What are Thermoset Composites?
Thermoset composites consist of a matrix of reinforcing materials impregnated with a thermoset resin such as epoxy, phenolic or polyester. The reinforcing materials typically comprise over 50% of the composite’s volume, and impart performance characteristics specific to the fiber or fabric. Among the most common are cotton, glass, aramid, and carbon fibers, as well as fabric woven from various materials. Other additives and solid lubricants can be integrated into the matrix to enhance performance. The resulting composite is processed under high temperature and pressure to produce plate, tube and rod in various sizes for machining into finished parts.
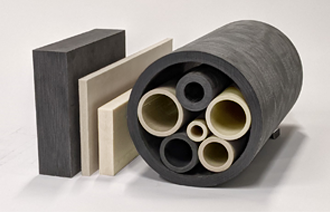
During processing, the forming temperature cross-links the thermoset resin’s polymer chain. Cross-linking, coupled with the properties of the other components, creates a composite with high compressive strength, corrosion and wear resistance, load-bearing properties at high temperatures, and other characteristics specific to the composition.
Differences Between Thermosets and Thermoplastics
Like thermoplastics, the variety of resins and additives that can be combined in a thermoset composite affords a diverse range of physical properties. Unlike thermoplastics, thermosets cannot be melt-processed by injection molding or extrusion, or re-melted and re-processed. The cross-linking that occurs during curing permanently “sets” the composite in the form in which it is produced. As a result, the manufacturing process for composites cannot reproduce complex designs possible with injection molding, and is best suited to making simple three-dimensional shapes such as rods, tubes and plates that are machined into components.
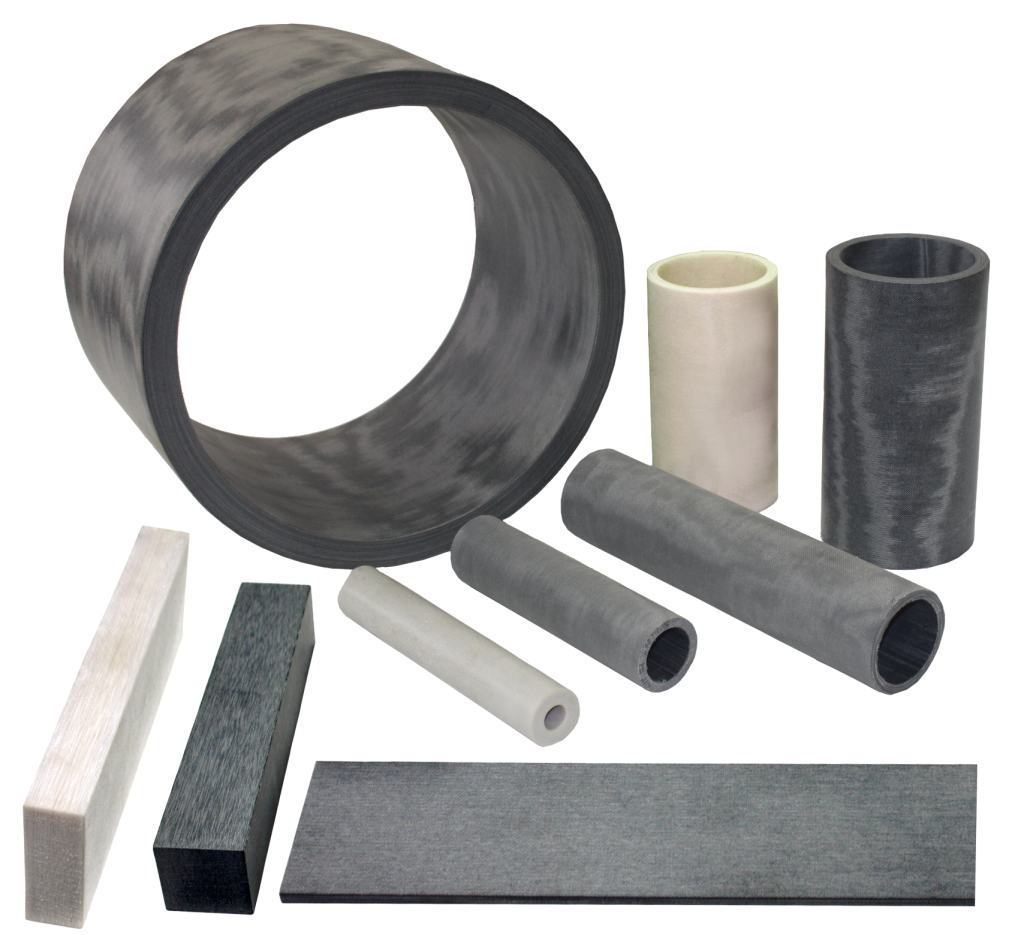
Versatile Range of Bearing and Wear Properties, Electrical and Thermal Isolation, Chemical Resistance and Working Temperatures
"*" indicates required fields
Drake Thermoset Composites and Capabilities
Drake offers advanced thermoset composite shapes in several forms, and has versatile capabilities for precision-machining the full spectrum of traditional commercially available composite materials as well as Drake’s HTT high performance composite products.
