High-Performance Plastics for Life Science, Medical and Analytical Equipment Applications
High-performance thermoplastic materials bring a number of benefits to components and devices used in the diverse field of life sciences, medical and analytical laboratory equipment. Different categories of thermoplastics serve these widely varied applications. One category of materials comprises plastics that provide specific functional qualities for components that are contained within equipment or devices and have no direct human contact. Drake Plastics offers an impressive portfolio of ultra high-performance thermoplastics for these uses. They include several grades of Victrex® PEEK (polyetheretherketone), Solvay’s KetaSpire®PEEK, Torlon® PAI (polyamide-imide), AvaSpire® PAEK (polyaryletherketone) and Ryton® PPS (polyphenylene sulfide),as well as Sabic’s Ultem™ PEI (polyether-imide). These materials offer various combinations of high strength at temperature extremes, long-term wear resistance under dynamic load – in many cases without external lubrication, the ability to withstand aggressive chemicals, and excellent electrical properties. Victrex PEEK and KetaSpire PEEK, AvaSpire PAEK and Ultem PEI also exhibit remarkable resistance to extended exposure to steam and hot water.
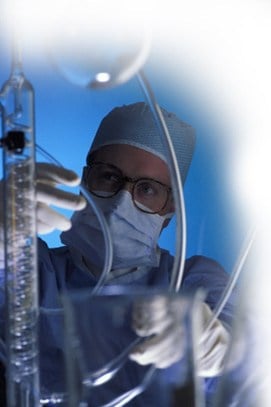
Another group of thermoplastics used in medical and life science applications falls under the term biocompatible materials. They fulfill stringent requirements for both implantable and non-implantable devices and components that have direct contact with the human body. These materials must adhere to rigorous compliance measures and certifications for their intended uses. Accordingly, Drake restricts activity in biocompatible and human implant materials including Solvay’s Zeniva PEEK and others to a dedicated operation that has the industry experience, knowledge, quality systems and procedures tailored to these specialized thermoplastics.
Standard High-Performance Thermoplastics in Non-Contact Applications
The functional benefits of Drake Plastics’ standard high-performance polymer materials include resistance to a wide range of chemicals, high strength and toughness even at temperature extremes, and electrical and thermal insulation and isolation properties. These thermoplastics also exhibit exceptional wear resistance for load-bearing components and moving parts such as gears, rollers, bearings, and bushings. They are used internally in many medical and analytical equipment applications where they are not exposed to bodily contact. For example, Drake Plastics machines its Torlon 4203 PAI (polyamide-imide) Seamless Tube® into highly wear-resistant rollers that provide long life in peristaltic pumps. Torlon 4275 PAI also affords long-term wear-resistance, high strength and the ability to maintain precise dimensions under temperature fluctuations in internal bushings used in prosthetics.
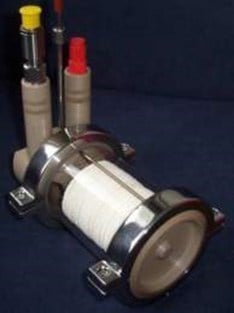
PEEK, recognized for its combination of strength, wear resistance and inertness in a vast number of chemicals, also serves many functional applications in medical, analytical and life-science equipment. Drake Plastics supplies various grades of Victrex® PEEK and Solvay’s KetaSpire® PEEK as extruded machinable shapes and machined and injection-molded components for these uses. Precision-machined bearings made from Drake’s 450FC30 PEEK rod combine high rigidity and lubrication-free wear-resistance for long term reliability in high-speed electric motors that power micro-surgery instruments. The application also serves to highlight the electrical properties typical of many Drake high-performance thermoplastics, an advantage behind their use in applications where electrical insulation and thermal isolation is important.
Drake extrudes Solvay’s high-temperature KetaSpire KT820 NT PEEK into rod, then machines precision-tolerance spacers that insulate and seal electrical components in electric motors contained within surgical apparatus.
