molded formulation. This is because in the melt extrusion process, the polymer is evenly melted, degassed, and consolidated by a screw within the machine barrel.
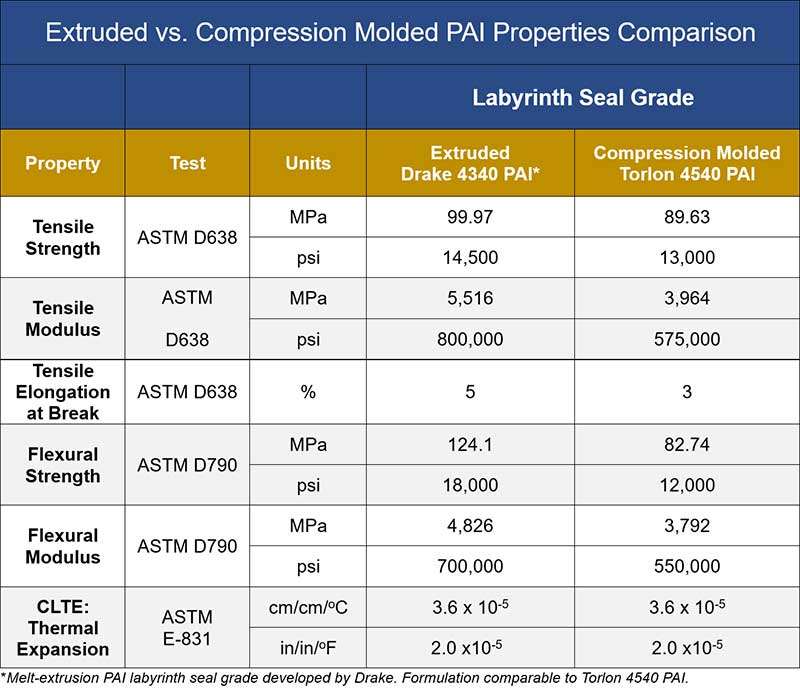
Expanded Size Range
While current compression molding technology has demonstrated an upper OD size limit of 127 cm (50 in.), extrusion of arcs as a continuous process has a virtually unlimited size range.
Drake Plastics reports its minimum diameter is 300mm (11.8 inches), and its largest project for a machined seal to date measures 12.2 meters (40 feet) in diameter. For large seals, another benefit of as-extruded dimensions that are close to finished part size is the reduction in the number of segments needed to create a full 360-degree seal. Working with fewer segments simplifies assembly and reduces the number of potential leak paths.
Guidelines for Designing Thermoplastic Labyrinth Seals
The use of advanced polymers for rub-tolerant labyrinth seals requires design details that differ from those for metals. The following guidelines for designing with advanced polymers vs. metals will facilitate a successful upgrade in performance:
- Reduce the seal’s operating clearances to those of the journal bearing clearances in the compressor. This usually results in a 50% reduction in seal clearance, and a resultant improvement in efficiency.
- Rake the seal teeth at an angle of approximately 15o toward the flow. This will allow for deflection during a rub, as well as creating turbulence between the teeth, reducing leakage further.
- Design generous radii at the root of the teeth. This maximizes support of the teeth and minimizes stress concentration in those areas.
- Machine the tooth tips as broad flat areas of approximately 0.75 mm (0.030”) to maximize their toughness.
Consider mounting larger seals such as balance piston seals in a metal holder ring. This has two benefits: it optimizes mechanical support of the seal and helps minimize material cost by reducing the thickness of the advanced polymer needed and keeping its use to the sealing area where its performance is most essential.
Benefits of Rub-tolerant Labyrinth Seals
In their decades of successful applications as retrofits to metal seals, polymer seals have demonstrated a consistent history of benefits. Increases in efficiency have typically ranged from about ½ to 1% per impeller, with a corresponding increase in throughput that compounds over time. Extended intervals for overhauls in wet gas applications of up to three-fold are not uncommon. The ability of a rub-tolerant seal to recover after contact also reduces recirculation within the compressor, which in turn reduces power consumption.
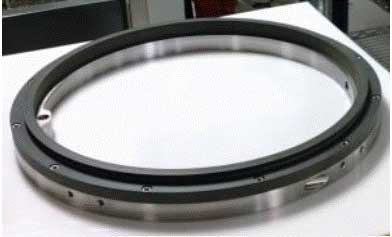