Exotic propellants, ablation, high g-force and vibration stresses, temperature, weather, and environmental extremes, EMI/RFI and radiation exposure and precision tolerance requirements all factor into military and defense applications for high performance plastic materials. Drake’s ultra high-performance polymers have built an impressive record with decades of success in providing solutions to these challenges.
Drake’s Ultra High-Performance Polymers in Weapons Systems
Precision accuracy and flawless, dependable performance under extreme conditions are essential to advanced weapons such as portable missile launchers. Light weight is also a factor in weaponry that is carried and launched by personnel on the move. Components in complex sighting and guidance systems must remain dimensionally stable under widely different environmental conditions and stand up to rough handling, aggressive propellants, launch temperatures and high velocities. Inherent flame resistance often is a requisite on the list of material specifications for components used in this type of military equipment.
Ultra high-performance polymers from Drake Plastics have been providing solutions to these engineering challenges for decades, often by delivering significant advantages over metals. Unique property profiles of the many different grades of Torlon PAI, Victrex and Solvay KetaSpire® PEEK, Ryton R-4 PPS and Ultem PEI offered by Drake in the form of machinable shapes and machined and injection molded parts afford a range of material and production options. This provides engineers the opportunity to match the requirements of the weapons components they are designing to the optimum material and parts manufacturing method that will yield the most efficient and effective combination of performance and cost.
Compared to metals, these ultra high-performance polymers resist corrosion from exposure to a vast array of chemicals, lubricants and propellants. They also withstand the effects of excessive moisture, and maintain their dimensional stability in extremes of humidity and temperature. All these benefits are essential given the likelihood of extended exposure to a variety of weather conditions. Because they are far more lightweight than metals, they also improve weapon portability and facilitate rapid deployment from location to location – a routine requirement in the field.

Torlon PAI and PEEK grades with reinforced with carbon and glass-fibers have exceptionally high structural strength and rigidity. With low coefficient of liner thermal expansion rates comparable to metals, they afford dimensional stability in precision components at both extremes of the temperature spectrum. They also maintain their structural strength in proximity to peak levels of intense heat incurred with repeated weapon firing. This combination of high strength and stability has been a key factor behind their choice for components that require precise dimensional tolerances to guide and assure accuracy in portable missile launchers.
Radomes, igniter cups, fins, wings, and cable supports are among the applications of these high-performance polymers in missiles deployed from portable and fixed platforms and other guided weapons. The complex weapons systems capitalize on Drake Plastics’ Torlon PAI, PEEK, Ryton R-4 PPS and other high-performance polymers for structural strength and stability under widely different and severe operating conditions. These polymer materials that Drake supplies as machinable stock shapes and parts have proven they can stand up to the demands of advanced weapons and weapon systems with over two decades of successful performance.
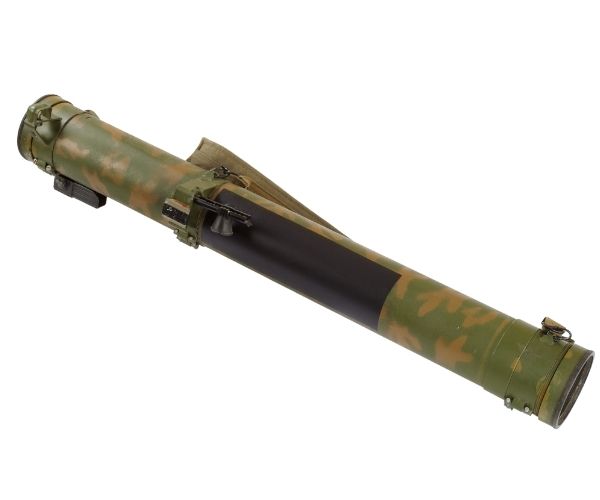
Military Aircraft Applications In Drake’s High-Performance Polymers
Drake’s ultra high-performance polymers have built a solid track record in providing solutions to the challenges associated with engineering complex military aircraft components. Routine operating conditions require lightweight materials that remain rigid and dimensionally stable in proximity to the intense heat from jet engines and through the rapid and extreme atmospheric temperature changes experienced in flight. Electronic shielding and electrical and thermal isolation are essential for uncompromising systems performance. In-flight stresses and the forces of acceleration, deceleration and landing demand that components maintain high levels of stiffness and impact strength. Missile propellants and jet fuels place the added requirement for uncompromised chemical resistance on materials used in aircraft components. Applications that are machined and injection molded from the array of formulations of Torlon PAI, Victrex and Solvay KetaSpire PEEK, Ryton R-4 PPS and Ultem PEI have demonstrated their effectiveness in meeting these challenges.
