Resolving Snowmobile CVT Clutch Roller Failures
When a major OEM experienced failures with rollers made from Vespel SP-1, , they turned to Drake for solutions. We provided machined prototypes and initial production from Torlon 4203L rod. For production cost reasons the OEM built a 4-cavity mold for Torlon with their legacy injection molding partner rather than continue with machining. Part failures continued, however, and the customer returned to Drake.
Drake’s engineers pointed out the critical factors behind the failures: The heavy sections of the part had a differential in cooling rate which negatively affected internal stresses, and the lower molecular weight of injection molding grade Torlon 4203L resin has inherently lower impact resistance than the extrusion grade. As a result, the heavy-walled molded parts could not withstand the high impacts that presented no problem for parts machined from tough and resilient extruded stock shapes.
Drake extrudes products from high molecular weight resins which have higher toughness, and we slow cool finished shapes to minimize residual stresses. Both factors helped resolve the performance issue. Drake then went to work on the cost difference first by making a custom diameter rod that matched the part OD. The machined part’s material efficiency then matched the injection molded version inclusive of the runner. Then Drake employed high speed machining that and approximated the injection molding production rate.
Result: Precision machined parts that perform, with a net cost equal to the injection molded version that would not work in this application.
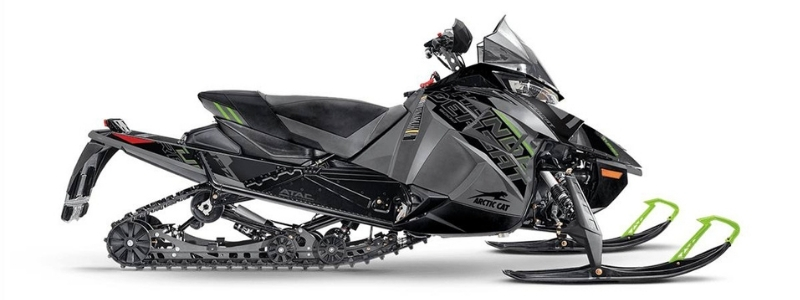