Drake Thermoset Composite Shapes
Depending on the grade, Drake’s thermoset composite shapes offer working temperatures that range from -40° C up to 204° C (-40° F to 400° F), high bearing and wear resistance, impressive compressive strength, thermal and electrical insulation and resistance to corrosion and chemicals.
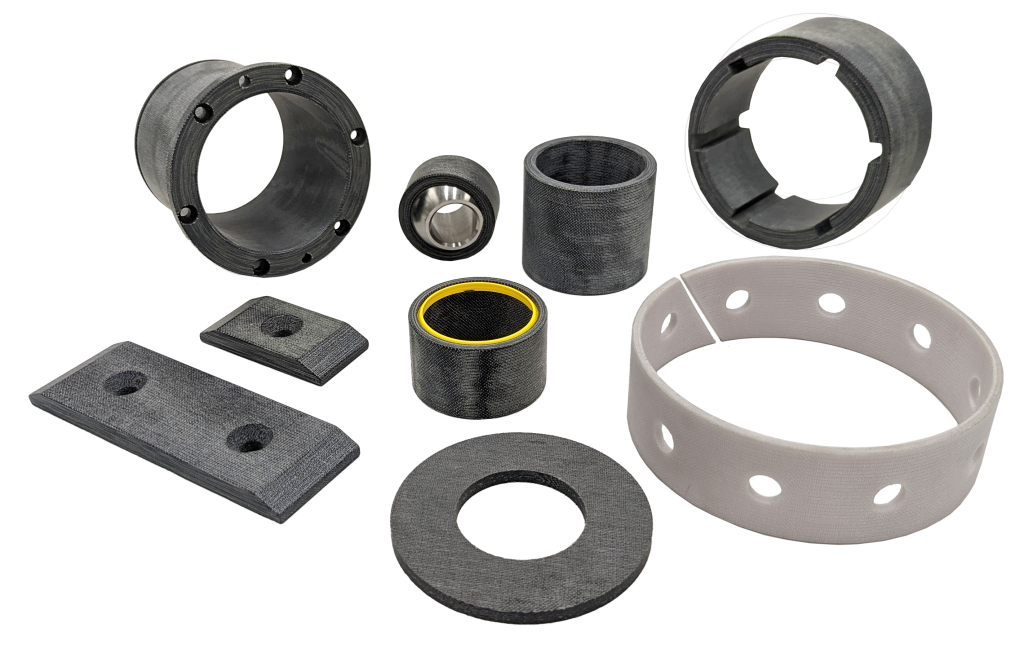
- High temperature structural grade: high compressive strength; electrical and thermal insulation
- Operating temperature range: -40°F to 400°F (-40°C to 204°C)
- Composition: high temperature thermoset resin with woven meta aramid fiber that is also used for welding blankets and fire retardant protective clothing.
- High-temperature self-lubricating bearing and wear grade: Dynamic CoF (dry): 0.13-0.15
- Operating temperature range: -40°F to 400°F (-40°C to 204°C)
- Composition: High temperature thermoset resin with woven aramid fiber, MoS2 and PTFE
- Self-lubricating standard bearing and wear grade: dynamic CoF (dry): 0.05-0.10
- Operating temperature range: -40°F to 200°F (-40°C to 93°C)
- Composition: High performance thermoset resin with woven textile, MoS2 and PTFE
- High temperature epoxy and glass-fiber fabric rolled and molded into desired MG-10 rod diameter
- Balls machined from MG-10 rod have a high level of isotropic properties
- Isotropic behavior eliminates failure-prone anisotropic properties of balls machined from sheet or plate laminate lay-ups.
- Composition: high-temperature epoxy / glass-fiber fabric