High Temperature KetaSpire PEEK extends the inherent wear-resistance, chemical inertness and high strength of this high-performance polymer family into applications requiring a step up in thermal properties beyond what standard PEEK grades such as KetaSpire KT-820 and Victrex 450G can handle. High Temperature PEEK is available from Drake Plastics as stock shapes and precision-machined and injection-molded components. It also features higher strength compared to standard PEEK formulations.
Because of their exceptional chemical resistance and dimensional stability under temperature variations, Torlon PAI, PEEK, High Temp PEEK, Ultem PEI, Ryton R-4 PPS and AvaSpire PAEK are also specified for internal components in analytical equipment used in the life science field. Drake Plastics offers its array of materials as stock shapes and precision CNC-machined and injection molded parts to satisfy the diverse performance requirements of these applications effectively and efficiently.
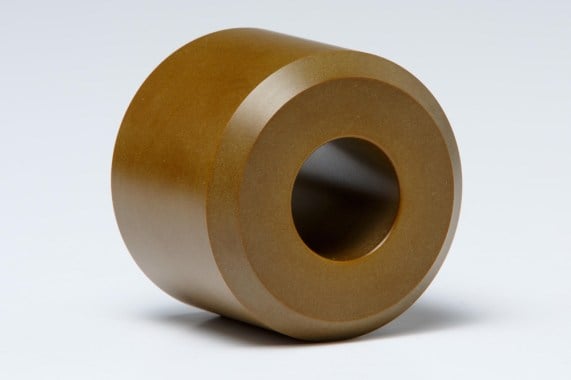
Drake Plastics is a recognized specialist in ultra high-performance polymers. Our decades of collaborative experience has helped engineers develop material selection and parts production solutions to numerous aircraft application challenges such as these.
Typical Applications: High-Performance Thermoplastics for Non-Body Contact Components
- Rollers in peristaltic pumps rely on high strength Torlon 4203 PAI for extended wear-resistance and long service life.
- Bearings used in micro-surgery instrument motors are machined from Drake’s 30% carbon fiber-reinforced PEEK 450FC30 rod for lubrication-free operation in these high-speed tools.
- Rotors and stators for HPLC (high-pressure liquid chromatography) equipment are injection molded in carbon-fiber PEEK for its chemical inertness and strength.
- Electrical spacers in surgical tool motors are machined from Drake’s Victrex KT820 NT PEEK rod. They provide insulation and sealing properties for the internal components.
- Prosthetic device bushings made from Drake’s Torlon 4301 PAI Seamless Tube® provide precision tolerances and wear resistance for internal components under dynamic load. Seamless Tube also reduces machining time and material loss vs. solid rod.
- Bearing cages used in high-speed dental drill motors rely on Torlon 4301 PAI and Torlon 4275 PAI for long service .
- Vacuum barrier stems for pharmaceutical bottle filling take advantage of PEEK’s chemical inertness, steam and hot water resistance and regulatory compliance for handling ingestibles.
- Analytical equipment components including fittings, valves, manifolds, seals, and ferrules are made from PEEK, Ryton PPS and AvaSpire PAEK for high strength and chemical inertness.
- High-speed robotic surgical tool bushings precision-machined from 30% carbon-fiber reinforced PEEK 450FC30 afford the strength and wear-resistance essential for reliable long-term performance.
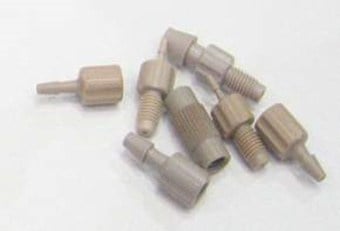
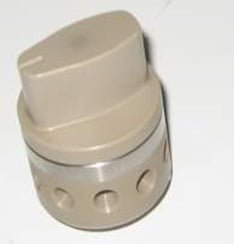
Biocompatible Plastics for Medical Devices
Biocompatible thermoplastics for medical devices in contact with internal human body tissue and fluids fall into these FDA regulatory classifications based on the cumulative sum of single, multiple or repeated contact time:
- Limited exposure: Materials for devices that have limited or short-term contact with internal tissue and fluids means their exposure time is limited to 24 hours or less. Plastics used in these applications are typically referred to in the industry as “medical grade plastics.”
