KetaSpire PEEK XT-920 significantly raises the upper temperature limit of traditional PEEK, opening new applications in injection molded and machined components for this ultra high-performance family of polymers.
With the same 2:1 ratio of ether (E) to ketone (K), high temperature PEEK XT exhibits the same exceptional chemical resistance as traditional PEEK. This polymeric structure also affords resistance to a broader range of chemicals compared to polyketones such as PEK, PEKK, PEKEKK and PAEK that have somewhat different ether-to-ketone ratios.
While comparable to PEEK in chemical resistance, the unique chemistry that led to the development of PEEK XT elevates its glass transition temperature to 170°C (338°F), or 20°C (36°F) higher than prior grades of PEEK including KetaSpire KT820 NT and Victrex 450G.
Components injection molded or machined from KetaSpire PEEK XT also retain their strength at high temperature extremes. Based on properties data from Solvay who produces KetaSpire PEEK polymers, the XT grade has a 400 percent greater tensile modulus and approximately 50 percent more tensile strength at 160°C (320°F) over traditional PEEK. It also offers improved dielectric strength and volume resistivity, making it a solid candidate for high temperature electrical applications.
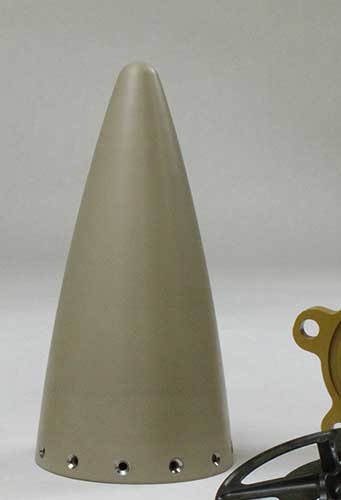
PEEK XT Grades for Injection Molded Components
Solvay offers KetaSpire PEEK in three grades: unreinforced PEEK XT-920, and 30% carbon-fiber reinforced KetaSpire XT-920 CF30 and 30% glass-reinforced KetaSpire XT-920 GF30. The fiber-reinforced formulations provide more structural strength for applications that must withstand high loads and pressures.
Injection Molding Technology for Reinforced and Unfilled PEEK XT Polymers
Customers recognize Drake Plastics’ expertise in developing the tooling, process conditions and equipment configurations for advanced polymers that yield injection molded parts with precision tolerances, minimal stress and optimum performance. XT920 is processed at much higher temperatures than PEEK, and its processing window is narrower. Precise process design and control are key factors to achieving the higher-level properties of KetaSpire XT PEEK grades, and even more so for the 30% glass or carbon fiber reinforced formulations.
Melt flow analysis as a roadmap:
Drake Plastics’ laboratory has the analytical tools to determine the polymers’ melt flow characteristics as a guide to the best processing parameters and tool design for each PEEK XT grade.
Our tooling technicians use the information for gating design to achieve fiber orientation that optimizes the strength of molded components. The analytical data also defines the process conditions that will preserve the inherent properties of each PEEK XT grade.
Molding technology optimizes performance and quality:
Drake Plastics uses all-electric molding machines that operate consistently and efficiently, and eliminate the risk of hydraulic leaks or spills.
Our engineers size barrels to each polymer, to minimize time at temperature during molding. This avoids degradation of the polymer in the melt phase and ensures maximum properties and consistency of each molded piece.
Drake Plastics’ investment in RJG control systems further contributes to consistent quality and performance in PEEK XT-920 injection molded components. The equipment monitors conditions in the mold cavity and maintains ideal process temperatures and pressures for each PEEK XT-920 grade.
High-temperature PEEK XT applications include large components with heavy wall thicknesses that can be subject to surface sinks or internal voids when molding. Drake Plastic’s injection molding machines are equipped with compression capabilities that allow heavy walled parts to be consolidated during the cooling cycle. This post- injection sequence compresses or “coins” the part inside the mold to yield heavy-walled parts with no voids or porosity.
Versatile size range:
Machine sizes between 35 and 300 tons provide customers with a range of injection molded components from 0.85 grams (0.03 oz.) to 567 grams (20 oz.). This capability serves the diverse array of oil and gas industry equipment applications from precision electrical components to large valves and seals.
KetaSpire High Temperature PEEK XT Applications
The three grades of KetaSpire XT-920 are ideal for components exposed to temperatures over the Tg of traditional grades of PEEK where they rapidly lose strength and stiffness, and their thermal expansion rate increases dramatically. Electrical insulation properties are also diminished dramatically at temperatures over a polymer’s Tg.
NORSOK M710 sour gas testing demonstrated the polymer’s capabilities for applications in downhole environments. After 50 days’ exposure to 20% H2S at 230°C and 14 days’ brine/HC exposure at 300°C, PEEK XT performed comparably to traditional PEEK, a material with worldwide recognition for reliability in oil and gas equipment components.
Typical applications that can utilize PEEK XT as a higher temperature upgrade to traditional PEEK include valve seats, seals and back-up seal rings, electrical connectors in ESPs, bobbins, coils and radomes.
Prototypes and Components Machined from KetaSpire PEEK XT Stock Shapes
Drake Plastics extrudes all grades of KetaSpire PEEK XT-920 into stock and custom sizes of machinable rod and plate. Our CNC machining operation routinely converts these stock shapes into prototypes for testing and validating component design and performance prior to investing in injection molding tooling. We also assist customers with production quantities of machined parts should they be needed before production tooling is finalized.
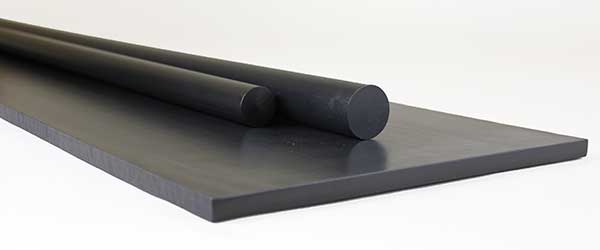