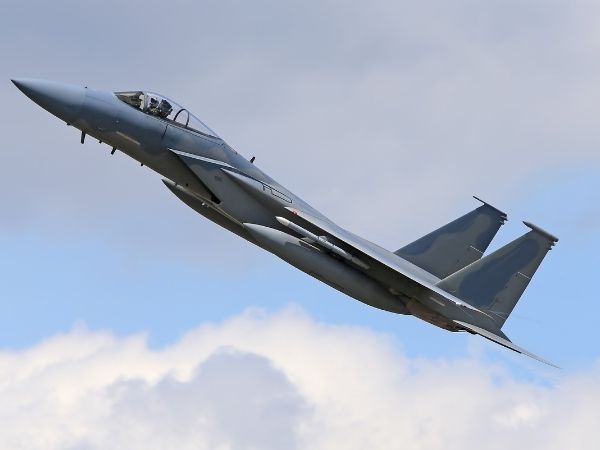
In most cases, components are engineered in Drake’s Torlon PAI, PEEK, Ryton R-4 PPS and Ultem PEI from the initial design stage. However, there are exceptions where these ultra high-performance polymers have provided solutions to unforeseen shortcomings encountered with metal components.
As an example, the fuel connects for the F-16 jet fighter’s auxiliary fuel tanks were originally made from stainless steel. The auxiliary tanks provide the jet fighter with an important tactical advantage in extending its range by 50%. The wetted metal connects used with the original tanks were deemed unsafe in the event of lightning strikes. Rather than pursuing a costly and uncertain path of trying to insulate the metal parts, the engineers took on the challenge of finding a material that would directly replace the metal components. The material had to resist degradation and embrittlement from exposure to jet fuel, withstand heavy vibrations without failure, and maintain its rigidity and dimensions at temperature excursions to 400°F (200°C) during afterburner flight. Drake’s development team worked with the aircraft’s engineers and pinpointed Torlon 4203L as the material with the best combination of properties to meet their requirements. They then specified Drake’s proprietary Seamless Tube® as the material form to be used for machining the connects. The Torlon 4203L parts machined from the extruded Seamless Tube® exhibited lower inherent stress levels and higher toughness and strength over injection molded parts. Producing the connects from Drake’s Seamless Tube instead of solid rod also minimized material loss and yielded a significant savings in machining time. From the first connect that Drake’s machining operation produced, every one has passed the rigorous 650psi (45 bar) pressure test required for the application.
Many military aircraft applications of Drake’s machined and molded Torlon PAI, PEEK, Ultem PEI and Ryton R-4 PPS are quite similar to those in commercial aircraft. They include electrical connectors, terminal blocks and light housings where the dimensional stability, strength, shielding benefits and electrical properties of these polymers are key factors. Bushings, bearings, rollers, gears, vanes and similar moving and sliding parts are also produced from bearing and wear resistant grades of these materials to achieve dependable long -term performance under extreme conditions.
Drake’s Ultra High-Performance Polymers in Naval Vessel Components
It would be a tough challenge to define an application area for high performance polymers where reliability of systems and components is more essential than nuclear submarines.
Reliability and safety are paramount.
The nuclear propulsion operating environment places unique demands on the materials and components used in proximity to it. Determining how the amount of radiation encountered in each application affects the properties of polymers ranks as a key factor in material selection.
Under testing at high levels of rads, some plastic materials exhibit a steep drop in mechanical properties. The consequences are loss of strength and ductility, which indicates a high probability of failure under stress or impact loads.
In testing conducted and certified by the American Composites Manufacturing Learning Center, a comprehensive range of thermoplastic materials including Torlon PAI, PEEK and Ultem PEI were tested at exposure levels from 103 to 109 rads. Only a handful of materials exhibited satisfactory property retention at levels of 106 and higher. High strength Torlon 5030 PAI, a 30% glass-reinforced polymer extruded into shapes and machined into parts by Drake Plastics, successfully retained the required level of mechanical properties to pass the agency’s testing at 109 rads – the highest level used in evaluating polymer materials. Victrex PEEK, another Drake high performance stock shapes and parts polymer, also passed at 109 rads. 30% glass-reinforced Ultem 2300 PEI which Drake supplies in its unique and efficient Seamless Tube® configurations, demonstrated impressive property retention at 108 rads.