- Prolonged exposure: This designation defines plastics for devices that can be in contact with internal tissue and fluids for up to 30 days.
- Long-term or permanent exposure: Devices and plastics defined as biocompatible for long-term or permanent exposure means they can be in contact with bodily tissue and fluids for more than 30 days.
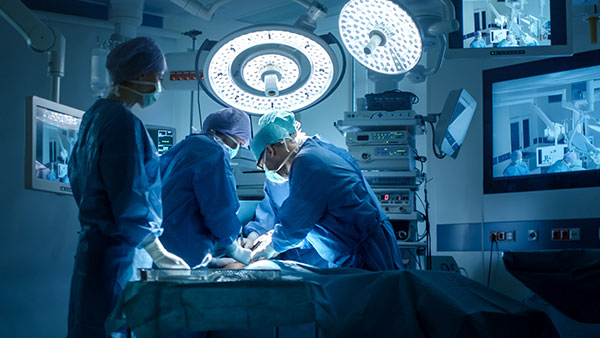
Plastics that meet the requirements for devices in the latter two categories are generally considered as implantable materials, with their level of biocompatibility defined by the duration of contact.
Some of the polymer families that Drake Plastics routinely extrudes, machines into precision parts or injection molds are grades that meet biocompatibility requirements for all three regulatory categories. DRAKE typically supports customers’ requirements for these specialized polymers through an association with a dedicated medical plastics manufacturing company located adjacent to Drake’s operations in Cypress, TX. That facility extrudes machinable shapes and produces precision machined parts and injection molded components from these biocompatible materials. It is an ISO 13485 registered company and can support site registration as required. The applications and process engineering teams also offer their expertise in medical device and materials regulatory requirements to facilitate product development projects.
Medical Grade Plastics
The spectrum of medical polymers gives device manufacturers the ability to specify a biocompatible material with the physical properties, sterilization resistance, cost and production options that best fit the requirements for each device.
Notable among medical plastics for limited or short-term exposure applications (up to 24 hours) are grades of KetaSpire and Victrex PEEK, AvaSpire PAEK, Radel PPSU, Udel polysulfone, Ixef PARA and Ultem PEI. All comply with industry regulatory standards and quality management protocols and most (if we include Ixef) are available as extruded shapes for precision machined parts or as injection molded components.
PEEK offers an unmatched combination of toughness, rigidity, inertness to a vast range of chemicals and resistance to multiple sterilization cycles. With a Tg (glass transition temperature) of 289°F (143°C) and a heat deflection temperature of 306°F (152°C), it retains its rigidity at thermal extremes. PEEK also holds precise dimensions over wide temperature variations.
KetaSpire PEEK from Syensqo (formerly Solvay), Victrex PEEK and Evonik’s VESTAKEEP PEEK are prominent tradenames for the resin, and all three serve short-term applications in the medical device industry worldwide. The opaque polymer is available from the resin manufacturers in natural off-white and custom colors.
Radel PPSU (polyphenylsulfide)
Syensqo’s Radel PPSU is well-recognized for its performance retention after hundreds of cycles in common sterilization methods. This has made it a leading material for re-useable devices where longevity translates to cost-effectiveness. It also offers high impact and mechanical strength and is inert to many chemicals and cleaners used in medical facilities.
Biocompatible grades of PPSU have common physical properties and differ mainly in their melt processing characteristics. Radel 5500 is often extruded converted into machinable shapes, while Radel 5100 and Radel 5800 are injection molding grades. The melt characteristics of Radel 5000 make it suitable for both extrusion and injection molding. All natural Radel PPSU resins have a transparent amber tint. Semi- opaque healthcare colors are also readily available.
