Polyamide-imide (PAI) Overview
Polyamide-imide is recognized as the highest performance melt-processable polymer available. Chemically it is part of the imide family of resins and is closely related to two other high temperature aromatic imide polymers: polyetherimide (PEI) and polyimide (PI). Polyimide differs however in that it cannot be melt processed in the form of extruded shapes and injection molded parts whereas PAI and PEI can.
Among ultra high-performance polymers, PAI offers exceptionally impressive strength under load at high temperatures. It maintains it rigidity even as it approaches its glass transition temperature (Tg) or softening point of 537°F (280°C) and resists deformation under static load over time with its superior compressive strength and creep resistance. Polyamide-imide’s resistance to wear, broad chemical resistance, and high energy radiation resistance, add to its extraordinary performance profile that makes it ideal for applications in the most severe service environments.
Suppliers, Products
Solvay, the world’s foremost producer of PAI resins, supplies a range of polyamide-imide formulations under the brand name Torlon® PAI. Commercial forms of polyamide-imide sold under the Torlon® name include pelletized grades for injection molding, and for extrusion and compression molding for the production of machinable stock shapes. The polymer resin is also available in powder form for use in high temperature adhesives, epoxies, coatings and composites.
A proliferation of applications and the desire for higher levels of physical properties led to the development of several performance-enhanced grades of PAI in the decades following the polymer’s commercial introduction in 1970.
Glass and carbon-fiber reinforced formulations were developed to increase strength at elevated temperatures, extending the application possibilities of PAI for structural components. These higher strength grades exhibit rigidity comparable to many metals, even under considerable repetitive mechanical loads and stresses at elevated temperatures.
Although inherently wear-resistant, formulations of PAI were developed with additives that enhance the polymer’s bearing and wear properties and extend the functional life of moving and rotating components under load. In many cases, the resultant improvement in wear resistance allows parts under dynamic load to function dependably long-term without the need for external lubrication. The benefits to equipment and machinery incorporating polyamide-imide components include lower maintenance and replacement costs, longer production runs, and elimination of the risk of contamination from lubricants.
The ability to melt process the diverse grades of polyamide-imide by extrusion and injection molding has led to countless applications for the ultra high-performance polymer. Drake Plastics supplies machining companies and distributors globally with unreinforced, fiber-reinforced and bearing and wear grades of PAI in an unparalleled range of extruded rod, plate and Seamless® Tube stock shapes sizes and configurations. The company’s investments in process technology have also led to the development of unique sizes and shapes that expand the application range of PAI. As examples, Drake offers the world’s largest PAI diameter rod with sizes up to 10.125 inches (257.275mm), and unmatched plate thicknesses to 4.0 inches (101.6mm). Drake also provides precision PAI components machined from its stock shapes and is widely recognized for its polyamide-imide injection molding capabilities.
Stock Shapes Supplied as Torlon® PAI, Drake PAI and Other Designations
Commercial practices for identifying PAI stock shapes differ among the limited number of dedicated manufacturers. Some use their own brand names for all PAI products. Drake Plastics’ stock shapes made from Torlon® PAI grades commercially available in pellet form for melt processing are identified with the Torlon® brand name.
Drake also supplies polyamide-imide products under the Drake PAI designation where commercial extrusion grades are unavailable for products that customers required. Where such products were required in the form of stock shapes, Drake developed technology to convert Torlon® PAI powder into the pelletized form necessary for extrusion. The investment was based on meeting ongoing customer demand for stock shapes in a specific grade when the extrudable pellet form of the resin was discontinued by the supplier.
Polyamide-imide products offered commercially under the Drake PAI designation include Drake 4200 PAI stock shapes. The formulation eliminates ionic impurities associated with titanium oxide used in standard PAI formulations and is required for components used in semiconductor manufacturing. Other examples are Drake PAI thin sheet and film, configurations for which standard resins for extrusion are unavailable.
Performance Attributes of Polyamide-Imide
High strength and dimensional stability at temperature extremes
One of the most notable features of PAI is its retention of very high flexural modulus and tensile strength at elevated temperatures well beyond the capabilities of all other thermoplastic materials. In fact, PAI is has greater strength and stiffness at 400°F (205°C) than most engineering plastics at room temperature. It also retains its properties extremely well after long-term exposure to high temperatures.