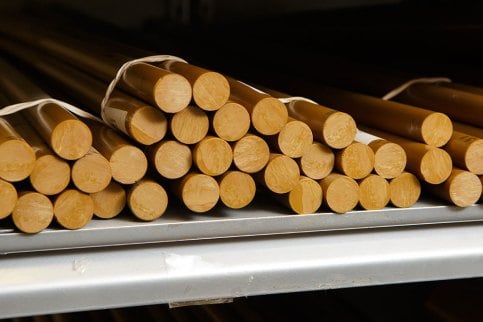
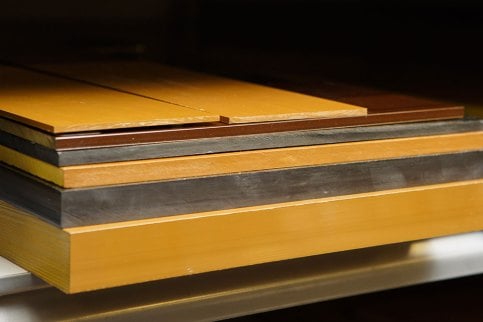
Along with its history of reliable performance in similar applications, its property retention under radiation exposure prompted the US Navy engineers to specify Torlon PAI in a number of designs from Drake Plastics for ball valve and tube seats for its nuclear submarines. With the material’s exceptional resistance to the effects of radiation, Torlon PAI delivers and retains the high compressive strength, toughness and wear resistance specified for these components.
Drake Plastics’ development team also met the US Navy’s challenge for a long-life material in a form that could be used for stern tube seals. The solution: Drake Seal Segments® produced from Torlon PAI. Today the Navy’s growing fleet of vessels relies on these arc-shaped seal components for their high compressive strength, toughness and long-term resistance to wear.
Other applications for Drake high performance polymer products in naval vessels include electrical connectors and receptacles machined from high strength and chemical-resistant Ryton R-4 PPS. The material provides excellent electrical and thermal insulation and isolation properties required for a variety of these components. Its chemical resistance is also notable, with no known solvents for the PPS material.
Drake High Performance Polymers In Military And Defense Components
- Portable missile fins machined from 30% carbon fiber reinforced PEEK are light weight, tough and rigid, contributing to weapons portability, reliability and accuracy.
- Radomes benefit from the dielectric properties, high strength and the higher temperature resistance of Solvay’s KetaSpire XT920 GF30 PEEK vs. the standard PEEK grade.
- Antennal mounts machined from Carbon fiber filled PEEK, used for its outstanding strength and electrical conductivity properties.
- Electrical connectors rely on the dimensional stability and isolation and insulation properties of Ryton R-4 PPS.
- Bushings and bearings machined from bearing and wear-resistant Torlon PAI and PEEK grades deliver reliable performance in aircraft and naval vessels.
- Auxiliary fuel tank and air connects machined from Torlon 4203 Seamless Tube® extend the flying range of fighter jets.
- Ball valve seats machined from Torlon PAI perform reliably long term in nuclear submarines and other naval vessels.
- Stern tube seals comprised of Drake’s Torlon PAI Seal Segments® serve the growing fleet of naval vessels.
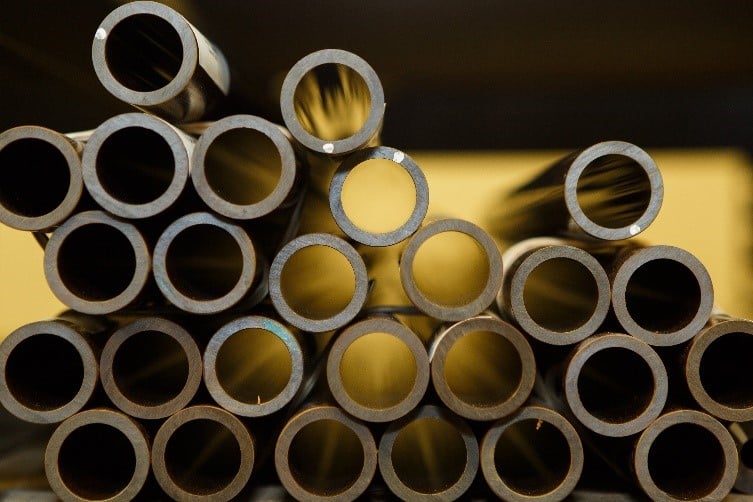
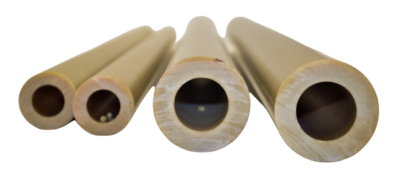