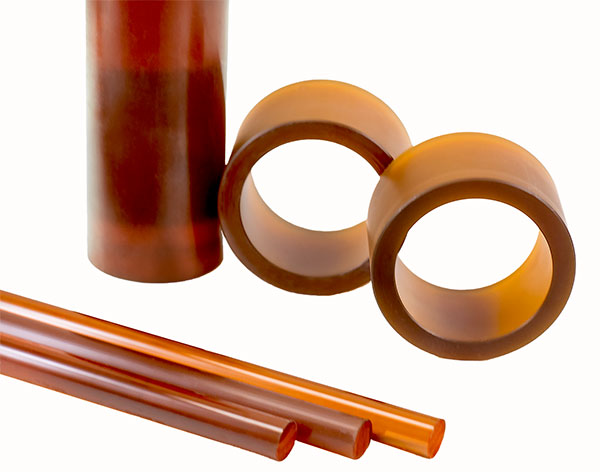
Two biocompatible Ultem PEI grades have been commercialized for medical devices. The properties of Ultem HU-1000 are comparable to standard Ultem 1000, and the material can be used in applications exposed to internal bodily contact for up to 24 hours. Ultem HU-1004 is a proprietary blend with higher impact resistance. It is also approved for contact up to 29 days. Both withstand repeated steam autoclave cycles, have excellent chemical resistance and maintain their high rigidity at temperatures up to 340°F (170°C).
The resins are available from Sabic, a global resin supplier, in transparent dark amber, black, and other custom opaque colors.
PSU (polysulfone)
A unique advantage of polysulfone among high-performance medical plastics is its transparency in thin cross sections. The material is almost water clear in thin-walled injection molded applications, a key factor behind its use in devices where visual observation of things like the physical position of a component or fluid flow need to be monitored and confirmed. Polysulfone is also available in custom tints and opaque healthcare colors.
Widely available as Udel 1700 from Syensqo, polysulfone withstands exposure to most healthcare chemicals and cleaners, and has good rigidity and toughness. Its resistance to hydrolysis and its temperature resistance up to 174oC (345oF) extend the re-usability of instruments and devices after repeated steam sterilization at 134oC (273oF). It is available in pelletized form for injection molding, and in the form of extruded stock shapes for machining into precision components and devices.
Syensqo’s AvaSpire PAEK is often considered an alternative to PEEK in components where the PEEK’s higher levels of chemical and thermal resistance are not required. Like PEEK and Ultem PEI, AvaSpire PAEK has the toughness and resistance to chemicals, steam and hot water to make it a candidate for multi-use surgical instruments that see repeated sterilization cycles. Available in natural off-white and custom opaque colors (PAEK is more easily pigmented than PEEK), typical applications include medical device handles, knobs, grips, retractors and instrument trays.
PARA (polyarylamide)
PARA is a versatile and cost-effective medical polymer for single-use devices. Reinforced with glass fibers, it imparts exceptionally high rigidity to hand-held instruments. Unlike many other fiber-reinforced plastics, it has a smooth high-gloss surface finish in injection molded components and devices.
Syensqo produces Ixef PARA in a range of standard gamma-stabilized colors that it supports with FDA Master Access File (MAF). The color options are especially useful for differentiating instruments in surgical kits. Devices made from the PARA withstand autoclaving and show no significant change in appearance or loss of mechanical properties from gamma sterilization.
Ixef PARA machinable semi-finished shapes
While PARA is generally considered a medical grade plastic for injection molding, technology now exists for extruding the polymer into stock shapes for machining. Drake can help MDMs source the shapes, which can be especially beneficial for prototyping and testing prior to finalizing injection molding tooling.
Implantable Plastics
Implantable plastics and devices are generally defined as those that have either prolonged exposure to bodily tissue and fluids (1 to 30 days), or for long-term or permanent implantation. Because of the critical nature of the applications, resin suppliers have set especially strict qualification protocol for availability of the polymers they offer for long-term or permanent contact devices.
DRAKE can provide medical device manufacturers with ready access to the processing capabilities and quality management systems required for converting implantable polymers into machinable extruded shapes, and precision machined and injection molded components. In addition to rod, implantable PEEK is also available to Medical Device Manufacturers in the form of film and thin sheet.