Compared to many metals, polyamide-imide grades reinforced with carbon or glass fibers demonstrate equivalent stiffness and rigidity at a substantially lower weight. This is a compelling reason for their use as a replacement for metals in aerospace and defense applications, for example, where light weight and structural strength at high temperatures are priorities for both performance and economics.
At the opposite temperature extreme, PAI exhibits greater impact resistance and toughness at cryogenic temperatures where most other high strength polymers become extremely brittle and ultimately fail.
PAI also affords excellent dimensional stability over wide temperature swings. Glass and carbon-reinforced grades in particular exhibit a very low CLTE (coefficient of liner thermal expansion), comparable to that of aircraft grade aluminum.
Compressive Strength and Creep Resistance of PAI
Polyamide-imide maintains its exceptionally high compressive strength and resists creep under load at elevated temperatures. In fact, under high static load, unreinforced grades of PAI resists creep that can cause compression set in other high-performance thermoplastics reinforced with glass or carbon fibers. Its elastic recovery behavior and compressive properties combined with its toughness across a broad temperature span have resulted in the extensive use of various polyamide-imide grades in applications such as seal rings, hydraulic poppets, brake tappets, check balls, thrust washers, and compressor plates. Reinforced and lubricated grades of PAI raise the level of performance for sealing components that require higher strength and wear resistance.
PAI Thermal Conductivity
Applications requiring thermal isolation and insulation such as heat shields benefit from the low thermal conductivity of polyamide-imide. PAI housings and panels are often used to protect critical internal components from high temperatures that can affect the accuracy of sensitive instrumentation.
Electrical Properties of Polyamide-Imide
Most PAI grades offer excellent electrical insulating properties, and specific grades offer higher levels of perfomance than others. Grades offered commercially as Torlon 4203L and 5030 PAI in particular offer exceptional dielectric strength and high volume and surface resistivity. However, certain wear-resistant grades contain graphite. While they show high resistivity properties according to standard test methods using direct current, they can exhibit some conductivity at higher voltage and frequency levels.
One carbon-fiber reinforced grade designated Torlon 7130 PAI in fact is conductive, an asset for use in applications requiring shielding against electromagnetic interference.
Because they can be injection molded into intricate configurations and are dimensionally stable in close-tolerance machined parts, a number of polyamide-imide grades are used extensively for precision electrical and electronic components requiring superior insulation and isolation capabilities.
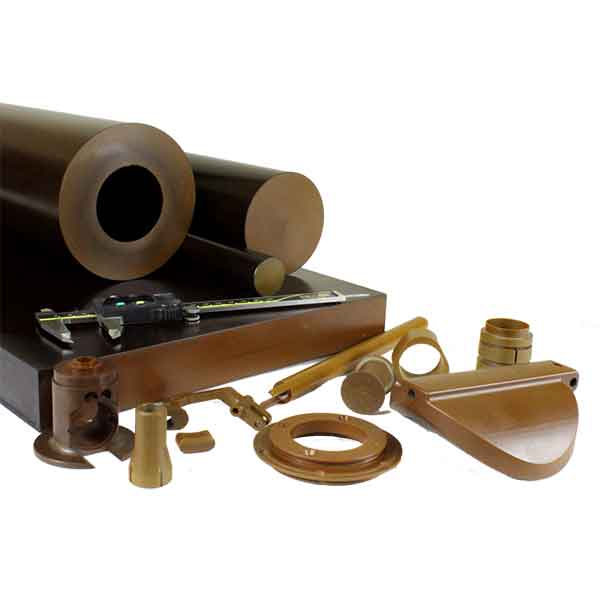
Chemical Resistance of Polyamide-Imide
PAI is virtually unaffected by most acids, aliphatic and aromatic hydrocarbons and chlorinated and fluorinated hydrocarbons at moderate temperatures. The polymer, however, may be attacked by saturated steam, strong bases, and some high-temperature acid systems.
Post-curing PAI shapes and parts after melt processing by extrusion or injection molding optimizes both their chemical resistance and wear resistance. For this reason, Drake Plastics post-cures all its extruded PAI stock shapes and injection molded parts. For polyamide-imide applications that require the highest level of chemical resistance, machined parts can be post-cured a second time to ensure optimal performance.
PAI Resistance to Gamma Radiation Exposure
Few thermoplastics offer the resistance to physical property degradation that PAI affords.
Many polymers exhibit a sharp drop in mechanical properties at exposure levels as low as 103 rads. PAI however demonstrates exceptional stability under gamma radiation at far higher levels of exposure. In certified agency tests at 109 rads, the highest level tested, a 30% glass-reinforced grade of PAI retained 95% of its mechanical properties after long-term exposure. Its performance was a major factor in the specifications for PAI as a material for applications in the field of nuclear energy, including components used in the US Navy’s nuclear submarines.
Flammability and Smoke Generation of Polyamide-Imide Grades
Certified ratings based on tests performed by major agencies and laboratories worldwide validate the suitability of polyamide-imide for electrical, electronic, aerospace, and other applications where flammability is an important factor. Most commercially available PAI grades carry impressive flammability ratings from these agencies. Two commercial grades available in the form of injection molded parts and machinable stock shapes as Torlon 5030 PAI and Torlon 7130 PAI surpass the FAA’s flammability, smoke density, and toxic gas emission requirements for use in commercial aircraft.
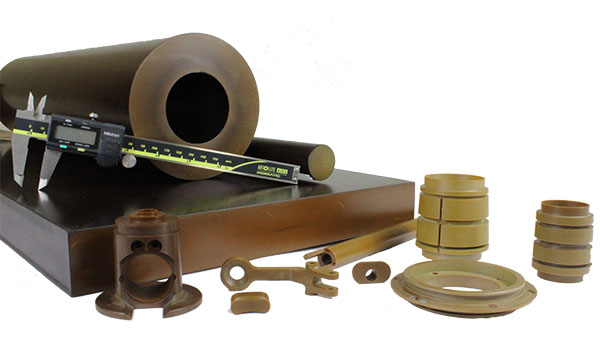
PAI Typical Applications
Since the polymer’s introduction, the development of multiple grades of PAI with different performance profiles has spurred a wide range of applications. All are characterized by having to withstand long term exposure to various combinations of extreme temperatures, high static and dynamic loads and aggressive chemical environments. Many applications also rely on polyamide-imide’s electrical and thermal insulation and isolation properties.
With these attributes, the family of PAI formulations has proven very effective in meeting these ultra high-performance requirements in bearing and wear, sealing, structural and thermal and electrical components where other engineering materials have failed. A partial list of uses in major industries includes components for aircraft, space shuttles and satellites, automotive transmissions, metal processing and plasma cutting tools, down-hole oil and gas exploration, alternative energy and battery storage applications, and military and defense weapons systems. The high dimensional stability, chemical resistance and low out-gassing of PAI are behind its use in semiconductor wafer handling applications, test sockets and nests. A machinable stock shapes grade developed by Drake without TiO2 and designated Drake PAI 4200 also resolves concerns about titanium contamination in semiconductor processes.
Polyamide-Imide Processing Challenges and Post-Curing Benefits
PAI is recognized throughout the industry as a challenging material to extrude and injection mold. The inherent characteristics of PAI necessitate a high degree of processing expertise to achieve the polymer’s optimum properties in extruded shapes and machined and molded parts.
Among the processing challenges are its high glass-transition temperature or softening point (Tg), its highly sensitive shear rate and parameters for controlling melt viscosity, and a narrow processing range at temperatures in excess of 600°F (315°C).
Polyamide-imide is also highly moisture-sensitive. Pre-drying is essential, and process conditions must be rigorously monitored and maintained to prevent moisture from degrading its molecular weight and physical properties.
After processing, polyamide-imide requires extended thermal post-curing over a precisely-staged temperature cycle up to 500°F (260°C). When properly implemented, this essential step completes the imidization process and advances the molecular weight of PAI to a level that achieves its optimum properties.
Capacity to Serve Growing Demand for PAI Stock Shapes and Parts
Since the commercial introduction of polyamide-imide in 1970, a limited number of dedicated companies have emerged as recognized specialists in extruded and molded PAI products. Drake in particular continues to make ongoing investments in product and process development and sustains ample capacity to support its customers’ growing demand for prompt and dependable supply of polyamide-imide stock shapes and parts worldwide.