Implantable PEEK
Specialty implantable PEEK grades have had the leading role among high performance plastics for long-term implanted devices. The polymer has built decades of acceptance globally for its biocompatibility, regulatory compliance and physical properties, and its efficacy has been validated in a growing and diverse range of medical devices.
PEEK resin suppliers have committed significant resources to the manufacturing and quality systems and biocompatibility testing to gain the required approvals from regulatory agencies. The range of potential applications also continues to expand with new product technology that enhances the performance of implantable PEEK. Developments include PEEK grades compounded with additives or with surface treatments to achieve benefits such as reducing macrophage response, minimizing risk of infection, and promoting bone growth.
In addition to the availability of the implantable polymer from resin suppliers, implantable PEEK is also available in the forms of film, thin sheet and stock shapes for precision machined parts.
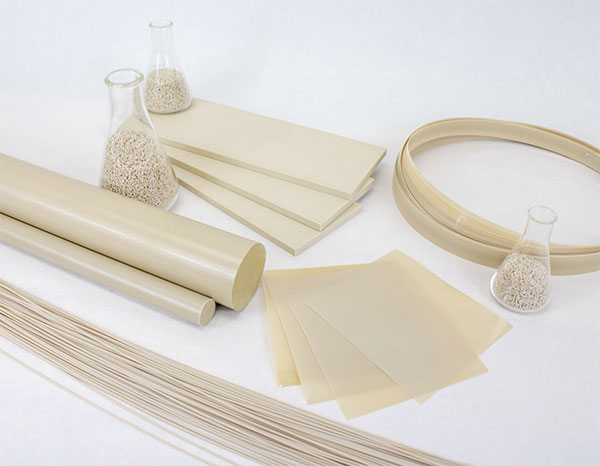
Implantable PEEK suppliers and brands
- Syensqo (formerly Solvay): Zeniva® PEEK resins
- Invibio Biomaterial Solutions: PEEK OptimaTM resins
- Superior Polymers: Magnolia PEEK resins
- Evonik: VESTAKEEP® Implant PEEK resins
- Genesis Medical Plastics: Genesis PEEK® machinable shapes, thin sheet and film
Implantable Sulfone Polymers
Syensqo, also in their Solviva® Biomaterials product line, has made the investment in facilities and regulatory approvals required to expand the options for implantable polymers beyond PEEK. Medical device manufacturers can add Veriva PPSU (polyphenylsulfone) and Eviva PSU (polysulfone) as material candidates for long-term implantable devices.
The polymers have performance profiles comparable to their medical grade Radel PPSU and Udel PSU counterparts. Both are available in opaque white and natural transparent tints. In fact, Eviva PSU and Veriva PPSU are the only transparent polymers that are implantable. The light tint of natural Eviva PSU is especially beneficial where clarity and transparency are important attributes for a device. Both polymers are available in pellet form for injection molded parts and as machinable shapes for precision machined components.
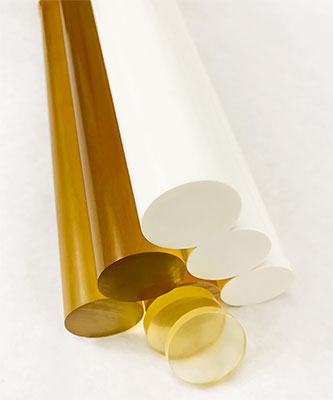
Typical Applications: Biocompatible Thermoplastics
Compared to metals and other traditional materials, biocompatible plastics can offer significant advantages in weight, manufacturability, cost, performance, and production consistency for specific medical devices. Material specifications are based on the specific requirements of each medical device. Typical applications include:
Medical Plastics for Limited Contact Devices (up to 24 hours)
- Repeat-use surgical instruments and surgical kits
- Probes and extractors
- Joint replacement sizing trials
- Short-term drug delivery systems
Implantable Polymers for Long-term / Permanent Contact Devices
- Spinal implants
- Drug delivery devices, valves and shunts
- Bio-electronic devices
- Cardiovascular and neurovascular devices
- Suture anchors
The ongoing development of improved implantable polymers and grades with performance-enhancing additives will extend the benefits to a growing list of devices.